Капитальный ремонт ДВС – как это делается сегодня?
Современные технологии позволяют выполнить капитальный ремонт ДВС и восстановить даже самые безнадежные моторы.
В нашей предыдущей статье мы писали о том, что в связи с экономическим кризисом и подорожанием импортных запасных частей вновь становится актуальным и экономически целесообразным капитальный ремонт двигателей внутреннего сгорания (ремонт ДВС). В этой статье мы расскажем об основных методах и технологиях, которые применяются при восстановлении поврежденных и изношенных частей двигателя.
Перед проведением капитального ремонта двигателя автомобиля выполняют его полную разборку, после чего все детали моют и дефектуют. Это является обязательным условием для обеспечения высокого качества результата ремонта ДВС, так как продукты износа и части поврежденных деталей могут попасть в рубашку охлаждения или перекрыть масляный канал, что приведет к повторному выходу из строя отремонтированного двигателя.
Блок цилиндров
Расточка блока цилиндров
Изношенные или поврежденные стенки цилиндров растачивают до ремонтного размера и используют поршни и поршневые кольца большего диаметра. Но такой способ ремонта ДВС применим только для моторов, завод-изготовитель которых при конструировании сделал запас, позволяющий выполнить расточку блока цилиндров.
В гильзованных блоках цилиндров гильзы выпрессовывают и устанавливают новые. Ремонт ДВС, для которых производитель этого не предусмотрел, выполняется следующим образом: сначала необходимо расточить цилиндр, а далее запрессовать чугунную гильзу с диаметром под стандартный поршень для каждого отсека. В случае если блок цилиндров ремонтируемого двигателя автомобиля изготовлен из алюминиевого сплава и имеет небольшую толщину стенок между цилиндрами, то чугунная гильза еще и усиливает конструкцию.
Деформированные при перегреве поверхности блока и головки шлифуют на станке, прокладку при этом подбирают такой толщины, чтобы не изменилась степень сжатия.
Коленвал и шлифовка
Поврежденные постели коленвала ремонтируемого двигателя автомобиля восстанавливают обработкой на горизонтально-хонинговальном станке. При этом снимают очень тонкий слой металла и обеспечивают идеально ровную ось вращения, что является очень важным условием, так как в противном случае на вал будут действовать неравномерные нагрузки, которые могут привести к его заклиниванию или поломке и полном отказе отремонтированного ДВС.
Дефектовку коленчатого вала проводят как визуальным осмотром и измерениями, так и с помощью различных технических средств. Довольно интересным методом проверки коленвала является
- коленчатый вал устанавливают на две опоры с обмотками разных полярностей;
- на поверхность наносят специальное масло;
- после коленвал посыпают металлическим порошком.
Магнитное поле, которое создается при прохождении тока через вал, позволяет обнаружить скрытые трещины вала, т.к. над ними характерно выстраиваются частицы порошка.
Обнаруженные неглубокие повреждения на шейках устраняют шлифовкой коленвала, при этом для ремонтируемого ДВС подбирают вкладыши необходимых размеров. Если оригинальных ремонтных деталей нет, то их заменяют на неоригинальные, а иногда изготавливают самостоятельно под требуемые размер.
При ремонте двигателя автомобиля изгибы коленчатого вала правят на специальном прессовом оборудовании. При большом износе шеек на них наваривают ленту, изготовленную из высокопрочного сплава, после чего коленвал шлифуют под размер вкладышей. В такой же способ восстанавливают поврежденные от выработки поверхности под сальниками. Во время ремонта ДВС восстановлению подлежат также и сломанные шпоночные соединения.
Описанный метод не применяют для коленчатых валов дизелей, т.к. они работают при более высоких нагрузках, которые приходятся на детали кривошипно-шатунного механизма. Покупать новый коленвал придется только в случае наличия на нем больших трещин.
Поршневая группа – замена поршней?
При капитальном ремонте двигателя автомобиля замена поршней может быть необязательной, если остаточная толщина их стенок и днища позволяет выполнить восстановление. Однако производители поршней не предоставляют ремонтных размеров и предприятия, которые специализируются на ремонте ДВС, могут рассчитывать только на свой личный опыт.
На поврежденном от удара о клапан днище поршня делают цековки. Если не удается найти кольца подходящего размера для поршня ремонтируемого двигателя автомобиля, то под них немного растачивают канавки.
Не заменяя поршней, на прессовом станке выравнивают и сами шатуны, а под поршневой палец устанавливают новую втулку.
ГБЦ
Проверку головки блока цилиндров (ГБЦ) выполняют так же, как и самого блока – в опрессовочной ванне. Для того чтобы расширились скрытые трещины, в нее наливают горячую воду, после чего закрывают все технологические отверстия и под избыточным давлением подают воздух в рубашку охлаждения. В случае наличия трещин в соответствующем месте будет видно пузырьки воздуха.
Восстановление ГБЦ, как и блока цилиндров, выполняют при помощи сварки. После чего вновь проводится проверка головки блока ремонтируемого ДВС в опрессовочной ванне.
Другие возможные технологические операции при капитальном ремонте двигателя автомобиля:
- Направляющие втулки клапанов меняют на ремонтные (если такие есть) или изготавливают самостоятельно.
- Чрезмерно изношенные седла клапанов растачивают, а на их место запрессовывают новые.
- Изогнутые распредвалы выравнивают на прессовом станке. Как правило, трещин на них не бывает.
- Постели, как и в блоке цилиндров, растачивают на специальном станке. После чего на опорные поверхности валов наваривают ленты металла и выполняют шлифовку.
Разработанные за долгое время технологии ремонта позволяют восстановить практически любой двигатель с повреждениями самой разной сложности. Но не стоит забывать, что капитальный ремонт – дело не дешевое и прежде чем начать выполнение работ, необходимо провести экономические расчеты, ведь возможно гораздо дешевле будет приобрести новый силовой агрегат.
info-parts.ru
Ремонт двигателя: когда он нужен?
Автовладельцы рано или поздно сталкиваются с ремонтом двигателя. Это трудоемкая и недешевая операция, но благодаря ей транспортное средство проработает еще очень долго. В данной статье мы рассмотрим основные причины поломки двигателя, а также способы его ремонта.
Ремонт двигателя бывает капитальным, либо выполняется переборка. В первом случае агрегат восстанавливается до максимально приближенных к заводским параметров, во втором – производится замена изношенных или неисправных деталей.
Почему изнашивается двигатель?
Двигатель является наименее надежным и долговечным среди всех агрегатов автомобиля. Даже несмотря на то, что агрегату уделяется больше всего внимания в процессе эксплуатации, он все равно первым выходит из строя. Это связано с тем, что ДВС работает при высоких нагрузка и температурах, механическом и химическом воздействии.
Износу наиболее подвержены поршни, поршневые кольца, клапаны, цилиндры, коленчатый вал, шатунные и коренные вкладыши коленвала. Именно ресурс этих деталей определяет долговечность двигателя. При их износе или неправильном расположении возникает необходимость в разборке и ремонте ДВС.
На работу силового влияют и другие детали, но при их ремонте или замене не требуется полная разборка двигателя.
Срок службы ДВС зависит не только от условий эксплуатации, но и от качества его компонентов. Поэтому очень важно при ремонте силового не использовать дешевые запчасти, так как они могут очень быстро износиться и полностью вывести его из строя.
Когда следует ремонтировать двигатель?
Ресурс ДВС определяется по пробегу или моточасам и составляет в среднем 150-250 тыс. км. По истечению ресурса происходит снижение характеристик и мощности двигателя, и ему требуется заменить основные детали. Существуют силовые агрегаты, ресурс которых может достигать 1 млн. км, но в последнее время такие двигатели являются большой редкостью.
Признаками необходимости ремонта ДВС являются:
-
Высокий расход масла на 1000 км
-
Повышенный расход топлива
-
Снижение мощности
-
Нагар и масло на свечах накала
-
Посторонние стуки при работе
-
Частый перегрев
-
Низкое давление масла в системе
-
Нестабильная работа ДВС
-
Падение компрессии в цилиндрах
-
Механические повреждения
-
Попадание большого количества газов в картер
При обнаружении таких проблем следует незамедлительно продиагностировать состояние автомобиля в сервисном центре. После этого существует два варианта развития событий: замена изношенных деталей или полноценный ремонт.
Выделяют регламентный, внеплановый и капитальный ремонт. В первом случае производится замена деталей на новые согласно рекомендациям автопроизводителя. При внеплановом ремонта двигатель еще имеет определенный ресурс, но по каким-то причинам вышел из строя. Капремонт выполняется как по регламенту, так и после полной поломки.
Но в некоторых случаях ремонт двигателя можно не делать. Например, если неполадки в системе питания и управления, опорах двигателя, коробки передач, системе выпуска отработавших газов и т.п. принимаются за неисправность в механической части ДВС. Такие неисправности устраняются без капремонта.
Помимо этого, особенно внимательным нужно быть и в автосервисах, где недобросовестные сотрудники пытаются заменить исправные детали под предлогом капремонта.
Что такое капитальный ремонт?
Подводя итог под вышесказанному, можно сделать вывод, что капремонт целесообразен только тогда, когда приведенные выше проблемы проявляются комплексно, а не по одной.
Условно ремонт двигателя делится на несколько этапов.
После того, как двигатель разобран и очищен, выполняется его дефектовка. В эту процедуру входит проверка износа определенных деталей, проверка дефектов головки и блока цилиндров, оценка выработки, измерение зазоров и т.д. В конечном итоге собранные данные о состоянии зазоров и деталей сравниваются с заводскими допусками.
Затем составляется список деталей под восстановление и замену на новые. Например, для ремонта головки блока цилиндров потребуется замена направляющих втулок клапанов и реставрация их седел, шлифование плоскости головки, устранение трещин, замена маслосъемных колпачков, клапанов и гидрокомпенсаторов, замена или восстановление толкателей, распредвала и т.п.
Некоторые компоненты, например, поршни двигателя, можно восстановить, однако успешность этой операции будет зависеть от наличия задиров на поверхностях.
Многие автопроизводители при сборке ДВС обращаются к антифрикционным твердосмазочным покрытиям (АТСП).
Серия антифрикционных покрытий MODENGY для деталей ДВС применяется при массовом производстве поршней
Подобными материалами обрабатываются вкладыши, юбки поршней, штоки клапанов, шлицевые соединения, вкладыши коленвала и распредвала, дроссельные заслонки и другие детали.АТСП позволяют облегчить приработку, снижают износ и трения, предотвращают задир поверхностей и т.д.
Однако со временем защитные покрытия истираются, происходит снижение характеристик двигателя. Определить исчезновение по косвенным признакам не получится, для этого нужно разобрать двигатель и осмотреть поршни или другие детали, где АФП было нанесено. Элементы, которые ранее обрабатывались подобными покрытиями, будут несколько темнее тех, на которых покрытий не было.
Но потеря покрытия не приговор, и его можно восстановить. Одним из материалов для таких целей является антифрикционное твердосмазочное покрытие MODENGY™ Для деталей ДВС. Основу материала составляет дисульфид молибдена и графит, которые распределены в полимерном связующем.
Данное покрытие отличается высокими эксплуатационными характеристиками и удобством применения:
Широким диапазоном рабочих температур
-
Возможностью отверждения как при комнатной температуре, так и при нагреве
-
Низким коэффициентом трения
-
Видимым эффектом после применения: снижается расход топлива, износ и трение, уменьшается шум от работы ДВС, предотвращаются задиры, повышается КПД двигателя
В комплексе с покрытием рекомендуется использовать Специальный очиститель-активатор MODENGY™. Он не только очищает поверхности, но и обеспечивает наилучшую адгезию покрытия к основанию.
Детальную видеоинструкцию по обработке поршней покрытием MODENGY™ смотрите ниже.
Для ремонта блока цилиндров требуется хонингование и расточка. Они нужны для установки новых деталей: ремонтных поршней, шатунов, поршневых колец и т.д. Можно также произвести гильзование блока цилиндров. Если в БЦ были обнаружены трещины, то они устраняются, заменяются вкладыши, восстанавливается изношенная постель коленвала, выравниваются привалочные плоскости. В это же время выполняется ремонт или замена самого коленчатого вала.
На последнем этапе двигатель собирается и проверяется перед установкой. Затем производится пробный запуск, необходимый для приработки новых деталей. В это же время оценивается работа отремонтированного ДВС, выполняется настройка и регулировка систем питания и зажигания, механизма ГРМ и т.д.
Что выбрать: контрактный двигатель или капремонт?
Все чаще автовладельцы вместо ремонта выбирают установку контрактного двигателя. Обусловлено это тем, что такой ДВС стоит дешевле, чем ремонтные работы.
Но следует помнить о том, что такой двигатель уже стоял на другом автомобиле. Поэтому возникают такие нюансы, как родной пробег, общее состояние и оставшийся ресурс ДВС. Помимо этого, при постановке транспортного средства на учет могут возникнуть определенные проблемы из-за контрактного двигателя.
Рассматривать покупку контрактного ДВС следует в том случае, если замена двигателя необходима очень срочно, приобретение новых деталей затруднительно ввиду их редкости, высокой стоимости или других причин, имеющийся агрегат сильно поврежден и не подлежит восстановлению.
Но в основном контрактный двигатель покупают лишь потому, что он в 1,5-2 раза дешевле, чем капитальный ремонт. Но исправный агрегат не может стоить дешево, поэтому приобретать подобный ДВС, хоть и по привлекательной цене, не стоит.
Правила эксплуатации автомобиля после капремонта двигателя
После проведения ремонтных работ над двигателем следует соблюдать определенные требования. Это обусловлено тем, что новым деталям нужно правильно приработаться, что позволит отремонтированному агрегату проработать достаточное количество времени. В особенности это важно для современных высокотехнологичных ДВС с турбонаддувом.
