Техническое обслуживание двигателя автомобиля
Категория:
Техническое обслуживание автомобилей
Публикация:
Техническое обслуживание двигателя автомобиля
Читать далее:
Техническое обслуживание двигателя автомобиля
При ежедневном обслуживании проверяют работу двигателя, соединения шлангов радиатора и топливопроводов (не нарушена ли герметичность), уровень масла и при необходимости доливают масло в картер двигателя.
При первом техническом обслуживании проверяют, не нарушена ли герметичность системы смазки, охлаждения двигателя, крепление на нем приборов; обнаруженные неисправности устраняют. Проверяют крепление двигателя к раме и, если оно ослабло, подтягивают гайки крепления опор.
При втором техническом обслуживании выполняют работы первого технического обслуживания и дополнительно проверяют и закрепляют радиатор и его облицовку, жалюзи, распорную тягу и капот, водяной насос, вентилятор, впускной и выпускной трубопроводы, трубу глушителя, картер двигателя (поддон) и отъемную часть картера сцепления, нижние и боковые брызговики двигателя.
Рекламные предложения на основе ваших интересов:
Проверяют работу компрессора, его крепление на двигателе и натяжение приводного ремня. При необходимости закрепляют компрессор и регулируют натяжение ремня. Проверяют, не нарушена ли герметичность соединения головки с блоком цилиндров, при необходимости подтягивают гайки и болты ее крепления. Проверяют компрессию в цилиндрах двигателя. Через одно ТО-2 проверяют и при необходимости регулируют зазоры между клапанами и толкателями.
Определение компрессии двигателя
Величину давления в конце такта сжатия в цилиндрах двигателя (компрессию) определяют с помощью компрессометра. Он состоит из манометра, соединительной трубки и наконечника с обратным клапаном. Компрессометр для дизельного двигателя, кроме того, снабжают спускным краном для сброса давления после измерения.
При определении компрессии карбюраторного двигателя число оборотов в минуту коленчатого вала должно быть 180—200. Перед проверкой двигатель прогревают до 70—80° С, вывертывают свечу зажигания первого цилиндра и полностью открывают воздушную и дроссельную заслонки карбюратора. Затем плотно прижимают наконечник к кромке отверстия и проворачивают коленчатый вал двигателя стартером на 10—12 оборотов, чтобы компрессометр зафиксировал максимальное давление в цилиндре, и записывают показания.
Таким же образом замеряют компрессию в остальных цилиндрах двигателя. Разница в величине компрессии по отдельным цилиндрам не должна быть более 1 кГ/см2.
Проверка компрессии не позволяет без разборки двигателя выявить конкретную неисправность (поломку или пригорание поршневых колец, повреждение прокладки головки блока цилиндров и т. д.). С несравненно большей достоверностью можно судить об износе деталей цилиндра — поршневой группы, о состоянии клапанов и прокладки головки блока цилиндров по величине утечки сжатого воздуха из цилиндров двигателя, по показаниям прибора К-69М, выпускаемого Новгородским заводом объединения Росавтоспецоборудование (бывший трест ГАРО).
Проверка и регулировка тепловых зазоров в газораспределительном механизме
Величина зазоров между клапанами и толкателями (коромыслами) должна обеспечивать плотную посадку и бесшумную работу клапанов. В процессе работы величина зазоров изменяется вследствие износа сопрягаемых деталей газораспределительного механизма, что приводит к нарушению его нормальной работы. Так, при отсутствии зазора между клапаном и толкателем (коромыслом) нарушается плотность посадки клапанов, подгорают клапаны и их седла, двигатель преждевременно изнашивается вследствие перебоев или даже прекращения работы того цилиндра, клапан которого не имеет плотной посадки.
При увеличении тепловых зазоров усиливается стук клапанов, ухудшаются наполнение цилиндров свежей горючей смесью и очистка их от отработавших газов, что затрудняет пуск двигателя и приводит к снижению мощности. Дополнительными признаками неплотной посадки впускных клапанов являются вспышки в карбюраторе, а неплотной посадки выпускных — выстрелы в глушителе. В
Следует иметь в виду, что перед регулировкой зазоров между клапанами и толкателями двигатель ЗИЛ-120 необходимо прогреть.
Регулировать тепловые зазоры клапанов на двигателе автомобиля ГАЗ-51А можно в холодном состоянии.
Тепловые зазоры клапанов двигателей автомобилей ЗИЛ-164А, ЗИЛ-130, ГАЗ, М-21 «Волга» проверяют двумя щупами. Зазор считается установленным правильно, если щуп, толщина которого равна нижнему пределу величины зазора, свободно проходит, а щуп толщиной, соответствующей верхнему пределу, не проходит. Например, для двигателя ЗИЛ-130 щуп 0,40 мм Должен проходить, а щуп 0,45 мм не должен входить в зазор.
У двигателя автомобиля ГАЗ-51А клапаны нижнего расположения. Перед регулировкой тепловых зазоров клапанов проделывают следующее:
Болты и гайки крепления головки блока цилиндров затягивают в определенном порядке: начинают с середины и последовательно подтягивают болты (гайки), расположенные от средних справа и слева. Подтяжку ведут в два приема: предварительно и окончательно.
У автомобилей ЗИЛ-130 болты и гайки крепления головок блока цилиндров подтягивают обязательно на горячем двигателе, а у автомобилей «Москвич-408», ГАЗ-21, «Волга», ГАЗ-51А, ГАЗ-53А — на холодном двигателе.
Проверка и регулировка натяжения ремня вентилятора
Во время работы двигателя ремень вентилятора постепенно вытягивается, натяжение его слабеет и он начинает проскальзывать по шкиву. Проскальзывание ремня вызывает замедленное вращение вентилятора, вала водяного насоса и генератора, вследствие чего ухудшается охлаждение двигателя, снижается сила зарядного тока.
Слишком сильное натяжение ремня также вредно, так как при этом увеличивается нагрузка на подшипники вентилятора и они быстро изнашиваются; кроме того, быстро изнашивается и ремень.
Натяжение ремня вентилятора проверяют следующим образом.
Прикладывают к наружной поверхности ремня в точке, расположенной на одинаковом расстоянии от шкивов вентилятора и коленчатого вала, линейку (рис. 148). Устанавливают миллиметровую линейку перпендикулярно линейке, упирая ее в середину ветви ремня, затем нажимают линейкой на ремень и замечают деление, с которым совмещается плоскость линейки; оно покажет величину прогиба ремня.
Для регулировки натяжения ремня ослабляют болты крепления генератора на кронштейне и болт крепления генератора в упорной планке. Затем, поворачивая генератор относительно оси нижних болтов его крепления, отодвигают генератор от блока цилиндров или, наоборот, приближают его к блоку, регулируя прогиб ремня. Потом затягивают болт крепления генератора в упорной планке и болты крепления генератора на кронштейне и повторно проверяют натяжение ремня.
Рис. 1. Порядок подтяжки гаек крепления головки блока цилиндров
Рис. 2. Проверка натяжения ремня вентилятора:
1 — деревянная линейка, 2 — масштабная линейка, 3 — шкив компрессора, 4 — шкив вентилятора, 5 — шкив генератора, 6’ — шкив коленчатого вала
Регулировка натяжения приводных ремней двигателя ЗИЛ-130
Регулировка натяжения ремня привода генератора. Для этого ослабляют ключом гайку крепления генератора к планке, затем, поворачивая генератор, добиваются правильного натяжения ремня. При нажатии рукой на ремень в средней части прогиб должен быть 10—15 мм.
Рис. 3. Регулировка натяжения ремней двигателя ЗИЛ-130:
1 — шкив коленчатого вала, 2— гайка, 3—плавка, 4 — шкив генератора, 5, 13 — шкив компрессора, 6 — болт, 7 — шкив водяного насоса, 8 — кронштейн, в — шкив насоса гидравлического усилителя рулевого управления, 10 — болты кронштейна, 11 — внутренний обод шкива компрессора, 12 — наружный обод шкива компрессора
Регулировка натяжения ремня компрессора производится в следующем порядке. Ключом ослабляют три болта, поворачивают рукой наружный обод шкива компрессора налево, а внутренний ободнаправо, после чего, поворачивая вместе ободы шкива, подводят в сторону вентилятора один болт так, чтобы ремень вышел из зева шкива, и завертывают ключом в этом положении, затем то же самое проделывают с двумя остальными болтами и закрепляют их окончательно.
При нормальном натяжении прогиб ремня между шкивами компрессора и водяного насоса при нажатии рукой должен быть 10—15 мм.
Натяжение ремня привода насоса гидравлического усилителя рулевого управления. Для натяжения ремня ослабляют ключом болты крепления кронштейна и, смещая гидравлический насос в противоположную от вентилятора сторону, добиваются, чтобы при нажатии рукой прогиб ремня между шкивами водяного насоса и насоса гидравлического усилителя рулевого управления был 15—20 мм.
—
Основные признаки неисправностей двигателя следующие: стуки в подшипниках коленчатого вала; резкие стуки поршней в цилиндрах и деталей механизма газораспределения; падение давления масла в системе двигателя при температуре воздуха выше 0°С и неустойчивая работа двигателя на холостом ходу; работа двигателя с перебоями или перегревом; повышенное дымление при работе прогретого двигателя на различных эксплуатационных режимах; подтекание жидкости в соединениях системы охлаждения. Основные неисправности двигателя обусловливаются неисправностями кривошипно-шатунного и газораспределительного механизмов.
Для кривошипно-шатунного механизма наиболее характерны износы поршневых колец, поршней, поршневых пальцев, стенок цилиндров, шеек коленчатого вала и его подшипников.
Износ поршневых колец, поршней и стенок цилиндров, а также пригорание колец в канавках приводят к снижению компрессии и падению мощности двигателя. Признаки этих неисправностей: повышенное дымление выпуска, увеличение расхода топлива и масла, которое, однако, может быть вызвано также закупориванием маслоотводящйх каналов в маслосъем-ных кольцах и соответствующих канавках поршня, что происходит иногда после небольшого пробега в результате применения масел низкого качества.
Резкий металлический стук, прослушиваемый на холостом ходу двигателя, усиливающийся при увеличении подачи топлива, является признаком поломки клапанных пружин или заедания клапанов. Стуки, хорошо прослушиваемые при значительных изменениях подачи топлива с увеличением нагрузки на двигатель, являются следствием изношенности поршневых пальцев, втулок верхней головки шатуна и бобышек поршня. Появление глухих стуков, хорошо различимых при резком увеличении подачи топлива на холостом ходу двигателя, является признаком увеличения зазора в коренных и шатунных подшипниках коленчатого вала в результате износа антифрикционного слоя вкладышей и шеек коленчатого вала.