Такие моторы изготавливаются из алюсила, никосила и подобных мягких сплавов, что является одной из причин их малого ресурса – до 100 тыс. км. Обусловлено это тем, что автовладельцы используют некачественное топливо и масло, которые снижают ресурс агрегата.
Избежать подобных проблем можно при помощи гильзования блока цилиндров, которое обеспечивает нормальное функционирование двигателя и увеличивает ресурс БЦ и самого агрегата.
Залогом правильной работы двигателя является обкатка. В нее входит обязательный прогрев двигателя в течение 5-10 минут перед каждой поездкой, а также ряд запретов и ограничений: на большие обороты, резкие разгоны и остановки, торможение двигателем, перевозку грузов или буксировку прицепа и т.д.
Период обкатки может составлять от до 10-15 тыс км. Лишь после этого можно постепенно увеличивать нагрузку на двигатель.
За время обкатки масло в ДВС меняется четыре раза. Первый раз спустя 500 км, затем спустя 1000 км меняется масло и фильтр, после этого жидкость обновляется на 1500 и 2000 км. Это делается для того, чтобы продукты износа, образующиеся в процессе приработки новых деталей, удалялись из системы вместе с маслом.
Полностью обкатка завершается спустя 10-15 тыс. км после капремонта. После этого можно переходить на рекомендуемый интервал обслуживания и увеличивать нагрузку на двигатель.
Рекомендации по эксплуатации двигателя
Ресурс двигателя зависит от множества факторов, но, для того, чтобы он проработал как можно дольше следует своевременно производить замену масла, следить за его качеством и качеством топлива, менять топливный и масляный фильтры, не перегружать двигатель, а также вовремя устранять возникающие неисправности и проводить профилактику.
Основной причиной того, что двигатель выходит из строя является несоблюдение регламента по замене масла и фильтрующих элементов.
Учитывая, что в нашей стране качество топлива низкое, а дороги оставляют желать лучшего, моторное масло быстро окисляется, а через засоренные фильтры в двигатель попадают посторонние частицы. Следствием этого является усиление износа, закоксовка каналов смазки и т.д.
Само моторное масло уже к 10 тыс. км пробега перестает выполнять свои смазывающие и защитные функции. Поэтому даже самую дорогую и качественную жидкость рекомендуется обновлять не позднее данной отметки.
Большой проблемой для автовладельцев также является то, что сегодня на рынке присутствует большое количество контрафактной продукции. Основу подобного масла составляет некачественная минералка, разлитая в канистры известных производителей.
Особенно от такой продукции страдают современные двигатели с турбонаддувом. В отдельных случаях происходит закупоривание каналов системы смазки, возникает масляное голодание и задиры. В худшем случае двигатель заклинит и уже никакой ремонт не поможет.
Ресурс ДВС также зависит от состояния его компонентов и их правильной конфигурации. Так, вследствие неправильной установки ремня ГРМ снижается мощность агрегата и т.д., вплоть до серьезных поломок. Поэтому любые изменения в работе агрегата нужно сразу же диагностировать и устранять.
Стоит обращать внимание и на посторонние шумы при работе агрегата. Если стучат поршни или поршневые пальцы, шатуны, коленвал и распредвал, клапана и гидрокомпенсаторы следует незамедлительно обратиться в сервисный центр и сделать диагностику. При подобных стуках в некоторых случаях эксплуатировать автомобиль не рекомендуется.
Рабочая температура оказывает наибольшее влияние на ресурс любого ДВС. Перегревы и локальные перегревы вызывают прогорание прокладки головки блока цилиндров, деформацию ГБЦ, выводят из строя многие узлы агрегата.
Необходимо также следить за состоянием системы охлаждения, так как попадание антифриза в моторное масло приводит к разжижению и потерей последним своих свойств.
atf.ru
Капитальный ремонт ДВС – как это делается сегодня?
Современные технологии позволяют выполнить капитальный ремонт ДВС и восстановить даже самые безнадежные моторы.
В нашей предыдущей статье мы писали о том, что в связи с экономическим кризисом и подорожанием импортных запасных частей вновь становится актуальным и экономически целесообразным капитальный ремонт двигателей внутреннего сгорания (ремонт ДВС). В этой статье мы расскажем об основных методах и технологиях, которые применяются при восстановлении поврежденных и изношенных частей двигателя.
Перед проведением капитального ремонта двигателя автомобиля выполняют его полную разборку, после чего все детали моют и дефектуют. Это является обязательным условием для обеспечения высокого качества результата ремонта ДВС, так как продукты износа и части поврежденных деталей могут попасть в рубашку охлаждения или перекрыть масляный канал, что приведет к повторному выходу из строя отремонтированного двигателя.
Блок цилиндров перед началом ремонта проверяют в специальной опрессовочной ванне на наличие скрытых трещин. Выявленные неглубокие повреждения ремонтируемого двигателя автомобиля сначала рассверливают до основания при помощи фрезы, после чего проваривают металлом. С помощью сварки заделывают и пробитые шатуном отверстия в блоке ремонтируемого ДВС, а также восстанавливают поврежденные перегородки между цилиндрами. Стоить отметить, что блоки из алюминия и алюминиевых сплавов варить легче, чем чугунные, так как у них более низкая температура плавления. Отверстия в блоках из чугуна устраняют при помощи чугунных заплаток.
Расточка блока цилиндров
Изношенные или поврежденные стенки цилиндров растачивают до ремонтного размера и используют поршни и поршневые кольца большего диаметра. Но такой способ ремонта ДВС применим только для моторов, завод-изготовитель которых при конструировании сделал запас, позволяющий выполнить расточку блока цилиндров.
В гильзованных блоках цилиндров гильзы выпрессовывают и устанавливают новые. Ремонт ДВС, для которых производитель этого не предусмотрел, выполняется следующим образом: сначала необходимо расточить цилиндр, а далее запрессовать чугунную гильзу с диаметром под стандартный поршень для каждого отсека. В случае если блок цилиндров ремонтируемого двигателя автомобиля изготовлен из алюминиевого сплава и имеет небольшую толщину стенок между цилиндрами, то чугунная гильза еще и усиливает конструкцию.
Деформированные при перегреве поверхности блока и головки шлифуют на станке, прокладку при этом подбирают такой толщины, чтобы не изменилась степень сжатия.
Коленвал и шлифовка
Поврежденные постели коленвала ремонтируемого двигателя автомобиля восстанавливают обработкой на горизонтально-хонинговальном станке. При этом снимают очень тонкий слой металла и обеспечивают идеально ровную ось вращения, что является очень важным условием, так как в противном случае на вал будут действовать неравномерные нагрузки, которые могут привести к его заклиниванию или поломке и полном отказе отремонтированного ДВС.
Дефектовку коленчатого вала проводят как визуальным осмотром и измерениями, так и с помощью различных технических средств. Довольно интересным методом проверки коленвала является магнитная дефектоскопия:
- коленчатый вал устанавливают на две опоры с обмотками разных полярностей;
- на поверхность наносят специальное масло;
- после коленвал посыпают металлическим порошком.
Магнитное поле, которое создается при прохождении тока через вал, позволяет обнаружить скрытые трещины вала, т.к. над ними характерно выстраиваются частицы порошка.
Обнаруженные неглубокие повреждения на шейках устраняют шлифовкой коленвала, при этом для ремонтируемого ДВС подбирают вкладыши необходимых размеров. Если оригинальных ремонтных деталей нет, то их заменяют на неоригинальные, а иногда изготавливают самостоятельно под требуемые размер.
При ремонте двигателя автомобиля изгибы коленчатого вала правят на специальном прессовом оборудовании. При большом износе шеек на них наваривают ленту, изготовленную из высокопрочного сплава, после чего коленвал шлифуют под размер вкладышей. В такой же способ восстанавливают поврежденные от выработки поверхности под сальниками. Во время ремонта ДВС восстановлению подлежат также и сломанные шпоночные соединения.
Описанный метод не применяют для коленчатых валов дизелей, т.к. они работают при более высоких нагрузках, которые приходятся на детали кривошипно-шатунного механизма. Покупать новый коленвал придется только в случае наличия на нем больших трещин.
Поршневая группа – замена поршней?
При капитальном ремонте двигателя автомобиля замена поршней может быть необязательной, если остаточная толщина их стенок и днища позволяет выполнить восстановление. Однако производители поршней не предоставляют ремонтных размеров и предприятия, которые специализируются на ремонте ДВС, могут рассчитывать только на свой личный опыт.
На поврежденном от удара о клапан днище поршня делают цековки. Если не удается найти кольца подходящего размера для поршня ремонтируемого двигателя автомобиля, то под них немного растачивают канавки.
Не заменяя поршней, на прессовом станке выравнивают и сами шатуны, а под поршневой палец устанавливают новую втулку.
ГБЦ
Проверку головки блока цилиндров (ГБЦ) выполняют так же, как и самого блока – в опрессовочной ванне. Для того чтобы расширились скрытые трещины, в нее наливают горячую воду, после чего закрывают все технологические отверстия и под избыточным давлением подают воздух в рубашку охлаждения. В случае наличия трещин в соответствующем месте будет видно пузырьки воздуха.
Восстановление ГБЦ, как и блока цилиндров, выполняют при помощи сварки. После чего вновь проводится проверка головки блока ремонтируемого ДВС в опрессовочной ванне.
Другие возможные технологические операции при капитальном ремонте двигателя автомобиля:
- Направляющие втулки клапанов меняют на ремонтные (если такие есть) или изготавливают самостоятельно.
- Чрезмерно изношенные седла клапанов растачивают, а на их место запрессовывают новые.
- Изогнутые распредвалы выравнивают на прессовом станке. Как правило, трещин на них не бывает.
- Постели, как и в блоке цилиндров, растачивают на специальном станке. После чего на опорные поверхности валов наваривают ленты металла и выполняют шлифовку.
Разработанные за долгое время технологии ремонта позволяют восстановить практически любой двигатель с повреждениями самой разной сложности. Но не стоит забывать, что капитальный ремонт – дело не дешевое и прежде чем начать выполнение работ, необходимо провести экономические расчеты, ведь возможно гораздо дешевле будет приобрести новый силовой агрегат.
info-parts.ru
Современные двигатели: можно ли их починить?
Список операций, выполняемых при капитальном ремонте ДВС, долгое время сохранялся практически неизменным. Расточка и хонингование цилиндров, постелей коленвала и распредвала, восстановление плоскостей ГБЦ и блока, шлифовка и восстановление геометрии коленвала, замена втулок клапанов и восстановление геометрии седел, клапанов и втулок. Еще оставались мероприятия по ремонту серьезно поврежденных узлов и, конечно, замена элементов поршневой группы, поршней и колец, элементов ГРМ, помпы и уплотнений. Сложно? Современные двигатели могут потребовать вдвое больше операций.
Что мы называем «современным двигателем»? С уверенностью можно сказать, что это агрегат с регулируемыми фазами ГРМ, с регулируемой длиной впускного коллектора и катколлектором, часто в алюминиевом блоке, с балансирными валами, часто с турбонаддувом и непосредственным впрыском и обычно с пластиковым впуском. А у дизельных моторов почти наверняка будет система CommonRail и турбины с регулируемой геометрией. У моторов премиум-марок в дополнение окажутся регулируемые маслонасосы и отключаемые цилиндры, хитрая компоновка, электроприводы помпы и маслонасоса.
С определенной степенью вероятности ремонтных размеров поршневой группы у подобных двигателей не будет, только несколько размерных групп и ремонтные комплекты коленвала, а также возможность восстановления седел клапанов. Ремонт в этом случае потребует проверки значительно большего числа узлов и целого ряда точек их установки и крепления, а заодно и замены огромного количества навесного оборудования. Что придется сделать для восстановления надежной работы современного силового агрегата? И насколько список работ будет больше, чем у «классических» моторов из прошлого века?
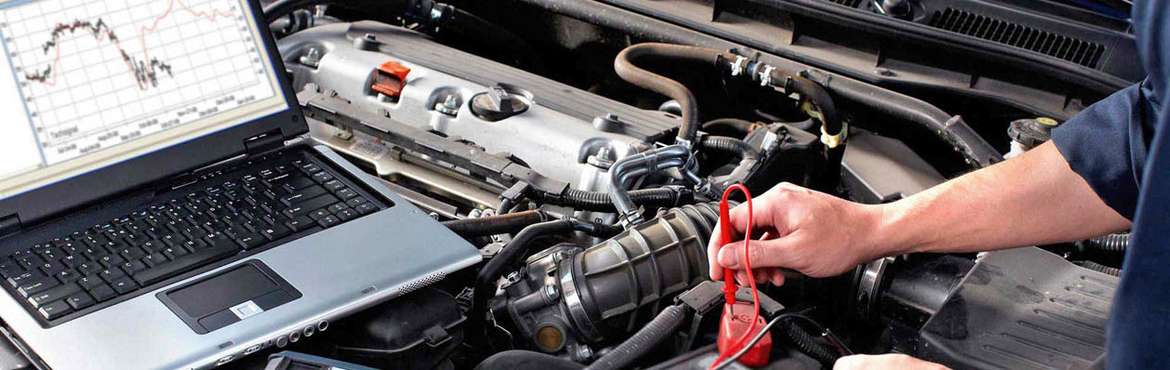
Базовая операция при капитальном ремонте — это восстановление геометрии поршневой группы, а также работы над блоком цилиндров и коленчатым валом. Даже если блок чугунный или имеет чугунные гильзы, простая расточка обычно бесполезна: нет ремонтных размеров поршней и колец. Индивидуальный заказ, как правило, дорог и может не обеспечить нужного качества и ресурса. Остается только произвести гильзовку блока цилиндров. Эту же операцию придется проделать, если алюминиевый блок имеет технологии упрочнения стенок, не предусматривающие наличия ремонтных размеров и восстановления отдельной гильзы, такие как: напыление, alusil, FRM, nicasil и тому подобные покрытия с повреждениями хотя бы в одном из цилиндров. Для покрытий, наносимых с использованием плазменного напыления или гальваники, возможно локальное восстановление, но оно применяется редко.
Ряд легкосплавных блоков потребуют также целого набора операций по восстановлению резьбы для болтов, заворачиваемых с программируемой вытяжкой, или просто высоконагруженных соединений. Для блоков, изготовленных прессованием, обязательна проверка на микротрещины и герметичность. И конечно, обязательна промывка «рубашки» системы охлаждения. Для блоков цилиндров со встроенными балансирными валами также потребуется дефектовка и замена их подшипников или самих блоков валов.
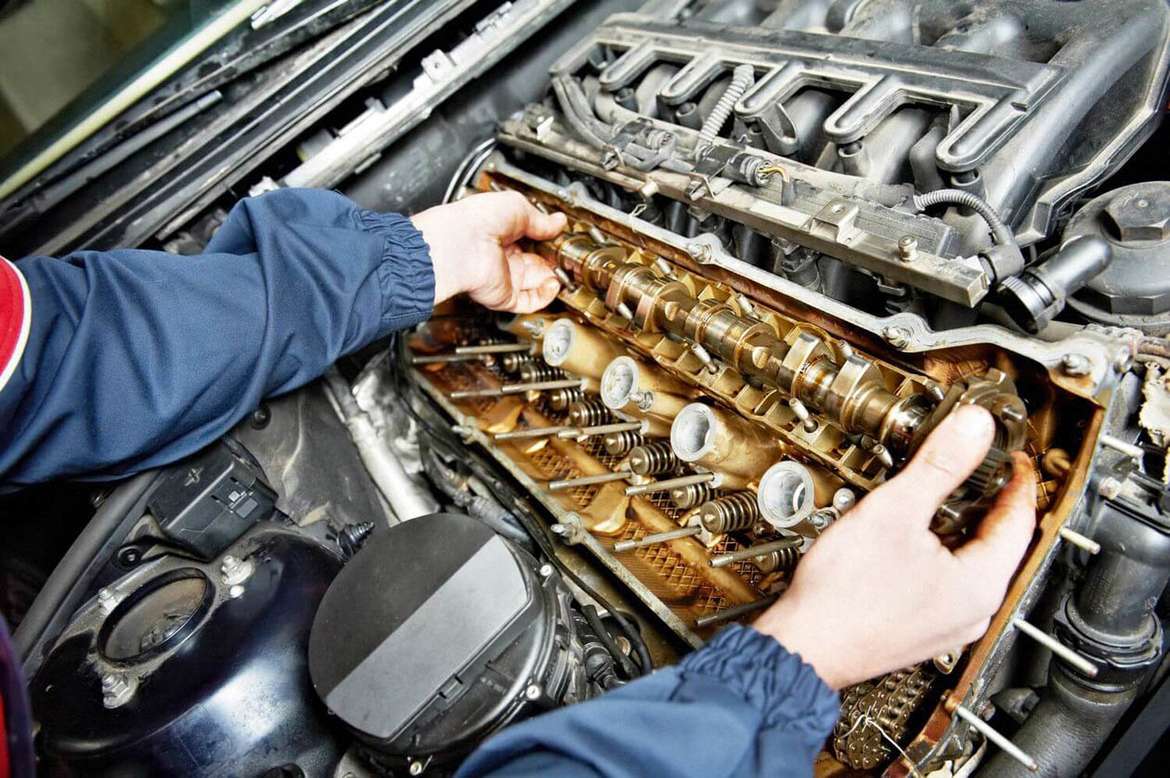
Часто необходима замена крышки ГРМ или другие внешние элементы в связи с обновлением, улучшением характеристик и устраненными недостатками. А порой пластиковые детали просто не подлежат повторной установке из-за коробления поверхностей или растрескивания.
Ремонт головки блока цилиндров тоже потребует большего числа операций. Тут и чистка всех каналов от масляного шлама и нагара, и проверка на герметичность, и проверка посадочных мест всех клапанов, и тому подобные операции. Часто потребуется восстановление плоскостей, работающих с сальниками распредвалов, если они не выполнены в виде отдельной детали.
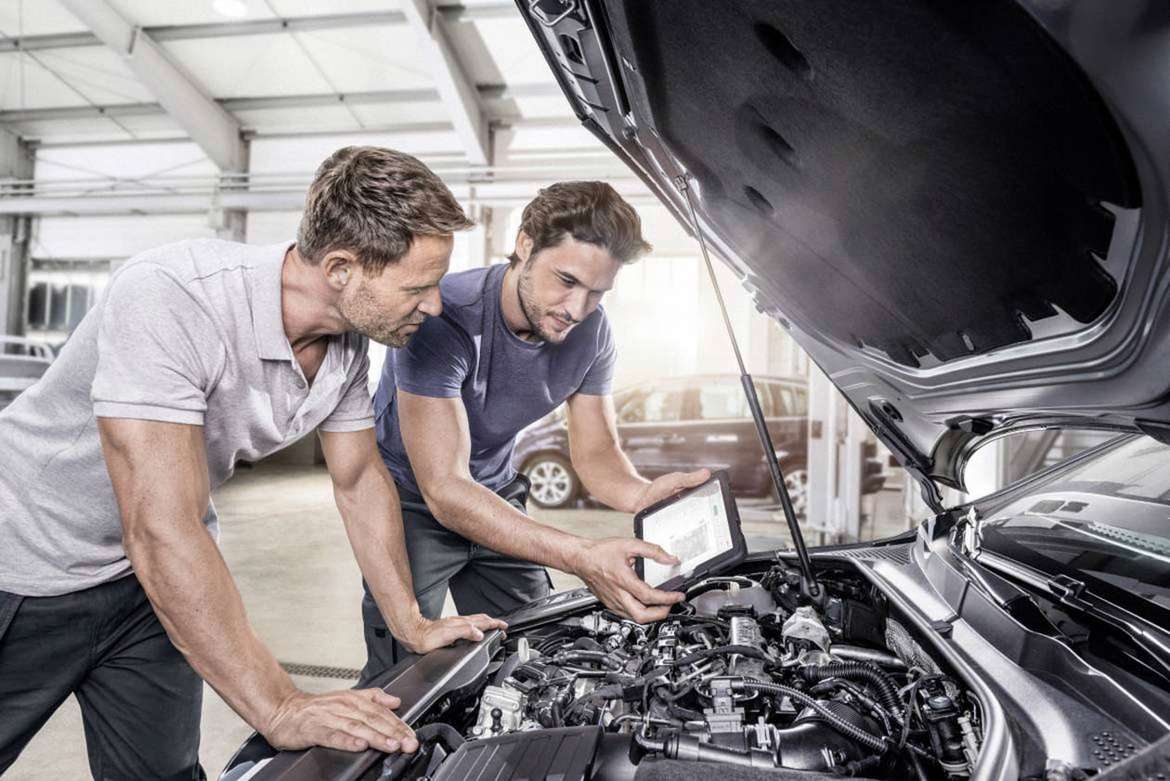
Работы с клапанами, их седлами и втулками часто осложняются тем, что эти элементы не ремонтируются, поскольку изготовлены из керамики или с помощью металлокерамической матрицы (MMC), и потому они вырезаются и заменяются на ремонтные целиком, даже при небольших нарушениях геометрии.
Начинка ГБЦ также подвергается серьезной ревизии. Так, замена распредвалов требуется все чаще, даже несмотря на внедрение схем ГРМ с отсутствующим трением скольжения, например на роликовых рокерах. Меняют или ремонтируют регуляторы фаз (фазовращатели) и их клапана управления, сальники систем подачи масла и фильтры. Часто требуют чистки и ремонта каналы системы EGR, если они выполнены непосредственно в теле ГБЦ или блока, как на моторе Mercedes M271. Меняются, дефектуются и чистятся также сопутствующие этой системе детали, клапаны EGR и теплообменники.

Такая деталь, как маслонасос, постепенно превращается в расходный материал. В целом ряде моторов их рекомендуется менять, не доводя до максимального износа, а уж после капремонта точно потребуется новый маслонасос, а заодно его цепь и блок балансирных валов в комплекте.
Такие элементы передовых двигателей, как электрические помпы и разнообразные соленоидные клапаны регулирования давления масла, требуют замены в обязательном порядке. Термостаты тоже превратились в расходный материал, причем менять придется чаще всего все вместе с патрубком, датчиками, системой подогрева и даже собственным приводным ремнем.
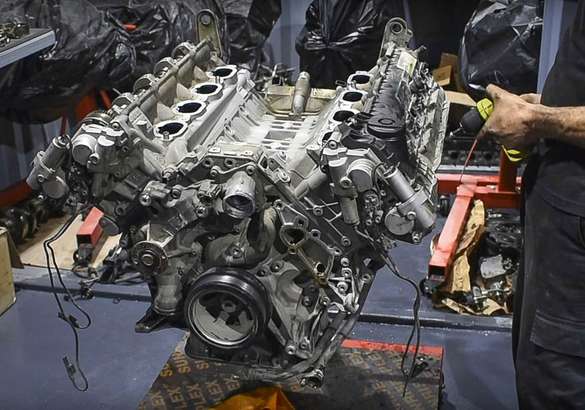
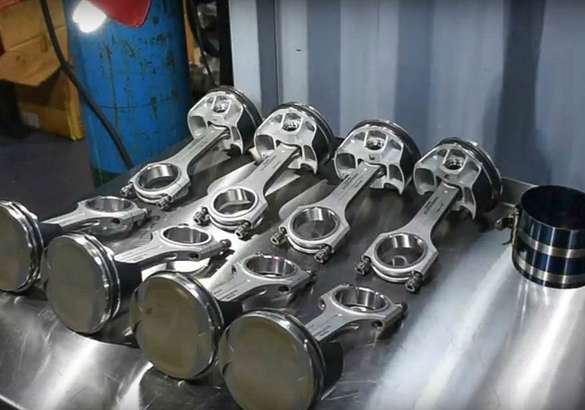
Серьезных работ почти наверняка потребуют впускная и выпускная системы. Помимо случавшихся и раньше трещин выпускного коллектора, новым моторам грозит поломка катализаторов. Эта дорогая деталь имеет ограниченный срок службы, а если мотор расходует масло или регулярно запускается при очень низких температурах, катализаторы выходят из строя куда раньше прогнозируемого срока. При повреждении они также способствуют быстрому износу поршневой группы, поставляя пыль сначала через EGR, а затем и непосредственно через выпускные клапаны. Сажевые фильтры у дизельных моторов тоже добавят хлопот при ремонте. Если прожиг невозможен, то потребуется их замена.
Впускной коллектор у очень многих моторов имеет изнашиваемые элементы вроде заслонок и их привода. Он может потерять герметичность из-за разрушения осей заслонок и даже протирания стенок. При установке требует обязательной чистки (особенно у машин с системами EGR), ремонта всех систем изменения геометрии или попросту замены. Добавляют расходов не меняющиеся отдельно от коллектора датчики. Удивительно, но дроссельная заслонка также постепенно переходит в разряд узлов с ограниченным сроком службы: датчики положения заслонки и электропривод все чаще не поставляются отдельно и не являются ремонтопригодными.
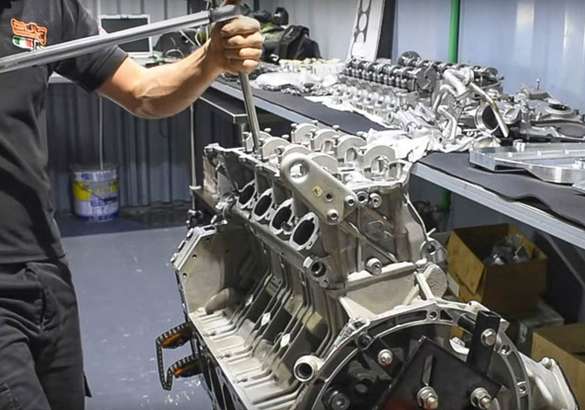
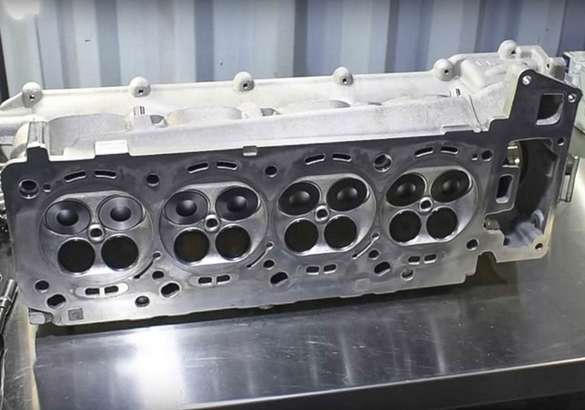
Топливная система современного мотора тоже устроена сложнее, чем карбюратор или даже распределенный впрыск, и требует большего внимания. Такие элементы, как насос ТНВД бензиновых и дизельных моторов, форсунки непосредственного впрыска, рампы с датчиками давления, зачастую потребуют серьезной проверки и ремонта, если нужна гарантия качественной работы силового агрегата.
Даже система вентиляции картера у современных моторов не так проста. У атмосферных двигателей появляются как минимум PCV-клапаны, требующие регулярной замены, а если двигатель с наддувом, то протяженность трасс вентиляции возрастает в разы — в них появляются клапаны и почти всегда присутствует так называемая маслоловушка.
Современные поршневые группы создают достаточно большой поток картерных газов, а требования к большим интервалам замены масла заставляют конструкторов улучшать газообмен в картере для предотвращения раннего старения масла. Как итог — большая нагрузка на систему вентиляции, низкий ресурс трубок, высокие требования к качеству ее работы и потери масла при неисправностях.