При неисправностях кривошипно-шатунного механизма двигатель подлежит ремонту. При этом отдельные детали (поршневые кольца, вкладыши и др.) в случае их значительного износа заменяют, а основные детали (блок цилиндров, коленчатый вал) ремонтируют.
Основные неисправности газораспределительного механизма заключаются в износе рабочих поверхностей клапанов и их гнезд, что влечет за собой неплотное закрытие клапанов, падение мощности двигателя, появление перебоев при работе под нагрузкой с малой частотой вращения коленчатого вала, а также стуки в приводе клапанов.
Повышенные зазоры в клапанах, определяемые по характер-пому металлическому стуку, приводят к падению мощности двигателя, затрудняют его пуск. Признаком увеличенного зазора является металлический стук высокого тона, хорошо прослушиваемый на фоне общего глухого шума в зоне расположения клапанного механизма. Уменьшенные зазоры в клапанах вызывают понижение компрессии и перегрев двигателя, что также ведет к падению его мощности.
Для поддержания механизма газораспределения в исправном состоянии необходимо следить за правильной величиной зазоров между стержнями клапанов и носками коромысел. При значительном износе рабочих фасок клапанов и седел клапанов их ремонтируют шлифовкой.
Основные неисправности системы охлаждения следующие: подтекание жидкости, уменьшение интенсивности работы центробежного насоса и вентилятора вследствие ослабления натяжения приводных ремней (неисправности в работе гидромуфты у двигателя ЯМЗ-740), засорение пространства между трубками радиатора, ухудшение отвода от них тепла. Эти неисправности приводят к нарушению теплового режима и перегреву двигателя.
Для поддержания системы охлаждения в исправности необходима тщательная проверка герметичности всех соединений, контроль за натяжением приводных ремней, своевременная промывка системы охлаждения.
Неисправности системы смазки определяют по падению давления масла, увеличению дымности выпуска со специфическим цветом отработавших газов (синеватый оттенок).
Неисправности системы смазки приводят к недостаточной подаче масла к трущимся поверхностям вследствие падения вязкости масла или засорения масляных фильтров и маслопроводов. Кроме того, ухудшение смазки может явиться следствием выдавливания масла, обладающего недостаточной вязкостью, через увеличившиеся зазоры в сопряжениях трущихся деталей. Большое влияние на работу системы смазки и ее исправность оказывает качество применяемого масла, которое должно соответствовать требованиям заводов-изготовителей двигателей.
Обязательным условием сохранности двигателя является поддержание нормального уровня масла в картере. Резкое снижение уровня масла может привести к уменьшению подачи масла к трущимся поверхностям; при избытке масло сгорает с выделением характерного синеватого дыма. Сгорание масла помимо его перерасхода ведет к усиленному отложению нагара. Для обеспечения нормальной работы системы смазки двигателя необходимо следить за уровнем масла в картере и при необходимости доливать масло. Во время работы следить за давлением масла по указателю, имеющемуся на щитке приборов.
Кроме серьезных неисправностей, вызванных нарушением работоспособности основных механизмов двигателя в процессе эксплуатации автомобиля, могут появиться другие отдельные нарушения нормальной работы двигателя. Как правило, такие неполадки легко устраняют проведением необходимых операций по уходу и регулировке. К ним относятся главным образом перебои в работе отдельных цилиндров, которые могут быть вызваны засорениями и неполадками в системе питания, перегрез двигателя, связанный с неисправностями системы охлаждения.
Двигатель ЯМЗ-236 работает иногда «вразнос» или не останавливается при прекращении подачи топлива. Причина этой неисправности заключается в неправильной работе регулятора частоты вращения вала двигателя, иногда причиной может быть попадание избыточного количества масла в цилиндры двигателя.
Другой характерной неисправностью дизельных двигателей является чрезмерная дымность выпуска, которую нельзя допускать, так как она вызывает значительное засорение окружающей среды и отравление ее токсичными веществами, содержащимися в отработавших газах.
Помимо неисправностей топлнвоподающей системы причиной сильного дымления могут быть загрязнение воздушного фильтра, перегрев двигателя, разжижение топлива маслом.
Основные работы, выполняемые при техническом обслуживании
При ежедневном техническом обслуживании (ЕО) проверяют, нет ли подтекания охлаждающей жидкости и топлива. Перед пуском двигателя следует проверить уровень жидкости в радиаторе, масла в картере, наличие топлива в баке. После пуска двигателя прослушивают его работу на холостом ходу, проверяют давление масла по указателю.
При первом техническом обслуживании (ТО-1) кроме работ, выполняемых при ежедневном уходе, выполняют ряд дополнительных операций.
По системе охлаждения проверяют состояние и действие шторок радиатора, натяжение приводных ремней генератора, насоса, вентилятора.
По системе смазки доливают или заменяют масло в картере в соответствии с графиком смазки, проверяют соединения маслопроводов, крепление фильтров и масляного радиатора, а у двигателей, имеющих центробежный фильтр очистки масла, снимают фильтр и промывают ротор, колпак и сетку.
При втором техническом обслуживании (ТО-2) помимо работ, выполняемых ежедневно и при ТО-1, дополнительно проверяют затяжку гаек крепления передней и задней опор двигателя; герметичность соединения приборов систем охлаждения и смазки; состояние и действие термостата.
Из контрольно-регулировочных работ выполняют те, необходимость в которых выявилась при осмотре двигателя.
Техническое обслуживание необходимо выполнять в соответствии с заводскими инструкциями по эксплуатации двигателей соответствующих моделей автомобилей.
Приемы выполнения работ по техническому обслуживанию двигателя
Проверка уровня масла в картере. Уровень масла в картере двигателя определяют по меткам на маслоизмерительном стержне, который нужно предварительно вывернуть из резьбовой части трубки. Проверяют не ранее чем через 5 мин после остановки двигателя. Доливают масло до отметки В на масло-измерительном стержне. Заменяют масло в картере двигателя при нормальных условиях работы в среднем через 100 ч работы (3000—3500 км пробега автомобиля), приурочивая смену к очередному техническому обслуживанию.
Проверка давления масла в системе смазки двигателя. Давление масла проверяют при его установившейся работе по указателю давления масла. Нормальное давление в системе смазки большинства дизельных двигателей составляет 0,45— 0,5 МПа (при работе двигателя с номинальной частотой вращения коленчатого вала). Давление масла может резко упасть, если редукционный клапан засорился и из-за этого нарушилась его герметичность.
Проверка фильтров очистки масла и клапанов системы смазки. У двигателей, имеющих фильтры со сменными элементами, рекомендуется промывать последние при очередной смене масла. С этой целью фильтрующий элемент вынимают из колпака и удаляют с него поверхностные отложения наружной очисткой жесткой металлической щеткой и промывкой в дизельном топливе. После очистки и промывки сменный фильтрующий элемент следует продуть сжатым воздухом. Меняют фильтрующие элементы при очередном ТО-2.
У фильтров центробел<ной очистки масла промывают ротор, предварительно вынув его из корпуса.
Перепускной, редукционный и сливной клапаны промывают в случае их засорения. Для этого их вывертывают, предварительно сняв замочную шайбу, а затем, не разбирая, промывают в дизельном топливе.
Проверка компрессии в цилиндрах. Выполняется как контрольно-регулировочная работа в случае ухудшения работы двигателя (плохая приемистость, падение мощности). Проверку выполняют при помощи компрессометра со шкалой от 0 до G МПа, который поочередно устанавливают в каждый цилиндр вместо форсунки. Компрессию проверяют у прогретого двигателя (температура охлаждающей жидкости не менее 80 °С) при минимальной частоте вращения коленчатого вала 500— 600 мин-1. При частоте вращения 500 мин-1 компрессометр должен показывать давление не менее 3,0 МПа. Разница в величине давления отдельных цилиндров не должна превышать 0,2 МПа.
В случае резкого отклонения давления от указанных выше норм необходимо выявить причину, вызвавшую это отклонение. Одна из таких причин — негерметичность соединения головки цилиндров с блоком.
Проверка крепления головок цилиндров к блоку. Степень затяжки гаек или болтов, крепящих головки цилиндров к блоку, проверяют, пользуясь ключом с динамометрической рукояткой, которая представляет собой стержень, имеющий на одном конце головку для установки сменных торцовых ключей, а на другом — шкалу и рукоятку. Шкала градуирована от 0 до 300 Н • м в обе стороны от нуля.
При затяжке резьбового соединения стрелка, связанная с головкой, показывает на шкале величину приложенного момента. Величина этого момента для двигателей ЯМЭ-236 и ЯМЭ-238 должна находиться в пределах 22—24 кгс • м.
Затягивают гайки в определенной последовательности в два приема: сначала предварительно, прилагая небольшое усилие, а затем полностью с указанным крутящим моментом.
Перед завертыванием резьбу болтов рекомендуется смазать графитовой смазкой.
Регулировка зазора между коромыслом и торцом стержня клапана. Зазор проверяют плоским щупом при появлении стуков в клапанном механизме. Проверяют зазоры на холодном двигателе между торцом стержня клапана и носком коромысла при полностью закрытом клапане.
У двигателей ЯМЭ-236 и ЯМЭ-238 тепловые зазоры у впускных и выпускных клапанов одинаковые. Они должны находиться в пределах 0,25—0,30 мм. У двигателя ЯМЗ-740 эти зазоры должны иметь следующие значения: для впускного клапана 0,15—0,20 мм, для выпускного клапана 0,20—0,25 мм. Из-за возможного биения сопрягаемых деталей распределительного механизма у двигателей, находящихся в эксплуатации, зазоры могут быть несколько увеличены (0,25—0,35 мм).
Регулируют тепловые зазоры в клапанах следующим образом. Выключив подачу топлива и сняв крышку головки цилиндров, сначала динамометрическим ключом проверяют затяжку болтов крепления стоек осей коромысел. Момент их затяжки должен быть равен 120—150 Н-м. Поршень в цилиндре, у которого проверяют зазор клапанов, подводят в в.м.т., соответствующую кониу хода сжатия до полного закрытия впускного клапана. При таком положении проверяют щупом величину зазора.
Для регулировки зазора отпускают контргайку регулировочного винта и вращают в нужном направлении регулировочный болт на коромысле до получения требуемого зазора. После регулировки затягивают контргайку и еще раз проверяют величину зазора.
Рекомендуется регулировать зазоры у клапанов отдельных цилиндров в соответствии с порядком работы двигателя. После регулировки клапанов прослушивают работу двигателя и при обнаружении ненормального стука клапанов снова проверяют их регулировку.