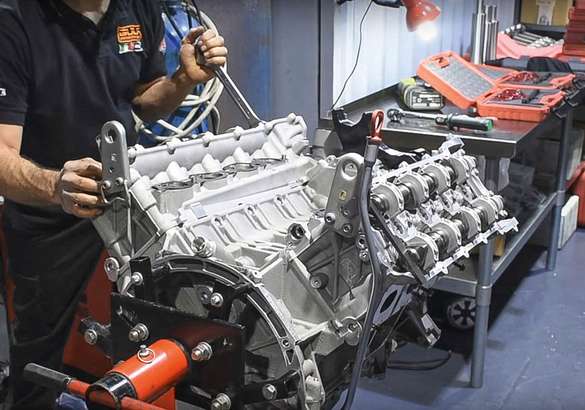
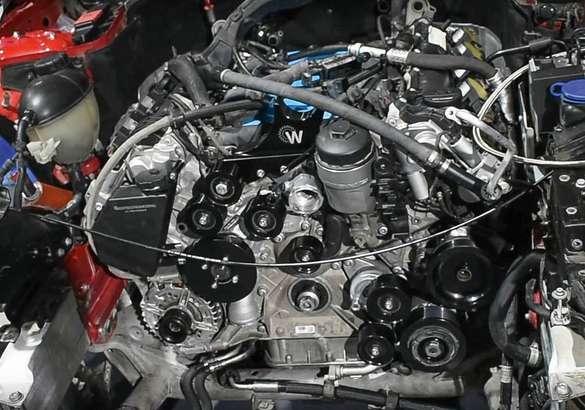
Каков итог?
Как можно увидеть, ремонт современного мотора представляет собой обширнейший комплекс сложнейших операций, которые многократно увеличивают стоимость не только из-за применения дорогих и высокотехнологичных узлов и компонентов, но и за счет заметно увеличившегося количества трудозатрат. Стоит учитывать и то, что все работы должны выполняться с очень высоким качеством механической обработки и использованием специальных сборочных материалов, приспособлений и при высокой чистоте. Так что стоит много раз подумать, прежде чем покупать по бросовой цене «под восстановление» современную машину с отметкой «требуется небольшой ремонт двигателя».
dvizhok.su
Ремонт блока цилиндров: как это делается
Итак, мы подошли к финишной прямой. В нашем двигателе Mitsubishi 4М41, который проехал полмиллиона километров, после ремонта головки блока цилиндров и цепного привода ГРМ осталось разобраться с кривошипно-шатунным механизмом и блоком цилиндров. К слову, именно по состоянию блока цилиндров озвучивались самые пессимистичные прогнозы — ведь такой пробег не мог не сказаться на геометрических характеристиках. Однако после полной ревизии блока этот двигатель окончательно влюбил в себя нашего мастера.
Кривошипно-шатунный механизм и блок цилиндров
Блок цилиндров — это металлическая корпусная деталь, в которой заключены элементы того самого кривошипно-шатунного механизма, благодаря которому поступательное движение поршней превращается во вращательное движение коленчатого вала. Внутри блока имеются полости, которые при работе мотора заполняются охлаждающей жидкостью — водяная рубашка. Блоки изготавливаются из чугунного или из алюминиевого сплава: сам по себе блок должен быть массивным, потому что воспринимает довольно увесистые ударные нагрузки, передаваемые от поршней. Также не стоит забывать о нагреве, последствия которого необходимо минимизировать.
Сверху блок накрывается головкой блока (ГБЦ), снизу — поддоном картера. В самом блоке располагаются гильзы, внутри которых перемещаются поршни. Внутренняя поверхность гильзы, которая непосредственно контактирует с поршнем, называется зеркалом цилиндра. В нижней части блока имеются «постели» — ложементы, в которые укладывается коленчатый вал, накрываемый крышками. При накрытии постели крышкой образуется отверстие, называемое коренной опорой коленвала.
Важно, чтобы блок цилиндров был достаточно жестким, так как силы, возникающие в процессе работы, пытаются скрутить, изогнуть и разорвать блок — именно поэтому он долгие десятилетия и оставался чугунным. Тренд современности — более легкие блоки цилиндров из алюминиевого сплава, с которыми (как и с облегченными чугунными) применяют интегрированные крышки коренных опор, называемые рамкой лестничного типа.
Итак, получается следующее: в классическом исполнении (как у нас, например) каждая коренная шейка коленчатого вала накрывается отдельной крышкой коренной опоры (ее часто называют бугелем). В рамке лестничного типа все бугели объединены в одну конструкцию, похожую на лестницу — таким образом конструкторы добились значительного повышения жесткости блока цилиндров. Недостатком данного подхода можно назвать стоимость изготовления подобной детали.
Разобравшись с блоком, переходим к движущимся частям — и первыми будут поршни. Они изготавливаются из алюминиевого сплава и конструктивно имеют юбку, днище и бобышки. Юбка — это боковая часть поршня, бобышки — это приливы, в которых выполнено отверстие под поршневой палец, а днище — это плоскость, обращенная непосредственно в камеру сгорания и непосредственно воспринимающая все нагрузки в процессе сжигания топливовоздушной смеси. Интересно, что днище поршня может быть плоским, как стапель краснодеревщика, а может иметь настолько сложную форму, что понять с первого раза, что это поршень, будет тяжело.
Сложность формы поршня, если таковая имеется, тщательно просчитана в угоду улучшению смешивания топлива с воздухом (что часто встречается в бензиновых ДВС с непосредственным впрыском топлива). Если же двигатель работает на дизеле (как наш), в поршне может находиться камера сгорания, а сам он будет значительно массивней своего бензинового собрата.
Поршень устанавливается в цилиндр с определенным зазором (часто 0.2–0.3 мм), потому для его уплотнения предусмотрены поршневые кольца. На современных двигателях поршень опоясывают два компрессионных и одно маслосъемное кольцо. Соединяется поршень с коленчатым валом через шатун — соединительный элемент. Один его конец крепится к поршню через палец, который запрессовывается или просто вставляется и стопорится кольцами в поршне и головке шатуна. Второй конец — разборный: для закрепления на коленвале необходимо установить крышку шатуна и затянуть ее болты или гайки крепления.
И коленвал с блоком, и шатуны с коленвалом контактируют через подшипники скольжения, они же вкладыши. Для дополнительного охлаждения поршней внутри блока могут быть установлены распылители масла, направленные на поршни.
Рядная «шестерка» считается одним из самых уравновешенных двигателей (в плане колебаний). У нас же — рядная «четверка», причем внушительного объема, а потому в блоке цилиндров установлены два балансирных вала, суть работы которых сводится к уменьшению колебаний двигателя.
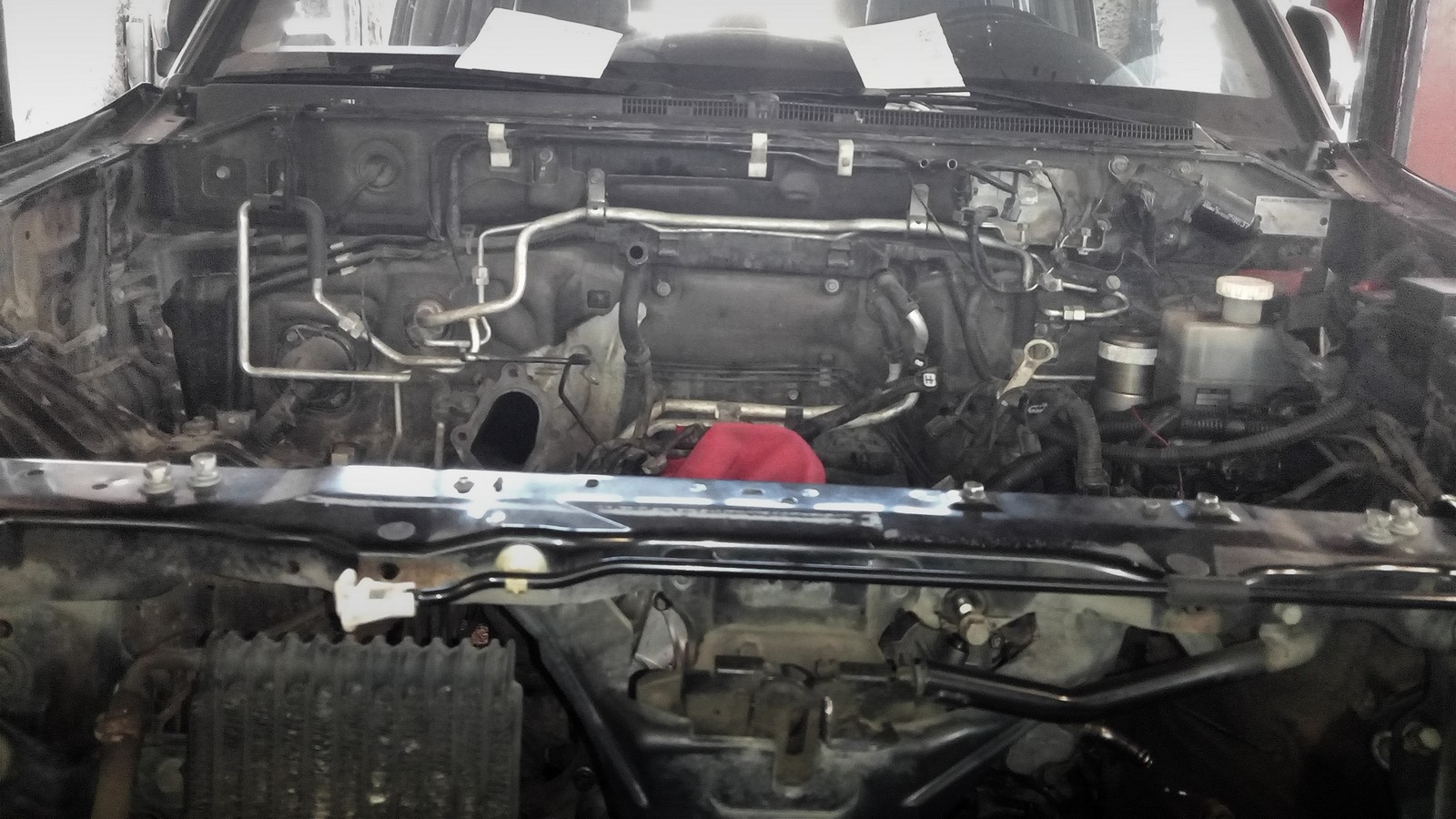
Что может поломаться
Одни из самых уязвимых деталей двигателя — поршневые кольца: из-за нагара они могут залипнуть в буквальном смысле слова. При этом могут лопнуть сами кольца, а могут и перемычки на поршне, между которыми они установлены. Может, наконец, износиться непосредственно выборка под кольцо в поршне.
С самими поршнями потенциальных проблем меньше, но ситуацию это не облегчает. Самое простое, что может произойти — банальный износ и отклонение от номинального диаметра, полный же «трэш» — это прогорание поршня. Кроме того, возможен износ поршневого пальца и отверстий под палец в бобышках поршня.
С шатуном все еще проще: здесь есть два нюанса, которые проверяют всегда, и два, которые часто игнорируют. Первые — износ втулки малой головки шатуна и износ вкладышей шатунного подшипника, а вторые — величина изгиба и кручения шатуна. Тем не менее, как показывает практика, шатун — один из самых редко заменяемых элементов в двигателе.
Самая распространенная проблема с коленчатым валом — износ рабочих поверхностей, второе по «популярности» место занимают случаи проворота вкладышей. Случается это, когда отсутствует достаточное количество масла в месте контакта, из-за чего коленвал срывает вкладыши подшипников и начинает «весело» вращаться вместе с ними. Это по-настоящему тяжелый случай: при определенном невезении ремонт может стоить замены блока.
Износ упорных колец коленчатого вала — тоже проблема довольно неприятная, хоть и незначительная на первый взгляд. Дело здесь в том, что не выявленный вовремя дефект в будущем может привести к заклиниванию двигателя — ведь на коленвал во время работы действуют силы и в продольном направлении тоже. Достаточно сместить вал на критическое расстояние — и поршни от перекоса просто заклинит. Стоит заметить, что поломка самого «колена» тоже возможна, хоть для этого и придется постараться.
В самом блоке конструктивно ломаться практически нечему — но это не означает, что с ним не бывает проблем, очень даже наоборот. Самые распространенные — износ цилиндров или коробление контактной поверхности блока с головкой из-за перегрева. Особо нерадивые автовладельцы, впрочем, могут сломать и сам блок цилиндров. Для этого нужно лишь выполнить парочку нехитрых операций: первая — залить в систему охлаждения обычную воду (можно дистиллированную), а вторая — оставить автомобиль на улице на ночь при минус 20°С.
Что измеряют при капремонте
Прежде всего, после разборки измеряют наружный диаметр поршней в строго определенной плоскости (поперек оси пальца) и на заданном расстоянии от поверхности днища поршня. Производитель может изготовлять поршни в нескольких размерах: номинальном и ремонтных — эти данные приведены в технической документации. Если поршень в «номинале» (как это оказалось у нас), проверяют биение шатуна и пальца. Профессионал может засечь неладное, что называется, на ощупь — неопытному же механику придется все-таки выпрессовать палец из поршня и шатуна. После выпрессовки необходимо измерить наружный диаметр пальца и внутренние диаметры втулки шатуна и отверстий в поршне, путем несложной математики вычислить зазор в данной сборке и принять финальное решение об утилизации или дальнейшем применении этого комплекта.