Проверка натяжения приводных ремней. Натяжение ремней проверяют, нажимая большим пальцем руки на соответствующую ветвь ремня посередине между шкивами с усилием 40—50 Н. При этом прогиб ремня должен составлять 10—15 мм.
У двигателей ЯМЭ-236 и ЯМЭ-238 натяжение ремня привода водяного насоса регулируют, удаляя или добавляя стальные прокладки между ступицей и боковиной шкива. Ремень компрессора натягивают специальным натяжным устройством, состоящим из натяжного шкива и перемещающего винта. Вращая болт натяжного устройства, устанавливают необходимый прогиб ремня. Натяжение ремня генератора регулируют смещением самого генератора, предварительно ослабив болты крепления лап генератора и его планки.
У двигателя ЯМЗ-740 ремень привода генератора и водяного насоса должен прогибаться на 15—22 мм. Регулируют прогиб изменением положения оси генератора.
Проверка термостата и шторок. Исправность термостата легко определить по нагреву приемного патрубка верхнего бачка радиатора. Если этот патрубок начнет нагреваться лишь при температуре воды 50—60 °С в рубашке охлаждения блока, то термостат исправен. Для более точной проверки термостат снимают с двигателя и опускают в сосуд с водой, нагретой до 90 — 100 °С, а затем по мере остывания воды следят за температурой, соответствующей началу (80—86 °С) и полному закрытию (68—72 °С) клапана. Термостат, не отвечающий этим требованиям, заменяют.
Шторки радиатора проверяют на полное открытие и закрытие и их плотное прилегание.
Проверка уровня охлаждающей жидкости в системе охлаждения. Уровень охлаждающей жидкости следует проверять только на холодном двигателе ввиду значительного объемного расширения жидкости при повышении температуры.
У двигателей, имеющих расширительный бачок, нормальный уровень охлаждающей жидкости должен находиться между верхней кромкой наливной трубы и краном контроля уровня расширительного бачка. Проверка уровня жидкости осуществляется путем открытия крана контроля уровня, установленного на расширительном бачке. Если при этом из крана не потечет жидкость, то уровень является недостаточным и жидкость необходимо долить.
Слив охлаждающей жидкости из систем охлаждения и отопления. Сливать охлаждающую жидкость из систем охлаждения и отопления следует через сливные отверстия, расположенные в нижней части отводящего патрубка водяного трубопровода, в котле подогревателя, насосном агрегате подогревателя и на подводящей трубе отопителя. Для слива жидкости необходимо открыть кран системы отопления, снять паровоздушную пробку с горловины расширительного бачка и отвернуть конические пробки, закрывающие указанные выше сливные отверстия.
При кратковременном использовании в системе охлаждения воды вместо антифриза сливать ее следует только при рабочем положении кабины. Автомобиль при этом должен быть установлен на ровной площадке.
Заполнение системы охлаждения антифризом. Систему охлаждения заполняют антифризом при открытом кране системы отопления через заливную трубу расширительного бачка до уровня ее верхней кромки. Перед заполнением необходимо открыть паровоздушную пробку. Полное удаление оставшегося в системе воздуха происходит автоматически при работе двигателя после открытия термостатов. При этом уровень антифриза в расширительном бачке несколько понижается, но остается выше крана контроля.
Рекламные предложения:
Читать далее: Техническое обслуживание механизмов трансмиссии
Категория: — Техническое обслуживание автомобилей
Главная → Справочник → Статьи → Форум
stroy-technics.ru
Тема 2.5. Технология технического обслуживания и ремонта механизмов и систем двигателя.
Вопросы темы:
1. Отказы и неисправности двигателя. Общая диагностика ДВС
2. Диагностика технического состояния и техническое обслуживание газораспределительного механизма и цилиндропоршневой группы
3. ТО и ТР системы смазки и охлаждения двигателя
4. Диагностика технического состояния и техническое обслуживание системы зажигания двигателя
5. Диагностика технического состояния и техническое обслуживание системы питания двигателя
2.5.1. Отказы и неисправности двигателя. Общая диагностика ДВС.
Отказы и неисправности. При эксплуатации двигателя в цилиндропоршневой группе (ЦПГ), кривошипно-шатунном механизме (КШМ), газораспределительном механизме (ГРМ), вспомогательных узлах и агрегатах появляются дефекты, которые могут быть вызваны как естественным и ускоренным износом деталей, так и внезапным появлением дефектов, потерей работоспособности деталей. Практика эксплуатации отечественных легковых автомобилей показывает, что примерно 20% всех отказов приходится на двигатель и его системы.
К основным отказам и неисправностям КШМ относят: износ, заклинивание, разрушение вкладышей; деформацию постелей в блоке; деформацию коленчатого вала; деформацию, износ отверстий нижней головки шатуна; обрыв шатуна или шатунных болтов; износ втулки верхней головки шатуна; износ подшипников балансирных валов; заклинивание, разрушение подшипников балансирных валов.
Для ЦПГ характерны появление разрушений перемычек, трещин в поршне; прогорание днища поршня; износ поршней, колец, цилиндров, поршневых пальцев; разрушение поршневых колец; деформация юбки поршня, задиры на юбке и поверхности цилиндра, возникновение пробоин, трещин в цилиндре или блоке; коробление плоскостей блока; выпадение фиксаторов поршневого пальца в поршне.
Основными признаками неисправности КШМ и ЦПГ являются: падение компрессии в цилиндрах, появление посторонних шумов и стуков при работе двигателя; появление из маслозаливной горловины голубоватого дыма с резким запахом; увеличение расхода масла, разжижение моторного масла.
Существенный перечень отказов и неисправностей имеет ГРМ: износ седла, клапана и направляющих втулок; разрушение, прогар клапанов; разрушение пружин; износ подшипников распределительного вала; перегрев и разрушение подшипников распределительного вала; износ кулачков распределительного вала и толкателей; износ коромысел и их осей; разрушение седла клапана; заклинивание гидротолкателей; износ цепи (ремня) и звездочек (шкивов) привода распределительного вала; разрушение зубьев звездочек; заклинивание гидронатяжителя; износ плунжера натяжителя цепи; прогар головки блока цилиндров; трещина, пробоина в головке блока; коробление головки блока.
Признаками неисправности ГРМ являются стуки, вспышки в карбюраторе и хлопки в глушителе.
Общим признаком неисправностей КШМ, ЦПГ и ГРМ является повышение расхода топлива и снижения мощности двигателя.
К основным отказам и неисправностям вспомогательных узлов и агрегатов следует отнести: износ шестерен, корпуса маслонасоса; заклинивание маслонасоса; негерметичность, заклинивание редукционного клапана; разрушение, негерметичность маслоприемника; негерметичность насоса охлаждающей жидкости; разрушение уплотнения и подшипника насоса охлаждающей жидкости; износ, разрушение подшипников и уплотнений турбокомпрессора.
2.5.2. Диагностика технического состояния и техническое обслуживание газораспределительного механизма и цилиндропоршневой группы.
Состояние цилиндропоршневой группы и клапанного механизма проверяют по давлению в цилиндре в конце такта сжатия. Состояние цилиндропоршневой группы и клапанного механизма можно проверить, измеряя утечку сжатого воздуха, подаваемого в цилиндры (рис. 2.8). Сравнительно быстро и просто определяют наличие в любом из них следующих характерных дефектов: износ цилиндров, износ поршневых колец, негерметичность и прогорание клапанов, задиры по длине цилиндра, поломка пружин и зависание клапанов, поломка и «залегание» поршневых колец, прогорание внутренней части прокладки головки блока.
Рис. 2.8. Принципиальная схема прибора для проверки герметичности надпоршневого пространства цилиндров двигателя: 1 — быстросъемная муфта; 2 — входной штуцер; 3 — редуктор; 4 — калиброванное сопло; 5 — манометр; 6 — демпфер стрелки манометра; 7 — регулировочный винт; 8 — выходной штуцер; 9 — соединительная муфта; 10 — присоединительный штуцер
Техническое обслуживание. Для предотвращения отказов и неисправностей двигателя на автотранспортных предприятиях выполняется комплекс профилактических мероприятий, включающих диагностику; ЕО двигателя; ТО-1, ТО-2, СО, Для легковых автомобилей, принадлежащих гражданам, с этой же целью выполняется перечень операций, регламентированных талонами сервисной книжки.
Регулировка зазоров привода клапанов в механизме газораспределения (без гидротолкателей) выполняется на холодном двигателе при полностью закрытых клапанах. Перед началом регулировки поршень первого цилиндра подводится в положение верхней мертвой точки (ВМТ) при такте сжатия, что можно контролировать по закрытию обоих клапанов первого цилиндра. Зазор, как правило, измеряют плоским щупом (возможно использование приспособления с индикаторной головкой часового типа).
Появление в конструкции ГРМ гидротолкателей позволяет автоматически выбирать зазор в приводе клапана. Однако гидротолкатели очень чувствительны к качеству масла и степени его очистки. Коксование масла, частицы износившихся и разрушившихся деталей способствуют заклиниванию гидротолкателей. В таком случае возникают ударные нагрузки, на которые механизм не рассчитан. Они быстро приводят к поломкам, или к таким износам деталей (толкатели, кулачки распределительного вала), при которых их дальнейшая эксплуатация невозможна.
Ремонт головки блока. При перегреве двигателя, перетяжке головки, а также при длительной эксплуатации нижняя плоскость головки блока деформируется.
В большинстве случаев имеет место деформация местного характера, при которой наружные края плоскости головки «возвышаются» над серединой (обычно не более 0,1 мм) Допустимым искривлением головки считается величина 0,05-0,06 мм.
Седла клапанов в процессе эксплуатации приобретают форму, отличную от конической: появляется овальность седла по фаске из-за неравномерного износа седла. Кроме того, при перегреве и деформации головки часто возникает несоосность направляющих втулок и седел клапанов. Встречаются случаи, когда на фаске седла (обычно выпускного клапана) появляются раковины из-за нарушения процесса сгорания и перегрева.
Основными способами ремонта седел клапанов являются фрезерование (
В качестве абразива предпочтительно использовать корундовую пасту зернистостью 28-40 мкм или аналогичный порошок с трансмиссионным маслом. Алмазные пасты применять нежелательно, так как из-за внедрения твердых частиц в металл ускоряется износ рабочих фасок седла и клапана в эксплуатации после ремонта.
Для контроля качества прилегания клапана к седлу после притирки существует несколько методов: по индикатору специального вакуумного измерительного приспособления, по краске, по «карандашу», а также по утечке керосина, налитого в камеру сгорания при собранных клапанах и пружинах. Наиболее простой является проверка с помощью мягкого карандаша, при которой на фаску клапана равномерно наносится 6-8 радиальных линий. После установки клапана необходимо нажать на тарелку и повернуть клапан на 180° в обе стороны. Если все сделано правильно, линии будут стерты.