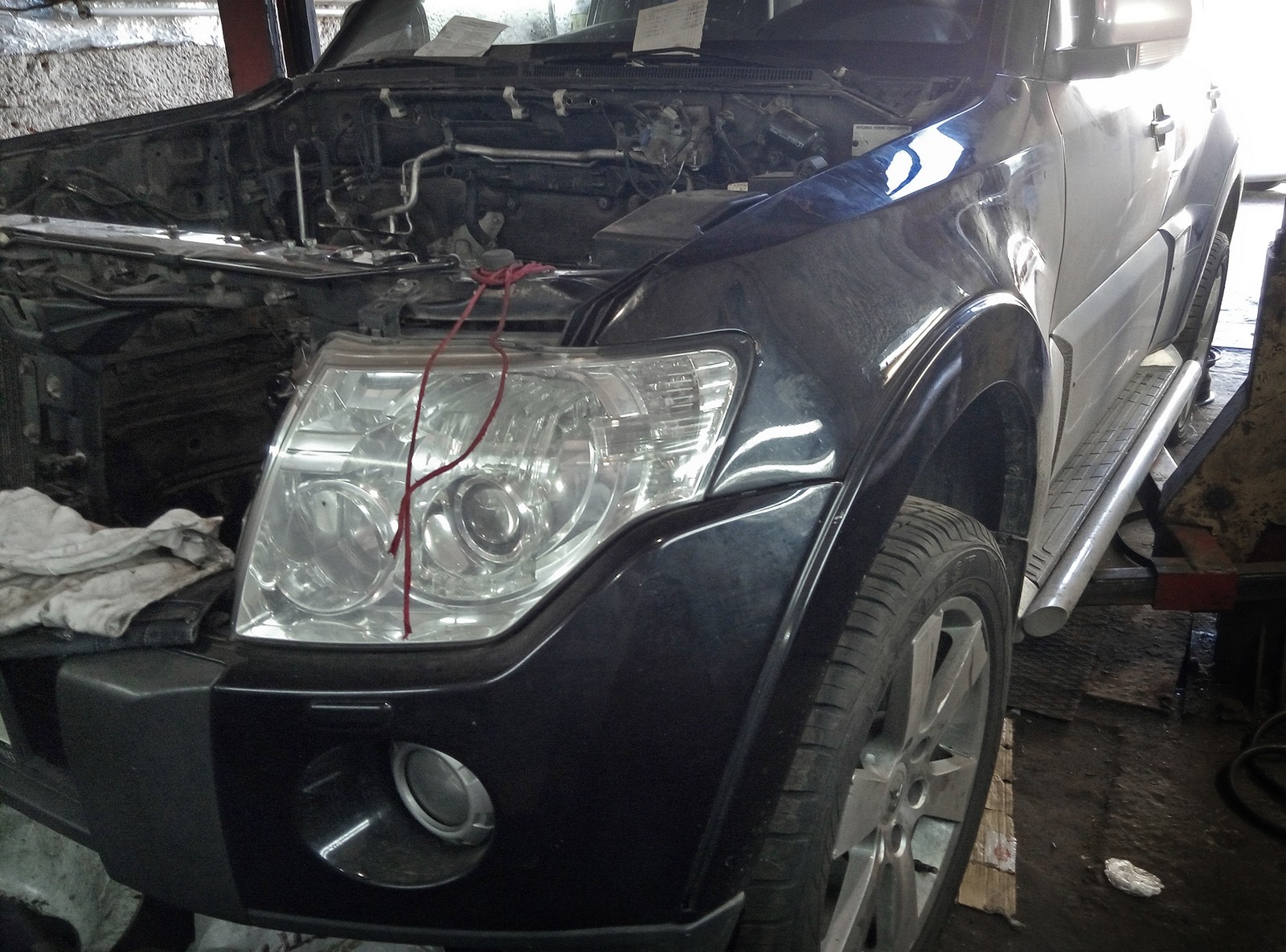
Вооружившись набором плоских щупов, специалисты-механики измеряют зазор между кольцом и выборкой в поршне: если он превышен — поршень отправляется под замену. Так как мы проводим капитальный ремонт, замена колец даже не обсуждается — это само собой разумеющийся факт.
Практически закончив с подвижными элементами, переходим к блоку цилиндров, для обмера которого необходим так называемый нутромер. Это приспособление, предназначенное для измерения внутреннего диаметра с высокой точностью, которая обеспечивается индикатором часового типа. Внутренний диаметр измеряют на трех уровнях и в двух взаимно перпендикулярных плоскостях: это необходимо для наиболее точного понимания величины и характера износа цилиндра. Характер износа в данном случае — величина бочкообразности и овальности цилиндра. Все дело в том, что нагрузка на цилиндр неравномерна, а, следовательно, неравномерен и его износ: ближе к центру величина износа будет расти, а затем снова уменьшаться. Из-за этого цилиндр в профильном разрезе слегка «округляется» и становится похожим на бочку. В свою очередь, поршень давит на цилиндр только в одном направлении, вырабатывая поверхность и превращая ее в овальную. Повторюсь, точность при работе с блоком должна быть предельной — никаких приблизительных размеров существовать просто не может: в технической документации обязательно есть цифры предельно допустимой бочкообразности и овальности цилиндров.
В конце концов, ревизии подвергается и коленчатый вал. У него измеряют диаметры коренных и шатунных шеек и, при необходимости, шлифуют до следующего ремонтного размера, если таковой предусмотрен. При помощи известного нам нутромера измеряются диаметры отверстий коренных опор (с установленными вкладышами, конечно). Затем, имея наружный диаметр шеек и внутренний диаметр опор, определяют масляный зазор: если он превышает допустимый, вкладыши отправляются под замену, а коленвал — на шлифовку. Кроме того, выше мы упоминали об осевом люфте коленвала — разумеется, при дефектовке измеряют и его, и если люфт завышен, заменяют упорные кольца коленвала.
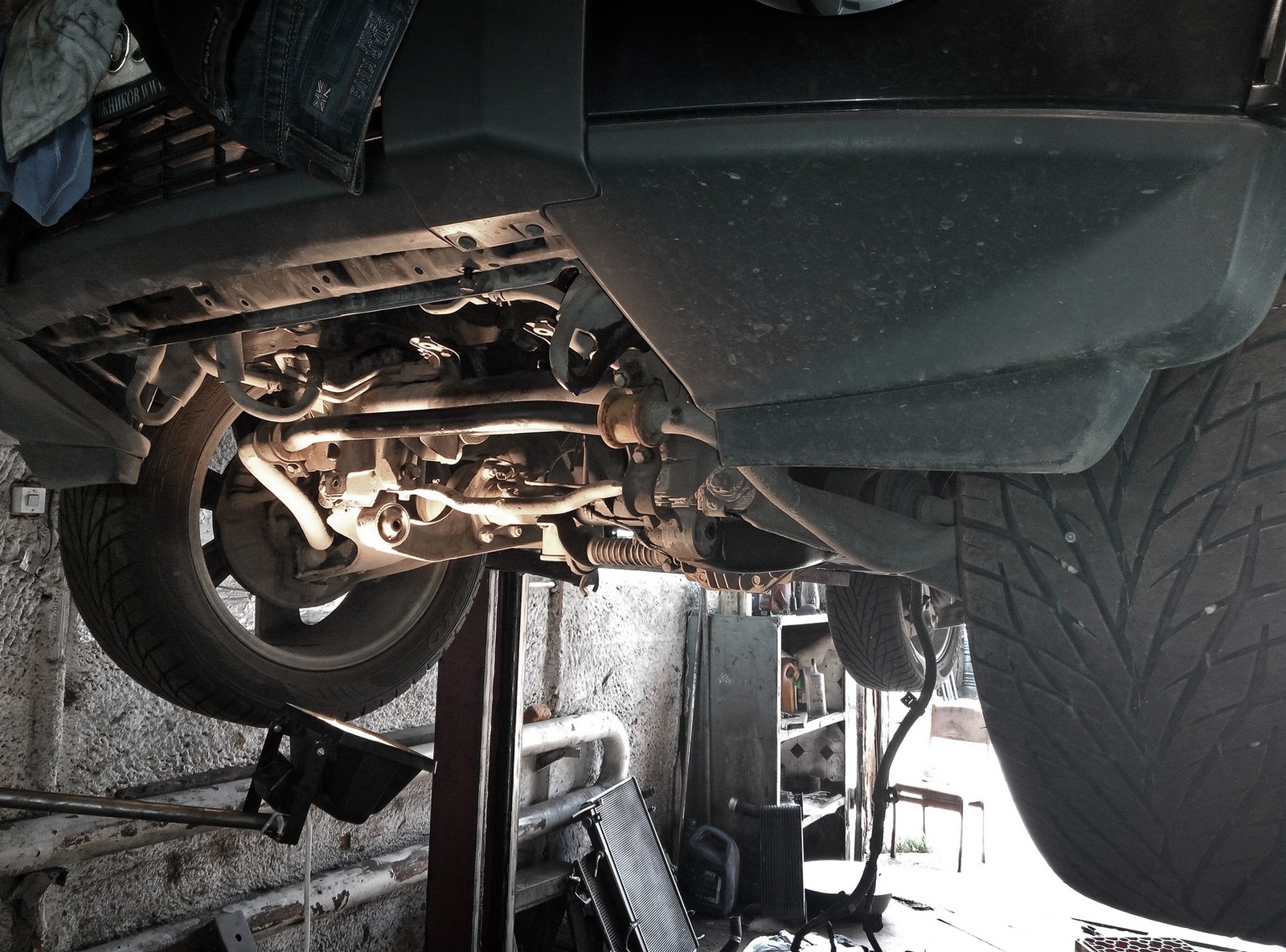
Как ремонтируется блок
Если состояние цилиндров совсем не позволяет продолжить эксплуатацию блока, его отправляют на расточку цилиндров до следующего ремонтного размера. Бывает, что производитель не предоставляет такой роскоши, тогда блок «гильзуют» — восстанавливают гильзованием. Как несложно догадаться, в этом случае существующую гильзу значительно растачивают и впрессовывают в нее еще одну гильзу с внутренним диаметром номинального размера. Однако это решение — уже не очень надежное, и некоторые мастера предсказывают такому двигателю не более 50 тысяч километров потенциального пробега.
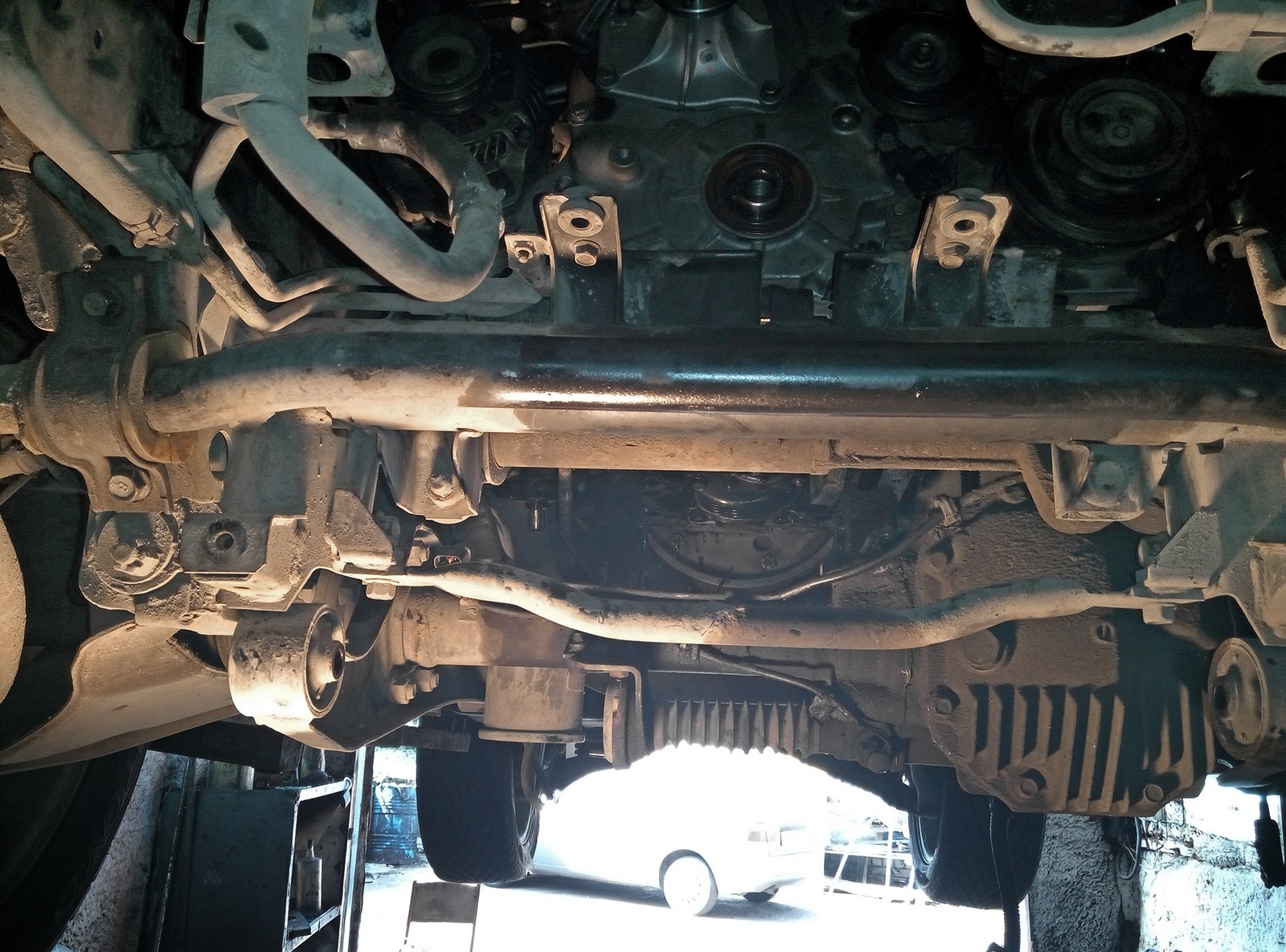
Если же блок растачивают, то, разумеется, и поршни с кольцами подбирают соответствующего размера. Шлифовка шеек коленчатого вала уменьшает их размер — а значит, и для них необходимо подобрать вкладыши следующего ремонтного размера. Работу облегчает то, что в техдокументации обычно присутствует размерная сетка подбора вкладышей.
Перед установкой поршней зеркало цилиндра подвергают хонингованию. Это процесс, который не изменяет размера цилиндра, но благодаря которому значительно уменьшается износ трущихся поверхностей. Хонингование — это нанесение небольших рисок на поверхность цилиндра с помощью специальных камней. Необходимо это для того, чтобы на поверхности цилиндра задерживалось моторное масло, увеличивая тем самым ресурс поршневой группы.
Ремонта блока цилиндров двигателя Mitsubishi 4М41
В нашем конкретном случае обошлось без сложных или интересных особенностей ремонта, так как замеры поршней, цилиндров и шеек коленчатого вала показали номинальные размеры.
Мнения наши разделились диаметрально: я немного расстроился, хозяин автомобиля — повеселел, а мастер… ему было все равно. Тем не менее, все мы очередной раз подивились стойкости данного мотора.
Перед разборкой блока и цилиндропоршневой группы мы сняли масляный поддон — и приступили к основной работе. Она свелась к извлечению поршней с шатунами из блока цилиндров. На всякий случай мы отметили номерами каждый поршень в соответствии с номером цилиндра.
После обмера поршней и цилиндров мы пришли к выводу, что коленчатый вал снимать смысла нет, так как биение отсутствует. Кольца все же заменили — да и то только потому, что они были предусмотрительно приобретены владельцем.
![]() | ![]() |
Дефекты же в разобранном нами моторе просто отсутствовали: никаких чрезмерных люфтов в сборке шатун-поршень, никаких задиров на шатунных вкладышах… Закончив дефектовку, мы в очередной раз убедились, что дорогое масло себя окупило.
![]() | ![]() |
После измерения коробления поверхности блока цилиндров мастер со словами «Ну хоть что-то же надо с ним сделать?!», отправил его на хонинговку цилиндров, а все прочие элементы — на тщательную мойку. После этого начался процесс сборки КШМ (кривошипно-шатунного механизма).
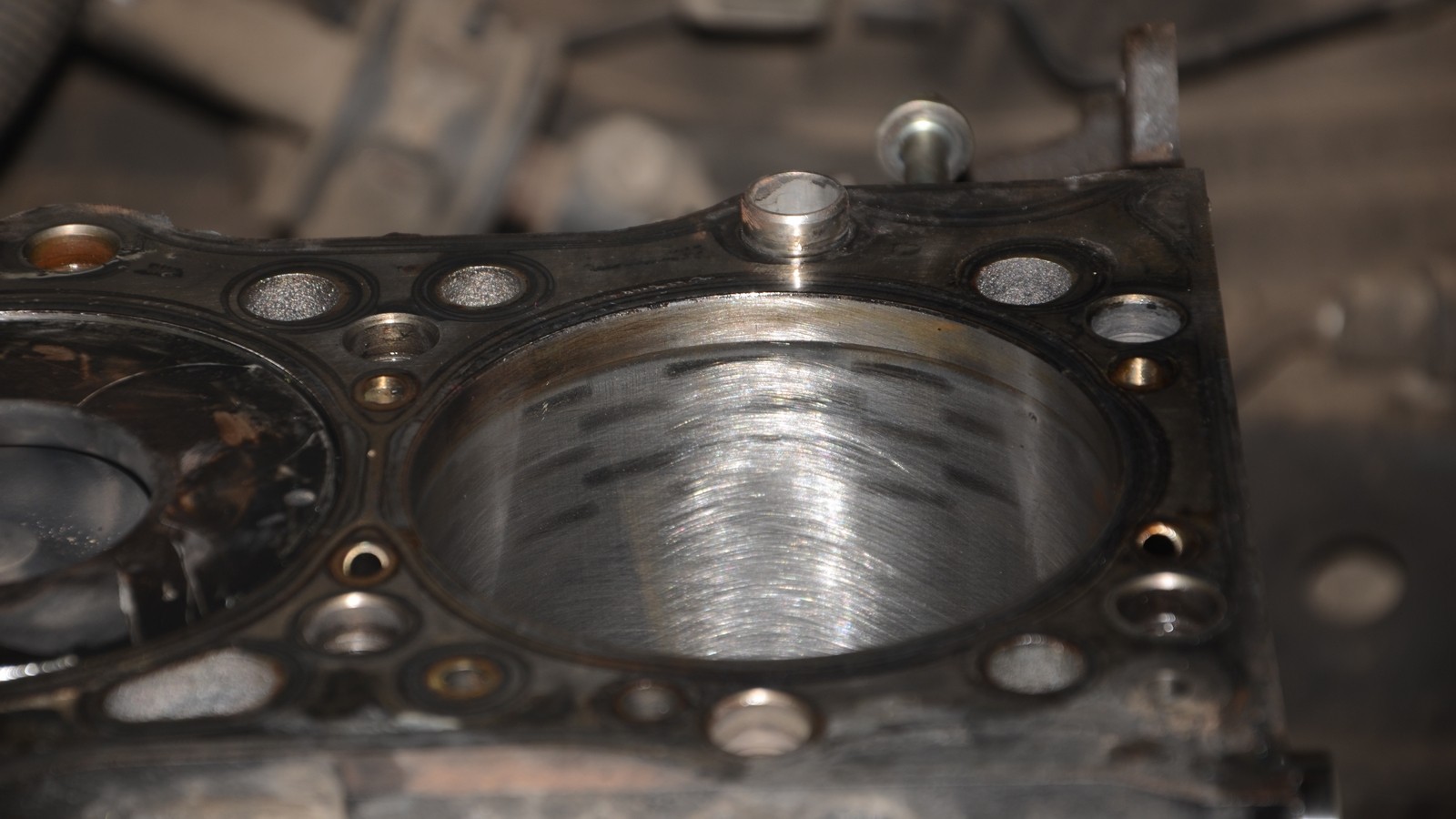
В шатуны и их крышки были установлены новые вкладыши, на поршни установили новые кольца.
Компрессионные кольца необходимо устанавливать в строго определенном направлении, и касается это абсолютно всех двигателей, а потому, чтобы не перепутать их, на поверхности кольца нанесены метки: надпись «ТОР» или иная.

Особенности установки поршневых колец на этом не заканчиваются. Поршневые кольца имеют разрез — ведь, во-первых, кольцо все-таки надо как-то установить на поршень, а во-вторых, компенсировать его тепловое расширение. Разрез этот называется замком кольца. Так вот, при установке колец их замки необходимо развести в разные стороны, чтобы минимизировать прорыв газов.
После выполнения всех вышеперечисленных операций мы нанесли на цилиндры свежее масло, установили на поршень специальное приспособление для обжима колец, четко сориентировали поршень относительно коленвала и блока, и легкими ударами рукояткой молотка установили шатунно-поршневую группу в блок.
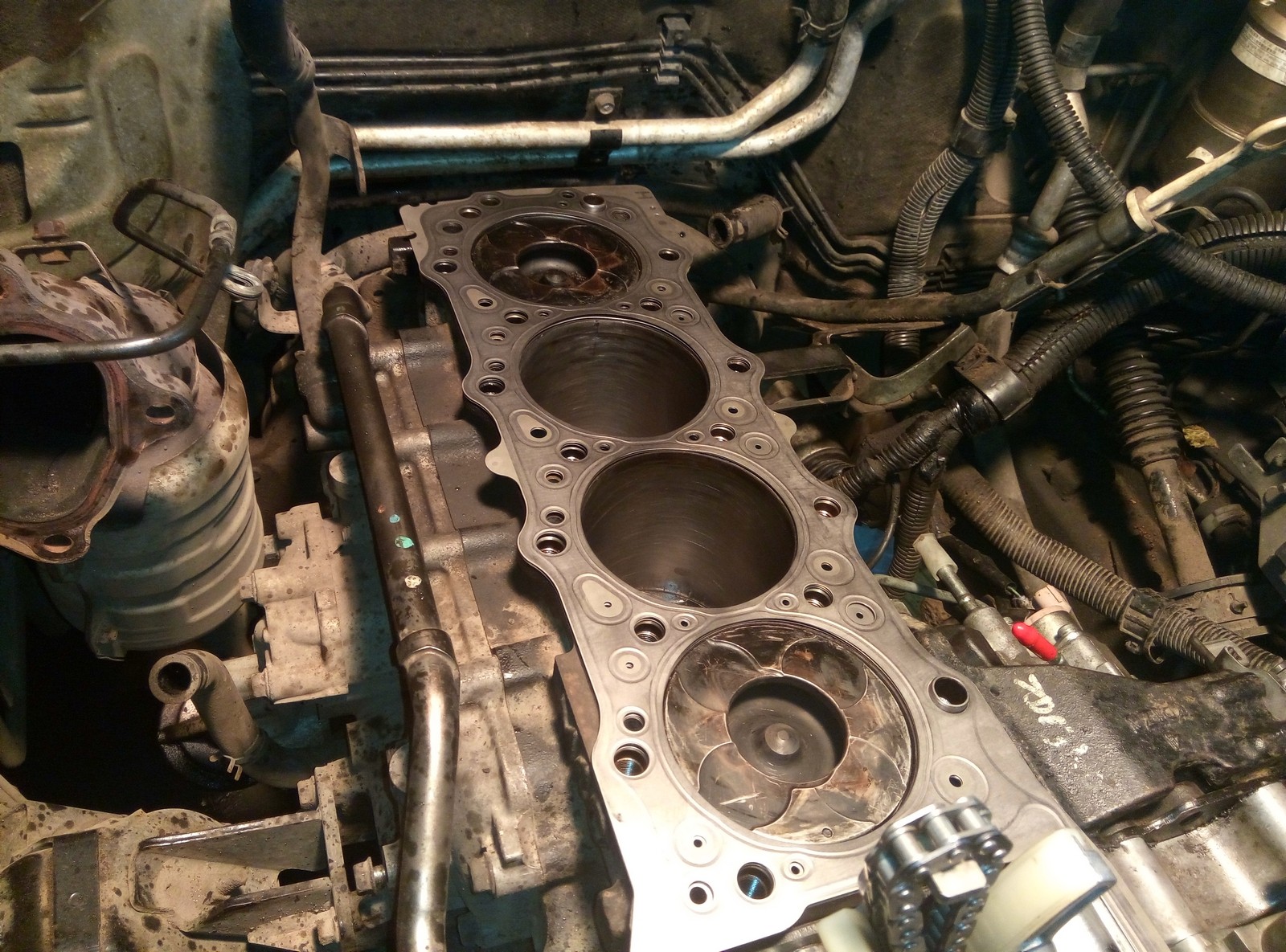
Если бы мы разбирали шатунно-поршневую группу, то при ее сборке пришлось бы следить за правильной установкой шатуна относительно поршня — в противном случае может возникнуть чрезмерный износ шатунных шеек коленвала. Нельзя изменять и расположение поршня в цилиндре: это очень важно, так как ось пальца самую малость не совпадает с осью поршня. Если нарушить установку, со временем в двигателе может возникнуть стук. Установив все поршни в блок цилиндров, мы подвели шатуны к шейкам коленчатого вала, установили крышки шатунов и затянули гайки их крепления с определенным моментом затяжки.
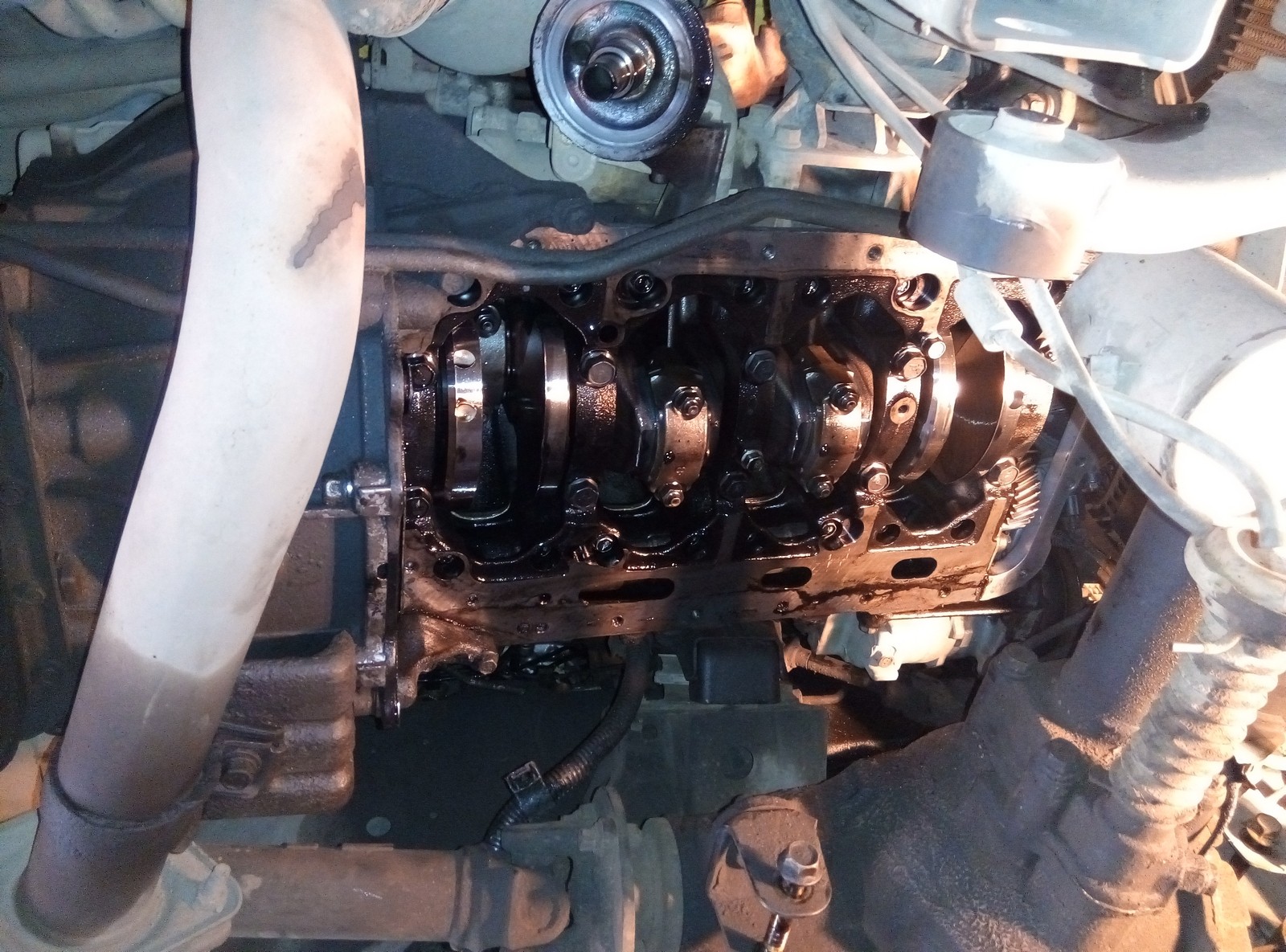
Отдельно остановлюсь на подборе прокладки головки блока цилиндров: у всех современных дизельных двигателей необходимо подбирать прокладку ГБЦ по толщине. Толщина эта будет зависеть от величины выступания поршня над поверхностью блока цилиндров. Так, после сборки КШМ каждый из поршней поочередно выводят в ВМТ и с помощью индикатора часового типа на стойке измеряют выступание поршня. Замер выполняют в двух противоположных точках поршня, потом вычисляют среднее арифметическое и в зависимости от высоты выступания подбирают толщину прокладки. Это — весьма важный момент, не уделив должного внимания которому можно поплатиться скорым прогоранием прокладки.