2.5.3. ТО и ТР системы смазки и охлаждения двигателя
Система смазки. Внешними признаками неисправности системы являются потеря герметичности, загрязнение масла и несоответствие давления в системе нормативным значениям. Для многих грузовых автомобилей при скорости 40-50 км/ч на прямой передаче давление в системе должно быть примерно 0,2-0,5 МПа. Например, в прогретом двигателе КамАЗ-740 при 2600 об./мин. коленчатого вала рабочее давление масла должно быть 0,45-0,5 МПа. При падении давления до 0,09-0,04 МПа на щитке приборов ряда автомобилей загорается сигнальная лампа.
Удаление осадков, т.е. промывка системы смазки, является необходимой технологической операцией, особенно при сезонном переводе работы двигателя на масло другой марки. Промывочные масла — это маловязкие жидкости с особыми присадками. У каждой марки масла своя технология применения, но эффект примерно одинаков.
Некоторые марки промывочных масел после отстаивания можно еще использовать 1-2 раза. При отсутствии промывочных масел можно использовать обычные маловязкие масла, время промывки — примерно 10 мин., или, как исключение, летнее дизельное топливо, время промывки — не более 5 мин.
Надежность работы системы во многом зависит от состояния фильтров. Многие двигатели грузовых автомобилей имеют два фильтра: полнопоточный (грубой очистки) и центробежный (тонкой очистки). При ТО-2 у полнопоточных фильтров заменяют фильтрующие элементы, а центробежные разбирают, осматривают и промывают.
В обычных условиях эксплуатации, когда центрифуга работает исправно, в колпаке ротора после 10-12 тыс. км пробега скапливается 150-200 г отложений, в тяжелых условиях — до 600 г (толщина слоя отложений в 4 мм соответствует примерно 100 г). Следует иметь в виду, что в некоторых фильтрах ротор имеет частоту вращения до 5000 об./мин. При неправильной сборке будет сильная вибрация со всеми возможными последствиями. У правильно собранного и чистого фильтра после остановки двигателя ротор продолжает вращаться 2-3 мин., издавая характерное гудение.
Периодичность замены масла назначают в зависимости от марки масла и модели автомобиля. Уровень масла проверяют через 2-3 мин. после остановки двигателя. Он должен быть между метками маслоизмерительного щупа.
Система охлаждения. Внешними признаками неисправности системы охлаждения являются перегрев или недостаточный прогрев двигателя, потеря герметичности. Перегрев возможен даже при небольшом снижении уровня охлаждающей жидкости в системе. Особенно это проявляется при применении антифризов, которые могут вспениваться из-за наличия в системе воздуха и замедлять отвод тепла. Для предотвращения замерзания антифриза необходимо поддерживать его нормативную плотность. Так, при 20 °С плотность антифриза А-40 должна быть 1,067-1,072 г/см3, а антифриза Тосол А-40 — 1,075-1,085 г/см3.
Если охлаждающей жидкостью является вода, в системе образуется накипь, ухудшающая теплообмен. Удаляют накипь специальными составами. При их отсутствии в условиях АТП для двигателей с чугунной головкой блока можно использовать раствор каустика (700-1000 г каустика и 150 г керосина на 10 л воды), для двигателей с головкой и блоком из алюминиевого сплава — раствор хромпика или хромового ангидрида (200г на 10л воды). Раствор заливают и выдерживают в системе охлаждения 7-10 ч. Затем запускают двигатель на 15-20 мин. (на малой частоте вращения) и раствор сливают. Для удаления шлама систему промывают водой в направлении, обратном циркуляции охлаждающей жидкости.
Герметичность радиаторов восстанавливают пайкой мест повреждения. Сильно поврежденные трубки заменяют на новые или удаляют (заглушают), места установки пропаивают.
Пайка радиаторов из латунных сплавов сложностей не вызывает. Труднее ремонтировать радиаторы из сплавов алюминия. Для этого используют газовые горелки, специальный присадочный материал и припой. По некоторым технологиям место для пайки надо нагреть до 400-560 °С. Если деталь прогрета недостаточно, то припой будет распределяться по поверхности не равномерно, как требуется, а отдельными наплывами.
Перед установкой на автомобиль герметичность радиатора испытывают сжатым воздухом под давлением 0,1 МПа в течение 3-5 мин. При испытании водой давление должно быть 0,1-0,15 МПа.
2.5.4. Диагностика технического состояния и техническое обслуживание системы зажигания двигателя
На автомобилях применяются батарейные контактные (классические), контактно — и бесконтактно-транзисторные, а также цифровые системы, по существу являющиеся вариантом автоматического управления транзисторного зажигания для отдельных цилиндров. По статистике, на батарейное зажигание приходится примерно 12% всех отказов и неисправностей, которые в 80% случаев являются также причиной повышения расхода топлива (на 5-6%) и снижения мощности двигателя; для бесконтактно-транзисторных систем показатели надежности значительно лучше.
Характерными неисправностями системы зажигания являются: разрушение изоляции проводов высокого напряжения и свечей зажигания, нарушение контакта в местах соединений; ослабление пружины подвижного контакта; повышенный люфт валика распределителя; нагар на электродах свечей зажигания; изменение зазора между электродами свечей; межвитковые замыкания (особенно в первичной обмотке) катушки зажигания; неправильная начальная установка угла опережения зажигания; неисправность центробежного и вакуумного регуляторов.
Для диагностирования системы зажигания используют стационарные неавтоматизированные и компьютеризированные мотор-тестеры с электронно-лучевой трубкой, а также переносные электронные автотестеры (в последнее время с цифровой индикацией на жидкокристаллическом дисплее), достоинством которых является низкая стоимость, приспособленность для условий небольших АТП и СТО в сочетании с широкими функциональными возможностями. В ряде моделей отечественных автомобилей, оборудованных системой встроенных датчиков для диагностирования системы зажигания, предусмотрен специализированный разъем для подключения мотор-тестеров.
Тестеры последнего поколения, ввиду перехода изготовителей на производство бесконтактно-транзисторных систем зажигания, рабочие процессы которых существенно улучшают экологические показатели, предусматривают визуальный и цифровой анализ изменения напряжения только во вторичной цепи.
В последнее время все большее применение находят упрощенные цифровые приборы для проверки зазора в контактах прерывателя в комбинации с тахометром и вольтметром с двумя диапазонами измеряемого напряжения: до 20 В и до 0,5-1,0 В (последний используется для измерения напряжения на замкнутых контактах). Более сложные приборы, выполненные на основе микропроцессоров последних разработок, позволяют измерять величину напряжения пробоя Uп и длительность искрового заряда И. Практически уже имеющее место повсеместное применение транзисторных бесконтактных или цифровых систем зажигания позволяет осуществлять полный контроль любых систем зажигания только измерениями параметров напряжения пробоя Uп длительности искрового разряда И и среднего «интегрированного» напряжения горения искрового разряда, которые в принципе могут выполняться цифровыми приборами «карманного» исполнения. Визуальный контроль осциллограмм при этом становится не нужным, так же как и мотор-тестер, однако только всесторонний учет особенностей изменения напряжения во вторичной цепи, отражаемого осциллограммами, позволит получить эффективно работающие цифровые приборы. Последнее особенно важно в связи с дальнейшим совершенствованием зажигания в направлении увеличения длительности искрового разряда (так называемое плазменное зажигание) и применения новых конструкций свечей (с тремя-четырьмя боковыми электродами или исполнения их в виде единого «кольца»).
Проверку и регулировку угла опережения зажигания проводят следующим образом. При неработающем двигателе производят начальную установку угла по совмещению подвижной и неподвижной меток ВМТ, расположенных на маховике или шкиве привода вентилятора двигателя, однако указанный метод дает погрешность до 5°. Проверку и окончательную регулировку данного угла, а также работу центробежного и вакуумного регуляторов осуществляют на режимах разгона автомобиля или «разгона» двигателя на холостом ходу.
В режимах разгона автомобиля на дороге или даже при испытаниях на ненагруженных беговых барабанах динамометрического стенда (простейшие барабаны могут быть изготовлены силами предприятия) неэффективная работа центробежного и вакуумного регуляторов ухудшают динамику автомобиля, которую несложно контролировать по увеличению времени разгона на прямой передаче от скорости 35-40 км/ч до скорости 60-80 км/ч, особенно на стенде.
Правильнее проверку угла опережения зажигания проводить на работающем двигателе при помощи стробоскопического устройства. Принцип его работы заключается в том, что если в строго определенные моменты времени относительно угла поворота вращающейся детали освещать ее коротким импульсом света (примерно 0,0002 с), то деталь будет казаться неподвижной. Таким образом проверяют соответствие измеряемых углов опережения их нормативным значениям на малой, средней и большой частотах вращения коленчатого вала двигателя (с учетом работы вакуумного регулятора). По результатам проверки производят регулировку или замену прерывателя. Снятый прерыватель можно восстанавливать в условиях специализированного участка с использованием для проверки качества восстановления стационарных стендов. В условиях участка эффективны также пескоструйная очистка свечей и проверка их работоспособности при определенном давлении (на специальных приборах).
2.5.5. Диагностика технического состояния и техническое обслуживание системы питания двигателя
На систему питания карбюраторных двигателей приходится около 5% отказов от общего их числа по автомобилю. Однако состояние основного элемента системы — карбюратора — является определяющим для обеспечения топливной экономичности (средний перерасход топлива из-за не выявленных по внешним признакам неисправностей составляет 10-15%) и допустимой концентрации вредных компонентов в отработавших газах.
К явным неисправностям системы питания относят нарушение герметичности и течь топлива из топливных баков и трубопроводов, «провалы» двигателя при резком открытии дроссельной заслонки из-за ухудшения функционирования ускорительного насоса; к неявным — загрязнение (повышение гидравлического сопротивления) воздушных фильтров, прорыв диафрагмы и негерметичность клапанов бензонасоса, нарушение герметичности игольчатого клапана и изменение уровня топлива в поплавковой камере, изменение (увеличение) пропускной способности жиклеров, неправильная регулировка холостого хода.
Выявление неявных неисправностей карбюратора и бензонасоса производится ходовыми и стендовыми испытаниями, а также путем оценки состояния отдельных элементов после снятия карбюратора и его профилактической переборки и испытаний в цеховых условиях.