После установки всех и вся в блок цилиндров, мы накрыли его снизу масляным поддоном, предварительно тщательно очистив оный, промыв и высушив. Непосредственно перед установкой поддона на его поверхность нанесли специальный герметик и в течение 15 минут после нанесения установили поддон на блок, затянув болты крепления с необходимым моментом затяжки.
![]() | ![]() |
Ремонт завершен!
На этом ремонт нашего мотора был завершен — пожалуй, нам удалось описать его в мельчайших подробностях. Вместо вывода можно было бы составить оду моторному маслу, но мы ограничимся малым, сказав очевидное: следите за тем, что льете в системы двигателя. Это, разумеется, не решит абсолютно всех потенциальных проблем вроде перегрева или перегрузки, но определенно поможет мотору прожить более долгую и счастливую жизнь.
Опрос
Приходилось ли вам ремонтировать блок цилиндров на своем автомобиле?
Всего голосов:
www.kolesa.ru
Ремонт типовых деталей двигателей внутреннего сгорания
Категория:
Ремонт дорожных машин
Публикация:
Ремонт типовых деталей двигателей внутреннего сгорания
Читать далее:
Ремонт типовых деталей двигателей внутреннего сгорания
Срок службы двигателей дорожных машин обусловливается долговечностью его ответственных деталей, к которым отнесем следующие детали, восстанавливаемые в ремонтной практике: блок цилиндров, цилиндры, головка блока, шатуны, поршневые пальцы, коленчатый вал, распределительный вал, клапаны.
Ремонт блоков цилиндров. Блоки цилиндров дизельных двигателей изготавливают из серого чугуна твердостью НВ 180—240 со вставными мокрыми гильзами. Основными дефектами блоков цилиндров являются: трещины в рубашке охлаждения; пробоины; коробление поверхности сопряжения с головкой блока; износ или нарушение соосности гнезд под вкладыши коренных подшипников; износ отверстий под втулки толкателей и втулки распределительного вала; износ резьбовых отверстий.
Трещины и пробоины в зависимости от их размера и места расположения заделывают сваркой, постановкой заплат на болтах или заклепках, синтетическими материалами, пайкой латунью. Сварку лучше вести холодным способом, используя железо-никелевые электроды Ц4-ЗА. При этом не происходит отбеливание чугуна, а сварной шов хорошо обрабатывается обычным режущим инструментом. Сварку применяют для заделки трещин в более нагруженных местах.
Рекламные предложения на основе ваших интересов:
При короблении верхней плоскости блока цилиндроь более 0,15 мм производят шлифовку на плоскошлифовальных или вертикально-сверлильных станках, используя специальное приспособление.
После обработки привалочной плоскости необходимо с той же установки углубить на такой же размер выточки под бурты гильз цилиндров.
При износе или нарушении соосности гнезд под вкладыши коренных подшипников вследствие износа и деформации крышек и поверхностей постелей опорные поверхности крышек шлифуют на плоско-шлифовальном станке, уменьшая высоту на 0,3—0,5 мм. Затем крышки устанавливают на место, затягивают гайками и растачивают гнезда на станке РР-4 или на универсальных горизонтально-расточных станках типа 2613 или 2А613.
Восстанавливают соосность путем расточки гнезд на увеличенные ремонтные размеры (через 0,25 мм) с постановкой вкладышей увеличенного наружного размера.
Можно восстанавливать изношенные поверхности отверстий под вкладыши, нанося на них составы на основе эпоксидных смол.
При небольшом износе отверстий под втулки толкателей и втулки распределительного вала иногда можно ограничиться постановкой в эти гнезда деталей нормальных размеров, используя эпоксидную смолу.
При большом износе гнезда растачивают на расточных станках, запрессовывают в них втулки увеличенных по наружному диаметру размеров и развертывают эти втулки до нормальных размеров.
При износе и срыве резьбы в отверстия рекомендуется ставить резьбовые переходные втулки, проволочные вставки или ступенчатые шпильки с резьбой увеличенного размера.
После ремонта блоки цилиндров подвергают гидравлическому испытанию.
Ремонт гильз цилиндров. Гильзы цилиндров изготовляют из легированного чугуна СЧ21-40 с последующей термической обработкой. Твердость внутренней рабочей поверхности гильз должна быть не ниже HRC 40.
Основной дефект гильз — износ внутренней (рабочей) поверхности. Цилиндры при изнашивании приобретают овальность и конусность, поэтому их восстановление сводится к получению правильной цилиндрической формы рабочей поверхности и приданию ей надлежащего качества.
При износах цилиндров и увеличении зазора в сопряжении цилиндр — поршень выше допустимого их растачивают и хонингуют на следующий увеличенный ремонтный размер, после чего комплектуют по размерным группам с поршнями соответствующего диаметра.
Гильзы блоков тракторных двигателей имеют по одному ремонтному размеру Р1, увеличенному на 0,7 мм. Для всех автомобильных двигателей устанавливают в основном три ремонтных размера с интервалом 0,5 мм. Растачивают цилиндры на специальных вертикально-расточных станках типов 278Н, РП2, 2В-697, В68П. Гильзы растачивают в специальных приспособлениях. Расточенные гильзы и цилиндры подвергают окончательной обработке (доводке) хонингованием или раскаткой. Хонингование проводят на специальных вертикально-доводочных станках типа 3833М абразивными или алмазными брусками, закрепленными в специальной головке. Устройство станка обеспечивает автоматическое вращательное и возвратно-поступательное движение головки, заданное увеличение ее диаметра (разжим) за каждый цикл подъема и опускания.
Изношенные цилиндры блоков последнего ремонтного размера восстанавливают постановкой сухой гильзы, изготовленной из титано-медистого или марганцовистого чугуна. В расточенный блок запрессовывают гильзу, вновь ее растачивают и хонингуют на нормальный размер.
Рекомендуется гильзы перед запрессовкой охлаждать, а блок подогревать.
Ремонт головок цилиндров. Головки цилиндров дизельных двигателей изготавливают из серого или легированного чугуна марок СЧ24-44, СЧ15-32 и др. Основные дефекты головок цилиндров: трещины в рубашке охлаждения, трещины в перемычках между клапанными гнездами, деформация привалочных плоскостей, износ или срыв резьбы в резьбовых отверстиях, износ клапанных гнезд, нарушение посадок втулок клапанов в головке.
Процесс заделки трещин в рубашке охлаждения головок цилиндров аналогичен процессу заделки трещин в блоках цилиндров.
Трещины в перемычках между клапанными гнездами фрезеруют на горизонтально-фрезерном станке и заваривают ацетилено-газовой сваркой (горячий способ) или электродуговой сваркой (холодный способ).
При короблении более 0,15 мм плоскость прилегания к блоку фрезеруют и шлифуют с минимальным снятием металла.
При износе резьбы в отверстиях головки цилиндров резьбу шпилек смазывают клеем на основе эпоксидной смолы и шпильки завинчивают в резьбовые отверстия. При срыве резьбы в отверстиях головок эти отверстия рассверливают, нарезают увеличенную (ремонтную) резьбу и ставят ступенчатые шпильки.
Изношенные отверстия под свечи (в головках карбюраторных двигателей) ремонтируют постановкой переходных резьбовых втулок.
Рис. 83. Последовательность фрезерования клапанного гнезда
Износ клапанных гнезд является наиболее частой неисправностью головки цилиндров. При небольших износах клапанов и гнезд герметичность сопряжения может быть восстановлена притиркой клапанов к гнездам. При больших износах клапанных гнезд их ремонтируют, восстанавливая геометрическую форму, ширину фаски и ее расположение. Наиболее распространенным способом ремонта таких гнезд является фрезерование (рис. 83). Для этого применяют набор специальных фрез (зенковок). Черновой фрезой с углом 45 °Снимают слой металла на фаске гнезда до выведения следов износа. При этом ширина фаски увеличивается. Для того, чтобы уменьшить ширину фаски, нижнюю часть ее подрезают фрезой с углом 75°, а верхнюю — фрезой с углом 15°. Чистовой фрезой с углом 45° зачищают поверхность фаски и доводят окончательно ее ширину до требуемой величины.
Фрезерование производят вручную или на сверлильном станке. После фрезерования гнезд для обеспечения плотного прилегания к ним клапанов при сборке головки требуется притирка фаски клапана к гнезду. Притирку производят вручную при помощи специальной дрели или коловорота, пневматической дрелью или на притирочных станках, применяя пасту ГОИ.
Для предварительной проверки качества притирки клапанов на фаску клапана через 30—40° по окружности наносят карандашом метки, вставляют клапан в гнездо и провертывают его 2—3 раза. При удовлетворительной притирке метки должны стереться. При большом утопании клапана гнезда восстанавливают кольцеванием. Для кольцевания гнездо растачивают на сверлильном станке специальным прибором. Кольцо обычно изготовляют из чугуна, имеющего идентичный химический состав с основной деталью-головкой. Наружный диаметр кольца выдерживают таким, чтобы при запрессовке в гнездо создать натяг в пределах 0,20—0,25 мм.
Перед запрессовкой кольцо смазывают насыщенным раствором нашатыря. Кольцо запрессовывают в гнездо до упора на гидравлическом прессе. Затем гнезда обрабатывают комплектом конусных фрез, как указано выше.
Посадку втулок клапанов в головках блока восстанавливают клеевым составом на основе эпоксидной смолы без наполнителя. Состав наносят на втулки перед их запрессовкой. После окончания ремонта головки блока цилиндров испытывают на герметичность под давлением 0,4 МПа (4 кгс/см2) в течение 5 мин. Течь воды и потение при этом не допускаются. Плотность прилегания клапанов к гнездам в собранной головке проверяют специальным пневматическим прибором (рис. 84).
Рис. 84. Прибор для проверки качества притирки
Проверить герметичность прилегания клапана к гнезду можно, заливая во впускные и выпускные окна головки блока керосин. В течение 3 мин керосин не должен просачиваться через сопряжение фаска гнезда —фаска головки клапана.
Ремонт клапанов. Основные дефекты клапанов: износ фаски тарелки, стержня по диаметру и торцу, прогиб стержня.
Изношенный торец стержня шлифуют на станке типа СШК до выведения следов износа.
При износе стержня по диаметру его шлифуют до уменьшенного ремонтного размера, восстанавливают хромированием или остали-ванием с последующим шлифованием до номинального размера. Фаску тарелки шлифуют после шлифования стержня до выведения неровностей. В результате неоднократного шлифования рабочей фаски высота цилиндрического пояска головки клапана уменьшается. Согласно техническим условиям она должна быть не менее 0,5 мм.
Прогиб стержня клапана устраняют правкой на ручном прессе или при помощи приспособления.
Ремонт шатунов. Шатуны изготавливают из сталей 40, 45, 45Г, 45Г2 и других марок. Шатуны проходят термическую обработку — улучшение. Основные их дефекты: изгиб и скручивание, износ поверхностей отверстий верхней и нижней головок, поверхностей по плоскости разъема крышки, износ отверстий и опорных поверхностей под гайки и головки шатунных болтов.
Изгиб и скручивание шатуна устраняют правкой на специальных приспособлениях (рис. 85).
На некоторых ремонтных предприятиях после правки шатун подвергают термостабилизации. Для этого его нагревают до температуры 400—450 °С, выдерживают в течение 0,5—1 ч, после чего охлаждают на воздухе.
Рис. 85. Правка шатунов:
а — изогнутых; б — скрученных; 1 — приспособление; 2 — шатун; 3 — разводной винт; 4 — рычаги; 5—упорные накладки; 6 — зажимные гайки; 7 — тиски
Изношенную внутреннюю поверхность верхней головки шатуна растачивают на ремонтный размер и затем запрессовывают втулку увеличенного размера или омедненную. Изношенную поверхность отверстий нижних головок шатунов восстанавливают растачиванием с последующим хонингованием под номинальный размер. Чтобы создать припуск для растачивания, с плоскостей разъема шатуна и крышки снимают слой металла на фрезерных станках.
При значительных износах поверхности отверстий нижнюю головку шатуна в сборе с крышкой наплавляют в среде углекислого газа или вибродуговым способом. Затем отверстия растачивают на расточных или токарных станках.
На некоторых ремонтных заводах изношенные поверхности нижней и верхней головок шатуна, а также поврежденные плоскости разъема шатуна с крышкой восстанавливают осталиванием с последующей механической обработкой поверхностей.