Одним из конечных показателей технического состояния системы питания (при прочих равных условиях) является расход топлива
Признаком экономичности является устойчивая работа карбюратора на постоянных и переменных нагрузочных режимах только при полном прогреве двигателя и карбюратора. В условиях цеха у карбюратора, помимо герметичности игольчатого клапана и уровня топлива в поплавковой камере, проверяют также пропускную способность жиклеров и герметичность клапана экономайзера. У бензонасосов проверяют создаваемое разрежение (не ниже 50 кПа), давление (17-30 кПа) и подачу (0,7-2,0 л/мин), а также целостность диафрагмы. (Указанные виды испытаний можно осуществлять как на отдельных приспособлениях и приборах, так и на специальных комбинированных стендах, которые достаточно широко распространены на АТП.)
Наиболее ответственной является проверка пропускной способности жиклеров, которая измеряется по количеству воды (в кубических сантиметрах), протекающей через дозирующее отверстие жиклера за 1 мин. под напором водяного столба 1 м ± 2 мм при температуре 20±1 °С. На основе указанных измерений можно не только проверять соответствие жиклеров паспортным данным, но и осуществлять индивидуальную «подгонку» пропускной способности топливных или воздушных жиклеров главной дозирующей системы для каждого карбюратора, что обеспечивает экономичные режимы работы (на основе данных участка диагностирования или испытаний карбюратора на дороге).
На систему питания дизелей приходится до 9% всех неисправностей автомобилей. Характерными неисправностями являются: нарушение герметичности и течь топлива, особенно топливопроводов высокого давления; загрязнение воздушных и особенно топливных фильтров; попадание масла в турбонагнетатель; износ и разрегулировка плунжерных пар насоса высокого давления; потеря герметичности форсунками и снижение давления начала подъема иглы; износ выходных отверстий форсунок, их закоксовывание и засорение. Эти неисправности приводят к изменению момента начала подачи топлива, неравномерности работы топливного насоса по углу поворота коленчатого вала и количеству подаваемого топлива, ухудшению качества распиливания топлива, что прежде всего вызывает повышение дымности отработавших газов и приводит к незначительному повышению расхода топлива и снижению мощности двигателя на 3-5%.
Контроль системы питания включает в себя: проверку герметичности системы и состояния топливных и воздушных фильтров, проверку топливоподкачивающего насоса, насоса высокого давления и форсунок.
Состояние сухих воздушных фильтров, устанавливаемых на всех последних моделях автомобилей, проверяют по разрежению за фильтром при помощи водяного пьезометра (должно быть не более 700 мм вод. ст.). Состояние топливных фильтров можно проверить в первом приближении на холостом ходу двигателя по давлению за фильтром (допускается не менее 150 кПа), а более точно — по перепаду давлений перед фильтром и за ним (не более 20 кПа). Более низкое давление свидетельствует также о неисправной работе топливоподкачивающего насоса, который после переборки в условиях цеха при испытаниях на специальном стенде должен обеспечивать (при 1050 об/мин) разрежение не менее 50 кПа, давление не менее 400 кПа и подачу не ниже 25 см3 на 100 рабочих ходов (приведенные нормативы — для восьмицилиндровых двигателей МАЗ и КамАЗ).
Контроль насоса высокого давления и форсунок непосредственно на автомобиле проводят при превышении двигателем норм по дымности и с целью выявления и устранения неисправностей. Наибольшее распространение получил метод, основанный на анализе изменения давления, фиксируемого при помощи специального накладного (зажимного) датчика, устанавливаемого у форсунки на нагнетательный топливопровод (рис. 3.19). Здесь в точке 1 начинается повышение давления в результате движения плунжера насоса, в точке 2 срабатывает нагнетательный клапан, и при малой скорости движения плунжера рост давления на некоторое время замедляется.
Рис. 3.19. Общий вид осциллограммы, отображающей давление в топливопроводе дизельного двигателя
В точке 3 поднимается игла форсунки. При этом давление падает, поскольку высвободившийся объем не успевает заполниться топливом, а затем снова повышается до определенной величины. Точка 4 на большой частоте вращения коленчатого вала двигателя может характеризовать максимальное давление процесса впрыска. Однако для нормального процесса в режиме холостого хода это давление обычно фиксируется по характерному пику точки 3. В точке 5 происходит «посадка» иглы форсунки и впрыскивание заканчивается, после чего происходит «посадка» в седло нагнетательного клапана плунжера. Импульсы остаточного давления (6) появляются в результате недостаточной герметичности нагнетательного клапана. Величина сигнала S1 определяет затяжку пружины форсунки и статическое давление начала впрыска. Перепад давления Р характеризует подвижность иглы форсунки. Путем интегрирования на периоде впрыска tвпр можно оценить цикловую подачу топлива. Время задержки впрыска S2 характеризует зазор в плунжерной паре, вызывающий утечку топлива между гильзой и плунжером.
Наиболее сложными и ответственными являются осуществляемые на специальных стендах цеховые проверка и регулировка насоса высокого давления на начало подачи, ее равномерность и на собственно подачу топлива. Отклонение начала подачи топлива каждой секцией относительно первой не должно превышать ±20, а неравномерность при установке рейки в положение максимальной подачи — 5%. На стенде регулируются пусковая и максимальная цикловые подачи топлива, а также работа регулятора топлива (выключение подачи топлива при остановке двигателя, автоматическое выключение подачи топлива при установленных максимальной частоте вращения коленчатого вала двигателя и частоте начала работы автоматического регулятора).
Монтаж насоса высокого давления на двигателе производят при помощи моментоскопа (стеклянной трубки с внутренним диаметром 1,5-2,0 мм), устанавливаемого на выходном штуцере первой или предыдущей по порядку работы секции насоса, по появлению топлива в котором производится закрепление муфты привода таким образом, чтобы угол опережения составлял 16-19° до ВМТ первого цилиндра. Выполнение указанных работ обеспечивает (при правильной регулировке клапанов и хорошей компрессии в цилиндрах двигателя) минимальную дымность и максимальную экономичность работы дизеля.
Контрольные вопросы темы:
1.Как производится общая диагностика двигателя?
2. Какие параметры технического состояния можно диагностировать у ДВС переносными диагностическими комплектами?
3. Объясните причины неравномерности работы цилиндров двигателя?
4. Объясните понятие «Балансовая мощность двигателя?
5. Как влияют состояния ЦПГ и клапанов на показатели работы двигателя?
6. Как по дымности выхлопных газов определить состояние ЦПГ?
7. Как произвести ослушивание двигателя с помощью стетоскопа?
8. Какие параметры диагностируют пневматическим калибратором?
9. Как устраняются неисправности газораспределительного механизма?
10. Существует ли определенная последовательность затяжки болтов головки цилиндров?
11. В чем заключаются особенности регулировки клапанов у разных ДВС?
12. Какие параметры диагностируются по фазам газораспределения?
13. Как производится текущий ремонт ЦПГ?
14. Как определить неисправности КШМ?
15. Как производится текущий ремонт КШМ?
16. Составьте порядок промывки систем смазок бензинового и дизельного двигателей.
17. Перечислите основные неисправности системы смазки.
18. Перечислите основные неисправности системы охлаждения.
19. Какие неисправности системы питания карбюраторного двигателя бывают?
20. Какие составы используются для очистки системы охлаждения?
21. Как производится регулировка карбюратора?
22. Перечислите основные неисправности систем питания инжекторных двигателей.
23. Перечислите основные неисправности системы питания дизельных двигателей.
24. В какой последовательности проводятся регулировки форсунок дизельных двигателей?
25. Приведите порядок установки угла опережения подачи топлива ТНВД.
studfile.net
Техническое обслуживание двигателя. Энциклопедия начинающего водителя
Техническое обслуживание двигателя
Мойка двигателя. Моют двигатель по двум причинам – во-первых, из-за того, что постоянно высокая температура двигателя способствует образованию прочной и плотной пленки из масла, пыли и грязи, которая нарушает теплообмен между двигателем и окружающим воздухом; во-вторых, если нужно определить места неплотностей, через которое подтекает масло.
Для мойки двигателя лучше использовать аэрозоль-очиститель для холодной очистки. Мыть бензином или керосином слишком опасно. Автоочиститель наносят кистью, слегка смачивая ее в воде и растирая очиститель по поверхности. Через некоторое время, закрыв полиэтиленовой пленкой распределитель зажигания и генератор, ополоснуть двигатель водой. Если нет автоочистителя, применяют стиральный порошок (стакан порошка на полведра воды). Моют двигатель обычно сильной струей из шланга, надев, предварительно, как и в первом случае на карбюратор, катушку зажигания и распределитель мешочки из полиэтиленовой пленки и закрыв свечи. Двигатель после мойки, как правило, долго не запускается.
Одним из основных условий, необходимых для правильной работы двигателя и обеспечения его полной мощности, является абсолютная герметичность камеры сгорания цилиндра. Если камера сгорания одного или нескольких цилиндров негерметична, понижается степень сжатия смеси в цилиндрах, а следовательно, и мощность двигателя, что способствует непроизводительному расходу топлива. Поэтому компрессию следует проверять не только в случае увеличения расхода топлива и падения мощности двигателя, но и при замене масла. Из меряют компрессию на двигателе, прогретом до нормальной рабочей температуры. Для этого выворачивают свечу и вместо нее вворачивают наконечник компрессометра. Затем полностью открывают заслонку карбюратора и на несколько секунд включают стартер до максимального отклонения стрелки компрессометра. Таким образом последовательно измеряют давление до конца такта сжатия во всех цилиндрах двигателя. У разных двигателей величина компрессии различна и зависит от степени сжатия. Водитель должен знать величину компрессии, которую указывают в документации автомобиля, чтобы сопоставить с ней результаты измерения. Если данных о величине компрессии нет, можно, зная степень сжатия нового карбюраторного двигателя, умножить ее на 0,125 и с достаточной точностью определить (в МПа) величину компрессии для данного двигателя, если он находится в хорошем техническом состоянии. Допустимой обычно считается разница давления конца такта сжатия в отдельных цилиндрах, составляющая 0,1 МПа. Разница между самым низким показателем компрессометра и эталонными данными для двигателя, находящегося в хорошем техническом состоянии, не должна превышать 0,15 МПа. Низкая компрессия в цилиндрах свидетельствует о их негерметичности, основными причинами возникновения которой могут быть износ внутренней поверхности цилиндров и поршневых колец, негерметичность клапанов, залегание или трещина поршневых колец, повреждение прокладки головки блока.
Измерение компрессии производят только при полностью заряженной аккумуляторной батарее. Если она разряжена, стартер и коленчатый вал вращаются медленно, это приводит к неправильным, как правило, заниженным результатам измерений.
Техническое обслуживание цилиндропоршневой группы двигателя производят после пробега первых 2 тыс. км, а в дальнейшем только после снятия головки блока цилиндров или при появлении признаков прорыва газов либо подтекания охлаждающей жидкости в соединениях путем подтягивания гаек шпилек и болтов головки блока цилиндров. Через 10–15 тыс. км пробега следует проверить и при необходимости подтянуть болты и гайки крепления опор двигателя, а также очистить от грязи и масла их резиновые подушки.
Масло в двигателе. Нормальное количество масла в двигателе – чуть ниже верхней риски щупа. Начинающий водитель должен знать, что превышение уровня верхней риски для двигателя так же вредно, как и опускание уровня ниже допустимого, так как занижение уровня масла приводит к недостаточному разбрызгиванию масла коленчатым валом, а завышение – к выдавливанию масла через сальники и выгоранию его в цилиндрах (дымление из глушителя и маслоналивной горловины).
При расходе масла более 2,5 % от расхода топлива двигатель нуждается в ремонте. Если, конечно, нет течи или иных повреждений собственно системы смазки. Именно угар может служить основным критерием оценки работы двигателя. Уровень масла при ежедневных поездках неоходимо проверять: раз в неделю на исправном двигателе; ежедневно при подозрении на разрегулированность двигателя; после каждой поездки свыше 50 км на высокой скорости.
Расход масла менее 2,5 % от расхода топлива считается нормальным, поэтому постепенное снижение уровня масла в двигателе вас беспокоить не должно. Кроме того, длительное движение на высоких скоростях неизбежно приводит к перерасходу масла.
Особое беспокойство должно вызывать не понижение, а повышение уровня масла. Это означает, что где-то нарушилась герметичность соприкасающихся систем (прокладки системы охлаждения или мембраны бензонасоса). Определить неисправность можно, если понюхать щуп – запах бензина будет свидетельствовать о необходимости ремонтировать бензонасос. При отсутствии запаха 2–3 раза в день нужно доставать щуп и проверять цвет масла. Если оно начало светлеть, необходимо отправляться в ремонт. Одним из признаков нарушения герметичности системы охлаждения может служить пробулькивание газов при заведенном двигателе и снятой пробке радиатора.
Другим способом определения неисправности является внесение кончика щупа с маслом в пламя зажигалки. Чистое, качественное масло не горит; масло с примесью бензина сразу ярко вспыхивает; если при внесении щупа в пламя появляются треск и яркие искры, значит, в масло попадает вода или иные посторонние примеси.
Масло следует менять раз в год, независимо от пробега, так как, попав в мотор, масло начинает медленно, но неотвратимо ухудшать свои качества – окисляться, осмоляться, загрязняться. В конце концов оно утрачивает все свои полезные качества, даже если автомобиль за это время не прошел ни одного километра.
Не следует беспокоиться, если залитое в двигатель масло темнеет уже на третий день работы. Это свидетельствует только о его хороших моющих качествах. Тревогу должно вызывать, если вы, растерев масло между пальцами, ощутили присутствие каких-либо крупинок.
Система охлаждения. Каждый двигатель при работе нагревается, поэтому любая конструкция мотора предполагает наличие системы охлаждения. Система охлаждения предназначена для поддержания температуры элементов двигателя в определенных допустимых пределах и для выравнивания температур различных его частей, иначе может произойти перегрев или переохлаждение двигателя.
Перегрев двигателя приводит к самовоспламенению и детонации. При этом из-за уменьшения наполнения цилиндров снижается мощность двигателя и увеличивается расход топлива. Переохлаждение двигателя способствует конденсации части топлива, которое, осаждаясь на стенках цилиндров, разжижает масло, ухудшая его смазочные свойства, а это, в свою очередь, увеличивает износ стенок. При переохлаждении двигателя снижается качество процесса сгорания, уменьшается мощность и до 20 % возрастает расход топлива. Для того чтобы предотвратить это, современные двигатели оборудованы автоматическими термостатами, которые обеспечивают наиболее выгодный тепловой режим двигателя в различных эксплуатационных и климатических условиях.
Если двигатель в исправном состоянии нагревается слишком медленно, то это сигнал о повреждении термостата (не закрывается его клапан). Если клапан открывается при более низкой температуре, то увеличивается время нагревания двигателя до его рабочей температуры. В двигателях, охлаждаемых воздухом, подаваемым воздухонагревателем, термостат регулирует поступление холодного воздуха. Действие термостата можно проверить, погрузив его в емкость с водой. Подогревая емкость на электрической плитке, нужно по показаниям термометра, помещенного в эту же емкость, проследить, правильно ли действует клапан термостата в требуемом режиме температур. В случае неисправности термостат заменить.
Зимой двигатель охлаждается очень интенсивно, поэтому радиатор частично или полностью утепляют. В некоторых моделях автомобилей имеются радиаторы с жалюзи или заслонкой. Перегрев нагревателя приводит к ускорению износа его деталей, значительному увеличению расхода масла и топлива. Поэтому при проведении ежедневного технического обслуживания двигателя необходимо обязательно проверять уровень охлаждающей жидкости. Утечка жидкости свидетельствует о негерметичности системы охлаждения. Если жидкость вытекает в местах соединений, следует проверить и подтянуть хомуты. Если это не помогает, меняют трубопроводы. Все неплотности радиатора устраняют с помощью пайки. В случае утечки охлаждающей жидкости нужно немедленно устранить неисправность, так как при этом помимо убывания охлаждающей жидкости возникают нарушения в циркуляции жидкости, ее закипание, следовательно, перегревание двигателя. В двигателях, не имеющих замкнутой системы охлаждения, убывание жидкости может произойти в результате ее вытекания через сливную трубку радиатора или вследствие ее испарения.
В качестве охлаждающей жидкости, как правило, применяют тосол. Уровень тосола в расширительном бачке проверяют раз в неделю. Заливать охлаждающую жидкость в расширительный бачок под горлышко не нужно, потому что после прогревания двигателя тосол поднимется в бачке и выплеснет излишек. Вполне достаточно, если она поднимется немного выше нижней отметки бачка.
Если при проверке уровня охлаждающей жидкости, верхний бачок полный – все хорошо. Если нет – следует наполнить его, пустить двигатель и посмотреть в радиатор. Пробулькивание сквозь жидкость пузырьков газа будет свидетельствовать о пробитой прокладке блока, трещине в головке блока или гильзе цилиндра.
Тосол имеет строго определенную плотность в зависимости от того, на какую минимальную температуру он рассчитан. Проверку можно произвести с помощью специального ареометра на станции техобслуживания. Тосол не замерзает на холоде, срок его службы в среднем составляет 2–4 года.
Летом, в пути, в систему охлаждения можно добавлять и чистую воду, однако по возвращении необходимо как можно быстрее пополнить ее соответствующим количеством охлаждающей жидкости. Если воду используют зимой (в случае долгой стоянки автомобиля), ее следует сливать из радиатора, иначе при замерзании она расширится и разрушит радиатор и части двигателя.
Охлаждающую жидкость сливают через отверстия в бачке радиатора и в блоке цилиндров. Для полного слива необходимо открыть кран отопителя. Слитая охлаждающая жидкость ядовита, ее нельзя сливать в почву и водоемы. Перед заливкой новой жидкости следует промыть систему раствором для удаления накипи и ржавчины.
В процессе эксплуатации двигателя необходимо периодически проверять натяжение ремня привода вен тилятора и насоса охлаждающей жидкости или воздухонагревателя. Если ремень натянут слабо или загрязнен маслом, он проскальзывает, из-за чего вентилятор и водяной насос или воздухонагреватель вращаются медленно, что приводит к перегреву двигателя.
Поделитесь на страничкеСледующая глава >
info.wikireading.ru
Основные неисправности двигателя — Техническое Обслуживание и Ремонт Автомобилей
§ 5. Основные неисправности двигателя
Двигатель должен работать надежно, без перебоев, развивать достаточную мощность для обеспечения нормальных динамических (тяговых) свойств автомобиля, расходовать топливо и масло в пределах установленных норм.
Признаками, основных неисправностей двигателя являются:
-падение мощности,
-повышенный расход масла, дымный выпуск,
-снижение давления конца сжатия (компрессии),
-стуки в двигателе.
Мощность двигателя снижается, а расход топлива увеличивается при неисправности системы питания, накоплении нагара в камерах сгорания, отложениях во впускной системе, наличии накипи и грязи в системе охлаждения, неправильной регулировке газораспределительного механизма, недостаточной компрессии в цилиндрах двигателя, пропуске воздуха через уплотнения впускной системы.
Повышенный расход масла (угар) и дымный выпуск наблюдаются при износе и поломке поршневых колец, потере ими упругости, износе канавок для поршневых колец, износе и повреждении гильз цилиндров, подсосе масла через зазоры между стержнями клапанов и направляющими втулками, нарушении уплотнений коленчатого вала и неисправности системы вентиляции картера двигателя. На дымность выпуска большое влияние оказывают неисправности топливной аппаратуры.
Давление конца сжатия (компрессия) может понизиться при износе поршневых колец и гильз цилиндров, неплотном прилегании клапанов к седлам, износе направляющих втулок клапанов, ослаблении затяжки гаек крепления головок цилиндров, повреждении прокладки головки цилиндров, нарушении зазоров в газораспределительном механизме.
Стуки в двигателях появляются при поломке клапанных пружин и заедании клапанов; задирах на поверхностях гильз и поршней; увеличенных зазорах между стержнями клапанов и носками коромысел; износе поршневых пальцев, отверстий для них в бобышках поршней и во втулках верхних головок шатунов; износе шатунных и коренных подшипников.
Техническое состояние двигателя проверяют наружным осмотром, по показаниям контрольно-измерительных приборов, расходу топлива и масла, путем прослушивания двигателя.
Для поддержания двигателя в работоспособном состоянии и в надлежащем внешнем виде, уменьшения интенсивности изнашивания деталей, предупреждения отказов и неисправностей, а также выявления их с целью своевременного устранения выполняют техническое обслуживание двигателя.
toira.ru
Виды технического обслуживания двигателей
Категория:
Двигатели ЯАЗ-М204 и ЯАЗ-М206
Публикация:
Виды технического обслуживания двигателей
Читать далее:
Виды технического обслуживания двигателей
При эксплуатации двигателей рекомендуется проводить следующие виды технического обслуживания: ежедневный уход, первое техническое обслуживание, второе техническое обслуживание, третье техническое обслуживание.
Интервалы между различными техническими обслуживаниями следует устанавливать в часах работы двигателя и записывать в ведомости эксплуатации или регистрировать счетчиком.
Ежедневный уход необходим как до пуска двигателя, так и после его остановки по окончании суточной работы. Кроме этого, при остановках во время суточной работы двигатель следует дополнительно осматривать.