Изношенные опорные поверхности под гайки и головки шатунных болтов фрезеруют до выведения следов износа. После фрезерования при сборке нижней головки шатуна следят, чтобы отверстие для шплинта шатунного болта не выступало за торцовую поверхность гайки. В противном случае поверхности наплавляют, а затем фрезеруют до нормального размера.
Опорные поверхности в крышке фрезеруют на вертикально-фрезерном станке концевой фрезой, а в шатуне — на горизонтально-фрезерном станке дисковой трехсторонней фрезой.
Ремонт поршневых пальцев. Поршневые пальцы изготовляют из стали 12ХНЗА, наружную поверхность подвергают цементации на глубину 0,8—1,3 мм. Твердость цементованной поверхности HRC 58.
Поршневые пальцы изнашиваются в сопряжениях с втулкой шатуна и с бобышкой поршня. Изношенные поршневые пальцы восстанавливают централизованно хромированием или раздачей с последующей термообработкой.
Изношенные поршневые пальцы ремонтного размера восстанавливают шлифованием до нормального размера.
Незначительно изношенные кулачки перешлифовывают с сохранением профиля кулачка. При этом высота подъема клапана не изменяется.
При значительном износе кулачков они могут быть восстановлены вибродуговой наплавкой или наплавкой электродами Т-590 и Т-620 на станках с копировальным приспособлением.
При необходимости наплавленный слой закаливают. После наплавки кулачки предварительно обрабатывают шлифовальным кругом по шаблону, а затем их подвергают круговому шлифованию по копиру с сохранением профиля.
Рекламные предложения:
Читать далее: Ремонт топливной аппаратуры
Категория: — Ремонт дорожных машин
Главная → Справочник → Статьи → Форум
stroy-technics.ru
Техническое обслуживание и ремонт двигателя автомобиля.
Техническое обслуживание ДВС заключается в его внешней очистке, контрольном осмотре, общем диагностировании и диагностировании и регулировании его систем.
Внешнюю очистку ДВС проводят путем его предварительной обдувки сжатым воздухом с последующей протиркой матерчатыми концами, смоченными в керосине или дизельном топливе.
Контрольный осмотр ДВС состоит из визуального установления его комплектности и мест подтекания масла, топлива и охлаждающей жидкости, контроля крепления двигателя и его систем, опробования пуска. При пуске двигателя обращают внимание на легкость запуска, продолжительность которого не должна превышать 20 с. Повторный запуск проводят через 1… …2 мин. При контрольном осмотре ДВС выявляют его очевидные неисправности.
Общее диагностирование ДВС позволяет оценить техническое состояние всего двигателя по некоторым обобщенным его параметрам как с качественной, так и в ряде случаев с количественной стороны.
Общее диагностирование двигателя можно проводить как на основе анализа различных внешних симптомов, характеризующих его работу, так и путем инструментального исследования. Наиболее распространены методы, основанные на анализе цвета выхлопных газов, развиваемых двигателем шумов, содержащихся в картерном масле примесей.
Анализ цвета выхлопных газов. Данный метод основан на зависимости между техническим состоянием отдельных частей двигателя и цветом выхлопных газов.
Анализ шумов, развиваемых двигателем. Этот метод осуществляют путем прослушивания двигателя. Механические шумы улавливаются достаточно хорошо. Поэтому оценка технического состояния двигателя по характеру шумов довольно широко распространена в эксплуатационных условиях, хотя она в определенной степени субъективна и требует высокой квалификации.
Анализ содержащихся в картерном масле примесей. Весьма перспективен и точен метод общего диагностирования технического состояния двигателя по анализу попадающих в масло продуктов изнашивания его деталей.
Текущий ремонт двигателей производится при наличии следующих дефектов: нарушении регулировки клапанов; неисправности прокладок крышки клапанов и головки блока; неисправности головки блока; стуке коренных и шатунных подшипников; повышенном расходе масла, пропуске газов; падении мощности; пониженном давлении масла в системе смазки двигателя. Устранение первых четырех дефектов производится без снятия двигателя с машины.
Для замены цилиндропоршневой группы, деталей кривошипно-шатунного механизма, системы смазки двигатель необходимо снимать с машины.
При одновременном наличии нескольких дефектов (стуке клапанов, подшипников, падении мощности двигателя и т. д.) и наработке близкой к наработке до капитального ремонта двигатель проходит наружную мойку и направляется на склад оборотных агрегатов для сдачи на технический обменный пункт для прохождения капитального ремонта на ремонтном заводе.
Разборка и сборка двигателей при текущем ремонте производятся после наружной мойки и очистки на агрегатном участке. Разборку ведут на универсальных или специализированных стендах.
Ремонт кривошипно-шатунного механизма. Кривошипно-шатунный механизм двигателя состоит из цилиндропоршневой и кривошипно-ша- тунных групп и включает следующие детали: цилиндр, поршень, поршневые кольца, поршневой палец, шатун, коленчатый вал, шатунные и коренные подшипники, маховик. Внешние признаки износа деталей этой группы — дымный выхлоп отработавших газов, повышенный расход масла, падение давления в системе смазки, стуки. Стуки возникают в результате естественного изнашивания трущихся поверхностей деталей кривошипно-шатунного механизма и увеличения зазора между ними. Увеличение^ зазора между деталями цилиндропоршневой группы приводит к снижению давления в цилиндрах (компрессии) и повышенному расходу масла. Увеличение зазора в подшипниках коленчатого вала вызывает снижение давления масла в главной масляной магистрали.
Поверхности цилиндров изнашиваются неравномерно как вдоль оси, так и по окружности. По окружности цилиндры изнашиваются сильнее в плоскости качания шатуна, а вдоль оси — в зоне компрессионных колец. Поршни и поршневые кольца, как правило, не ремонтируют, а заменяют новыми. Шатуны двигателя при наличии трещин, изгибов, скручивания, больших износов под втулку пальца и вкладыши выбраковываются и заменяются новыми. Для шатунов всех марок двигателей допускается изгиб 0,08 мм, а скручивание 0,12 мм на длине 100 мм.
Коленчатый вал изнашивается в зоне коренных и шатунных шеек. Для восстановления формы шеек и их чистоты, поверхности шлифуют под ремонтный размер. Для коленчатых валов тракторных двигателей принято четыре основных ремонтных размера с интервалом 0,75 мм для шатунных и 0,5 мм для коренных шеек. Для автомобильных валов интервал составляет 0,25 мм для коренных и шатунных шеек. При изломах, трещинах, погнутости коленчатый вал выбраковывается.
При ремонте поршни и шатуны подбираются по массе. Разность в массе приводит к дисбалансу, повышенной вибрации и снижению долговечности двигателя. Перед сборкой поршни нагревают до 75 … 85° С и соединяют с шатунами путем запрессовки пальца.
Коленчатый вал собирают в приспособлении. При сборке устанавливают шестерню привода масляного насоса. Шестерню располагают метками наружу. Масляные каналы продувают сжатым воздухом. К валу подбирают комплект шатунных и коренных вкладышей.
Ремонт головки цилиндров и деталей газораспределительного механизма. Основные дефекты головок цилиндров следующие: трещины, износ клапанных гнезд, коррозионный износ головок из алюминиевых сплавов, износ или срыв резьбы, коробление.
Крупные трещины обнаруживаются визуально, мелкие —при гидравлическом испытании давлением воды 0,4 МПа в течение 3 … 5 мин, при этом на поверхности не должно быть течи. Головка выбраковывается при трещинах, проходящих через отверстия под шпильки, направляющих клапанов или перемычки гнезд. Трещины ремонтируют электродуговой сваркой или эпоксидными смолами. При короблении плоскость прилегания головки к блоку фрезеруют и притирают на притирочной плите. Коробление плоскости допускается до 0,15 мм.
Клапанные гнезда восстанавливают фрезерованием с углом режущей кромки зенковки 15, 45 и 75°. Порядок фрезерования следующий: черновой фрезой с углом 45° снять фаску до выведения следов износа, фрезой с углом 15° снять с поверхности гнезд слой металла до образования четкой верхней кромки фаски, расположенной под углом 45°, чистовой фрезой с углом 45° зачистить фаску до получения рабочей фаски шириной 2 … 3 мм. После установки клапана фаска на его тарелке должна полностью перекрывать фаски гнезда без зазоров.
В клапанах изнашиваются фаски, тарелки и стержни по диаметру и торцу. Эти дефекты устраняются шлифовкой. После шлифовки для полного прилегания тарелки клапана к гнезду производят притирку с использованием пасты ГОИ или смеси наждачного порошка зернистостью 240 … 280 с дизельным маслом.
Ремонт системы смазки. Основные неисправности системы смазки относятся к износу и повреждению деталей масляного насоса и центрифуги. Перед разборкой масляный насос проверяется на стенде КИ-5278 или КИ-1575; при обнаружении неисправностей и утрате параметров насос подлежит разборке и замене неисправных деталей. После сборки насос проверяется на стенде и производится регулировка перепускного клапана на давление 0,6 … 0,8 МПа.
Обкатка и испытание двигателей. Собранный двигатель обкатывают и испытывают на специальных стендах. Цель обкатки — приработка трущихся поверхностей и выявление дефектов, возникающих в результате отклонений от технических условий. Основная приработка деталей двигателя происходит в первые 2 … 3 ч и полностью завершается через 40 … 60 ч. Поэтому обкатку проводят в два этапа: сначала на стендах по режиму, указанному в технических условиях для двигателя данной марки, а затем в условиях эксплуатации с пониженной нагрузкой. Автомобильные и тракторные двигатели подвергают холодной и горячей обкатке (без нагрузки и под нагрузкой) на универсальных стендах КИ-1363Б и КИ-1218А. (СМД-14, ЯМЭ-236, ЯМЭ-238, СМД-60 И др.).
Холодную обкатку автомобильных карбюраторных двигателей проводят в течение 20 мин, а дизельных — 80 … 100 мин сначала с выключенной, а затем и с включенной компрессией по режиму, установленному техническими условиями. Во время холодной обкатки проверяют давление масла в магистрали, при этом температура воды в системе охлаждения поддерживается на уровне 80° С. При обкатке не допускаются резкие шумы и стуки, а также подтекание масла, топлива и воды. После окончания холодной обкатки двигатель осматривают и подтягивают гайки крепления головки цилиндров.
При горячей обкатке включают подачу топлива и электродвигателем стенда запускают двигатель. В течение 10 … 15 мин его обкатывают без нагрузки при пониженной частоте вращения вала, а затем 10 … 15 мин при повышенной частоте вращения вала. При этом проверяется давление масла, регулируются обороты холостого хода, прослушивается стетоскопом двигатель в зонах возможных стуков.
Под нагрузкой двигатели обкатывают по режиму, установленному техническими условиями. Максимальная нагрузка не должна превышать 85% номинальной. В процессе обкатки замеряется мощность двигателя и расход топлива.
60.Техническое обслуживание и ремонт подвесок автомобиля.
Наиболее часто машине требуется диагностика подвески. Это связано с тем, что ходовая часть автомобиля в процессе езды принимает на себя основную нагрузку.
ТО подвески. После первых 2000 км, а затем через каждые 10000 пробега, а также после сильных ударов о препятствия на дороге (попадание в ямы, удары о случайные предметы или камни и т.п.), проверяют состояние деталей передней подвески осмотром снизу а/м после установки его на подъемнике, эстакаде или на смотровой яме.
Осмотром проверяют, нет ли на деталях подвески трещин или следов задевания о дорожные препятствия или кузов, деформаций рычагов, растяжек штанги стабилизатора, ее стоек и элементов передка кузова в мостах крепления узлов и деталей подвески. Деформация деталей подвески и, прежде всего растяжек, реактивных штанг и деталей передка кузова нарушает углы стыковки колес и может привести к невозможности их регулировки. При обнаружении таких деформаций необходимо проверить углы установки колес.
Ремонт подвески включает в себя проверку ее технического состояния, разборку, замену и ремонт деталей, сборку и регулировку углов установки передних колес. Ремонт деталей подвески включает обычно ремонт амортизационной стойки или амортизатора, а также перепрессовку сайлент-блоков рычагов подвески. Проверка технического состояния передней подвески производится как при появлении, так и в профилактических целях (обычно при очередном техническом обслуживании а/м), поскольку исправность подвески непосредственно связана с безопасностью движения.
Осмотр подвески производится снизу а/м, для чего удобнее всего вывесить его на подъемнике или установить на канаву с подъемником. При наличии деформаций и трещин на рычагах и других элементах подвески, повреждении защитных чехлов шаровых шарниров (сайлент-блоков), а также подтекание жидкости из амортизаторных стоек и амортизаторов. При наличии деформаций и трещин на рычагах и других элементах подвески, повреждения защитных чехлов шаровых шарниров, а также повышенном износе упругих элементов, они подлежат замене. Износ резинометаллических шарниров определяется по их проседанию и выпучиванию из них резины. При осмотре одновременно производится проверка креплений элементов подвески путем их подтяжки.
Проверка шаровых шарниров рычагов передних подвесок производится по люфтам в шарнирах при покачивании вывешенного колеса в вертикальной плоскости. На переднеприводных люфт контролируется по изменению расстояния между нижним рычагом и защитным кожухом тормозного ушка при вывешенном и снятом со ступицы колесе.
Проверка осадки пружин передней подвески производится после установки а/м на ровной горизонтальной площадке при полной его нагрузке. При этом измеряется расстояние от поверхности площадки до передней балки или поперечины кузова.
Проверка амортизаторов и амортизаторных стоек на а/м на специальном диагностическом стенде, при его отсутствии можно проверить амортизатор, раскачав кузов руками нажатием сверху на край крыла со стороны проверяемого амортизатора. После прекращения приложения усилий руками положение кузова должно стабилизироваться за 1-2 хода.
infopedia.su