Рекламные предложения на основе ваших интересов:
Сроки между обслуживаниями устанавливают в зависимости от условий работы двигателей.
Первое техническое обслуживание для двигателей ЯАЗ-М204, работающих с расходом топлива 15—20 кг/час, и для двигателей ЯАЗ-М206, работающих, с расходом топлива до 30 кг/час, необходимо выполнять через 50—60 час. работы.
При меньшем расходе топлива первое техническое обслуживание нужно выполнять через 60—80 час. работы.
При работе с меньшими нагрузками и благоприятных условиях эксплуатации обслуживание можно производить через 80—110 час. работы.
При работе в условиях большой запыленности воздуха обслуживание надо производить чаще, чем указано. Особенно важно в этих условиях практически установить время обслуживания воздушных фильтров.
Во время работы двигателей при очень низкой температуре воздуха, а также при резких и частых изменениях нагрузки и при Длительной работе на холостом ходу сроки между обслуживаниями нужно уменьшить.
В особо неблагоприятных условиях работы периодичность обслуживания двигателя устанавливают практически в зависимости °т результатов работы двигателей.
Второе техническое обслуживание необходимо проводить через 200—500 час. работы двигателя, т. е. через каждые четыре первых технических обслуживания.
Третье техническое обслуживание следует проводить через каждое второе техническое обслуживание.
Техническое обслуживание двигателя необходимо выполнять так, чтобы Ьнутрь двигателя и его узлов не попадала грязь и пыль. Для этого надо протереть и промыть двигатель и защитить его от попадания пыли.
В особенности важно избежать попадания грязи и пыли в нагнетатель, насос-форсунки, баки, топливные фильтры и другие узлы системы питания. При попадании грязи и пыли в эти узлы могут появиться задиры роторов нагнетателей и плунжерных пар насос-форсунок.
При снятии насос-форсунок необходимо отверстия в штуцерах и ниппелях немедленно закрывать колпачковыми гайками.
Перед разборкой топливных и масляных фильтров для замены или проверки элементов следует тщательно протереть корпусы и крышки фильтров.
Перед снятием воздушные фильтры, а также сопряженную часть впускного трубопровода надо тщательно протереть. После снятия воздушных фильтров нужно закрыть отверстия во фланцах этого трубопровода жестяными или картонными заглушками.
При снятии топливных трубок надо немедленно обмотать их концы изоляционной лентой и закрыть угольники или штуцеры пробками.
Ниже дан рекомендуемый объем различных технических обслуживании двигателей; этот объем может изменяться в зависимости от условий эксплуатации.
Ежедневный уход
До пуска двигателя
1. Проверить уровень охлаждающей жидкости в радиаторе и при необходимости долить жидкость.
В случае применения в зимнее время воды нужно заливать в двигатель горячую воду с температурой 70—80°. При применении жидкости, замерзающей при низкой температуре, в зимнее время надо подогревать двигатель, пользуясь безламповым пусковым подогревателем.
2. Проверить количество топлива в баке.
3. Проверить количество масла в поддоне. Уровень масла должен быть несколько выше верхней метки на маслоизмерительном стержне.
После пуска двигателя
1. Прогреть двигатель до температуры охлаждающей жидкости, равной 50°, сначала в течение 1 мин. при 400—500 об/мин коленчатого вала, а затем при 1000 об/мин коленчатого вала с последующим постепенным увеличением числа оборотов до 1500 в минуту.
2. Проверить показания контрольных приборов. Манометр снуемы смазки должен показывать давление не менее 0,4 кг/см2 при 500 об/мин коленчатого вала.
Термометр должен показывать температуру не менее 50° перед нагрузкой двигателя.
Тахометр должен показывать 400—500 об/мин при положении педали подачи топлива, соответствующем минимальной подаче.
Амперметр должен показывать зарядный ток при числе оборотов коленчатого вала более 1300 в минуту.
3. Проверить состояние всех топливных и масляных трубок и их соединений. Если есть подтекание, подтянуть соединения.
После окончания суточной работы
1. Протереть двигатель от пыли и грязи.
2. Проверить работу двигателя под нагрузкой при 1500 об/мин коленчатого вала, обращая внимание на цвет дыма выпускных газов, и провести необходимое обслуживание, если дым густой.
3. Прослушать работу двигателя и убедиться в отсутствии резких металлических стуков. Если слышны стуки, принять меры к их устранению.
4. Проверить показания манометра системы смазки (при температуре охлаждающей жидкости 80° давление масла должно быть не менее 1,7 кг/см2 при 2000 об/мин коленчатого вала двигателя).
5. Проверить, нет ли течи во всех соединениях систем: охлаждения, смазки и питания двигателя. При обнаружении течи устранить ее.
6. Спустить топливо из фильтра грубой очистки (0,1 л) и из фильтра тонкой очистки (0,2 л). После этого двигатель должен проработать 2—3 мин. при 1000 об/мин коленчатого вала.
7. Заполнить топливный бак топливом, не ожидая его охлаждения во избежание конденсации воды в топливе.
8. Через 5 мин. после остановки двигателя (при заполненной системе) проверить уровень масла в картере. Если уровень повысился и масло стало жидким, найти причины разжижения масла и устранить их. Если уровень масла ниже метки В на маслоизмери-тельном стержне, долить масло до метки.
9. При работе в условиях запыленности воздуха промыть воз-Душные фильтры. Если на двигателе установлены центробежно-контактные воздушные фильтры, их необходимо снять и удалить пыль из бункера встряхиванием.
10. Проверить натяжение ремней привода вентилятора; если требуется, подтянуть ремни
11. При безгаражном содержании двигателей в зимнее время слить воду из системы охлаждения, открыв краники, расположенные на нижнем патрубке, соединяющем двигатель с радиатором, на корпусе водяного насоса, на подводящем патрубке безлампово-то пускового подогревателя и на блоке цилиндров. Пробка радиатора при сливе воды должна быть снята.
Несоблюдение этих условий может вызвать разрыв блока цилиндров остатками замерзшей воды.
В случае применения жидкости, замерзающей при низкой температуре, сливать ее необязательно.
Рис. 1. Порядок затяжки гаек головки цилиндров двигателей ЯАЗ-М204
Первое техническое обслуживание
Первое техническое обслуживание, кроме работ по ежедневному обслуживанию, включает в себя следующие операции.
1. При установке двигателя на автомобиле проверить величину свободного хода педали сцепления. Если величина свободного хода педали достигнет 10 мм, обязательно отрегулировать сцепление и механизмы его включения (нормальная величина свободного хода 32—40 мм).
2. Сменить масло в двигателе. После пуска двигателя и последующей остановки на 3—5 мин. долить масло до метки В на маслоизмерительном стержне. Перед заливкой масла необходимо промыть поддон, элементы масляного фильтра грубой очистки и заменить элемент масляного фильтра тонкой очистки. При замене последнего следует сменить прокладки между корпусом и крышкой фильтра.
3. На прогретом двигателе только после первых 50 часов его работы проверить затяжку гаек головки цилиндров в порядке, показанном на рис. 1 и 2. Проверять затяжку нужно без рывков, усилием одной руки на плече 0,8 м, используя специальный торцовый ключ, прикладываемый к двигателю. При использовании динамометрического ключа момент затяжки должен быть 26—28 кгм.
Перед затяжкой гаек крепления головки цилиндров необходимо ослабить горизонтальные болты подъемных колец и болты крепления регулятора числа оборотов к головке блока.
4. Снять воздушные фильтры и промыть их фильтрующие элементы, руководствуясь указаниями раздела «Обслуживание системы подачи воздуха». В инерционно-масляных фильтрах одновременно сменить масло. При снятии фильтров следует закрывать отверстия во фланцах впускного топливопровода жестяными или картонными крышками.
5. Проверить установку насос-форсунок АР-20 калибром высотой 37,7 мм, АР-23А — калибром высотой 37,4 мм, АР-21 — калибром высотой 37,1 мм*. Калибр должен касаться контрольной площадки торца тарелки толкателя плунжера наcос-форсунки. В случае необходимости отрегулировать в соответствии с указаниями раздела «Регулировка двигателя».
6. Проверить зазоры между торцами клапанов и коромыслами при температуре охлаждающей жидкости около 70°. Щуп толщиной 0,25 мм должен проходить свободно, а щуп толщиной 0,3 мм — с усилием.
7. Проверить и при необходимости подтянуть все шланговые соединения и хомутики. Осмотреть крепления радиатора. Если радиатор загрязнен, промыть его снаружи. Проверить (нажимая пальцем) действие клапанов пробки радиатора; а также наличие и исправность ее прокладок.
8. Осмотреть электрическую проводку. Проводку с поврежденной изоляцией заменить или обмотать изоляционной лентой. Удалить накопившиеся в местах соединения проводов грязь и масло; при необходимости подтянуть крепежные детали.
9. Проверить крепление стартера к картеру маховика и плотность затяжки контактов всех проводов, соединяющих стартер с аккумуляторными батареями, в том числе и соединений с массой; при необходимости очистить контакты. Если полюсные наконечники снимались для зачистки, то после установки на место их необходимо слегка смазать вазелином.
10. Проверить кислотным ареометром состояние электролита в батареях. Если электролита недостаточно, долить дистиллированной воды. Уровень электролита должен быть выше пластин на Ю—15 мм. Минимальная плотность электролита для центральных и большинства северных районов СССР с температурой до —35°С зимой равна 1,245, что соответствует разряженности батареи на 25%) если в заряженном состоянии плотность электролита была 1,285. Минимальная плотность электролита летом для крайних северных и центральных районов СССР равна 1,19, что соответствует разряженности батареи на 50%, если в заряженном состоянии плотность электролита была равна 1,27. Аккумуляторную батарею, разряженную зимой более чем на 25% и летом более чем на 50%, необходимо снять с автомобиля или агрегата и отправить для зарядки на аккумуляторную станцию.
11. Слить из топливного бака не менее 3 л топлива (после отстаивания в течение не менее 5 час.)»
12. Тщательно проверить и устранить подтекание охлаждающей жидкости, топлива и масла. Для этого нужно тщательно протереть двигатель и дать ему проработать в течение 5—10 мин. при числе оборотов коленчатого вала 2000 в минуту. При этом хорошо будут видны все подтекания.
13. Проверить действие дренажных трубок воздушной камеры (при работе двигателя из отверстий трубок должна выходить струя воздуха). Подставив лист бумаги под струю воздуха, проверить, не уносится ли масло из воздушной камеры. При правильной работе дренажных трубок на поверхности листа бумаги через 1—2 мин. работы двигателя должны быть только отдельные масляные пятна.
14. Проверить на ощупь или с помощью термометра температуру стенок всех патрубков выпускного “ трубопровода работающего двигателя. Температура стенок отдельных патрубков при холостом ходе двигателя не должна значительно отличаться. При большой разнице в температуре или при неравномерной работе двигателя (заметной на слух) выяснить причину и в случ’ае необходимости отрегулировать двигатель.
15. Удалить с поверхности реле-регулятора грязь и масло. Проверить работу регулятора напряжений. При числе оборотов коленчатого вала менее 900 в минуту амперметр должен показывать разрядный ток, если включены потребители; при числе оборотов более 1300 в минуту — зарядный ток; когда двигатель не работает, стрелка амперметра должна стоять на нуле. Стрелка амперметра при полностью заряженных аккумуляторных батареях также может стоять около нуля или показывать минимальный зарядный ток. В этом случае отсутствие зарядного- тока не является признаком неисправной работы электрооборудования.
16. Проверить работу механизма управления насос-форсунками и механизма остановки двигателя.
17. Подтянуть все внешние болты и гайки. При подтяжке необходимо обратить особое внимание на затяжку гаек крепления оси вентилятора и выпускного трубопровода, болтов крепления опор двигателя, болтов крепления поддона. Проверить состояние зажимов аккумуляторных батарей и при необходимости затянуть их. Проверить прочность установки батарей в гнездах или на кронштейнах и, если потребуется, укрепить батареи.
18. Проверить работу приборов: манометра системы смазки, дистанционного термометра, тахометра, амперметра. Рекомендуется записать показания: манометра при 2000 об/мин коленчатого вала и температуре охлаждающей жидкости 70°; амперметра при 1400 об/мин коленчатого вала.
19. Наполнить консистентной смазкой полости шкива между подшипниками. Для этого нужно выдернуть пробку, имеющуюся на шкиве вентилятора, ввернуть масленку и нагнетать смазку шприцем до появления сопротивления. Не следует резко подавать смазку во избежание выдавливания ее через пробковый сальник привода вентилятора. На двигателе ЯАЗ-М204Г кроме того, необходимо набить консистентной смазкой полость шкива натяжного приспособления, сняв крышку шкива.
20. Залить в масленки стартера по 15 капель дизельного масла.
21. Смазать консистентной смазкой выжимной подшипник сцепления, сделав шприцем 3—4 хода.
22. Проверить уровень масла в картере коробки передач. При необходимости долить масло через воронку с сеткой до контрольного отверстия.
Рис. 2. Порядок затяжки гаек головки цилиндров двигателей ЯАЗ-М206
Для проверки состояния двигателя через одно первое техническое обслуживание рекомендуется, пользуясь простейшими жидкостными манометрами, заполненными водой или ртутью, показанными на рис. 3, проверить давление газов в картере и давление воздуха в воздушной камере. Давление газов Должно быть не более 160 мм вод. ст. при числе оборотов коленчатого вала 2000 в минуту.
Изменение давления воздуха в воздушной камере по сравнению с первоначальным должно быть не более 50 мм рт. ст.
При измерении давления газов в картере манометр присоединяют к трубке маслоизмерительного стержня, при измерении давления в воздушной камере — в месте забора воздуха для компрессора.
Рис. 3. Трубчатый манометр:
а — ртутный; б — водяной
Второе техническое обслуживание
Кроме операций первого технического обслуживания, при втором техническом обслуживании необходимо выполнить следующее.
1. Проверить работу всех насос-форсунок со снятием их с двигателя. Проверять рекомендуется на специальных приспособлениях, описанных в разделе «Проверка насос-форсунок».
Разборку и обслуживание насос-форсунок производить при наличии признаков ненормальной работы, выявленных при их проверке, а также при наблюдении за работой двигателя. Одновременно проверить установку насос-форсунок, правильность затяжки гаек их крепления (крутящий момент 2,60—3,30 кгм) и регулировку. Насос-форсунки рекомендуется устанавливать в те же стаканы, в которых они стояли до снятия.
2. Проверить компрессию в цилиндрах с помощью компрессомера после прогрева двигателя при числе оборотов коленчатого вала 500 и 1000 в минуту. Компрессомер последовательно устанавливают во все цилиндры двигателя (раздел «Недостаточная компрессия в цилиндрах двигателя»). Величину компрессии во всех цилиндрах при числе оборотов коленчатого вала 500 и 1000 в минуту необходимо записать в карте технического обслуживания.
Если компрессия недостаточна или разница в компрессии отдельных цилиндров слишком велика, следует разобрать двигатель и устранить неисправность.
3. Проверить затяжку гаек крепления головки блока цилиндров. При необходимости подтянуть гайки, как указано в разделе «Первое техническое обслуживание», пункт. 3.
4. Проверить регулировку соединения реек насос-форсунок с регулятором числа оборотов (раздел «Регулировка двигателя»).
5. Проверить через смотровые люки количество нагара, отложившегося на стенках продувочных окон блока цилиндров. При большом количестве нагара снять головку блока цилиндров и при положении поршня в н. м. т. прочистить окна деревянным стержнем диаметром 7 мм, Удалить грязь из воздушной камеры. В случае обнаружения лопнувших поршневых компрессионных колец заменить их.
6. Проверить давление топлива в подводящей топливной магистрали, включая специальный контрольный манометр между топливным насосом и насос-форсункой. Давление должно быть не менее 1,5 кг/см2 и не более 3 кг/см2 при 2000 об/мин коленчатого вала. При давлении топлива более 3 кг/см2 надо снять насос-форсунки для переборки и замены в них фильтров; при пониженном давлении заменить фильтрующие элементы топливных фильтров грубой и тонкой очистки. В случае отсутствия контрольного манометра нужно заменить элементы обоих топливных фильтров.
7. Проверить циркуляцию топлива в системе питания. При числе оборотов коленчатого вала 1200 в минуту из отводящей магистрали должно вытекать не менее 1,5 л топлива в минуту. Если подача топлива меньше, выявить причины и добиться нормальной подачи.
При нормальной подаче из отводящей магистрали должна вытекать прозрачная струя топлива. Если в струе видно большое количество пузырьков воздуха, вследствие чего струя становится светлой и непрозрачной, необходимо устранить подсос воздуха.
8. Сменить фильтрующий элемент фильтра тонкой очистки топлива. Допускается его восстановление, если элемент изготовлен из древесной муки (способ восстановления указывается в прилагаемой к каждому элементу инструкции).
9. Промыть систему смазки. Для этого двигатель необходимо нагреть до температуры охлаждающей жидкости 70°, снять элемент масляного фильтра тонкой очистки, промыть элемент фильтра грубой очистки, слить из поддона отработанное масло и залить в поддон смесь из 60% индустриального масла 20 (ГОСТ 1707—51) и 40% дизельного масла. После этого двигатель должен работать 4—5 минут при минимальном числе оборотов коленчатого вала на холостом ходу. Затем смесь полностью слить, в систему залить свежее масло, повторно промыть элемент фильтра грубой очистки масла и установить элемент фильтра тонкой очистки.
10. Промыть систему охлаждения, как указано в разделе «Обслуживание системы охлаждения», и очистить от грязи сердцевину радиатора.
11. Проверить работу термостата и системы охлаждения.
12. Проверить состояние электропроводки и очистить ее от пыли и грязи.
13. Промыть топливный бак.
14. Смазать подшипник водяного насоса. Для этого консистентную смазку нагнетать шприцем до появления свежей смазки из контрольного отверстия. Не следует резко подавать смазку во избежание выдавливания фетровых уплотнений подшипника.
15. Сменить смазку в картере коробки передач.
Третье техническое обслуживание
При третьем обслуживании, кроме полного объема работ первого и второго технических обслуживаний, необходимы следующие операции.
1. Сменить элемент топливного фильтра грубой очистки. Если Установлены увеличенные сроки между обслуживаниями, элемент нужно менять не реже чем через 700 час. работы двигателя.
2. Снять и промыть поддон, промыть сетку заборника масляного насоса.
3. Снять насос-форсунки, разобрать и отремонтировать при необходимости.
4. Промыть или очистить масляный радиатор (если на элементе масляного фильтра грубой очистки образуется большое количество отложений и давление масла в системе понижено, масляный радиатор следует промывать чаще).
5. Смазать генератор.
Через каждое третье техническое обслуживание следует снимать впускной трубопровод и проверять состояние нагнетателя.
В том случае, когда давление масла близко к нижнему пределу или ниже его, требуется проверить зазоры в сопряжениях коленчатого вала с коренными подшипниками.
Сезонное обслуживание
При переходе с летней эксплуатации на зимнюю нужно, кроме замены масла и топлива, проверить работу термостатов системы охлаждения и пусковых подогревательных устройств. Проверить электрофакельный подогреватель, сняв его с двигателя; аккумуляторные батареи подзарядить.
При применении жидкостей, замерзающих при низкой температуре, следует добиться полного устранения утечки из соединений системы охлаждения.
При переходе с зимней эксплуатации на летнюю надо промыть систему охлаждения и очистить радиатор.
Во время сезонного обслуживания следует промыть топливные баки, топливные фильтры и систему смазки.
Рекламные предложения:
Читать далее: Особенности зимней эксплуатации двигателей
Категория: — Двигатели ЯАЗ-М204 и ЯАЗ-М206
Главная → Справочник → Статьи → Форум
stroy-technics.ru
Обслуживание двигателя во время работы
Обслуживание двигателя во время работы должно производиться строго в соответствии с требованиями заводской инструкции, в которой учитываются особенности данного двигателя.
Некоторые общие указания по уходу за двигателем состоят в следующем.
После пуска двигателя в ход необходимо осмотреть все доступные части двигателя с целью проверки их действия. Во время работы
следует непрерывно и периодически наблюдать за двигателем, используя контрольно-измерительные приборы. Нужно:
1. Следить за нагрузкой двигателя, числом оборотов коленчатого вала и работой регулятора, не допуская длительной перегрузки двигателя (обычно не свыше 10%). В больших силовых установках для периодического контроля мощности и распределения ее по цилиндрам применяют индикатор для снятия индикаторных диаграмм или «гребенок» (наибольших давлений), а также пиметр — для измерения среднего давления по времени. Для определения наибольших давлений в цилиндрах иногда применяют максиметр.
Температура отработавших газов является показателем нагруженности двигателя и определяется по показаниям термометров, установленных на выпускных патрубках каждого цилиндра, или при помощи термопар и гальванометра с переключателем.
При полной нагрузке двигателя температура отработавших газов не должна выходить за пределы норм, указанных в заводской инструкции. Обычно этот предел:
для четырехтактных дизелей (без наддува)…………………………………………. 450° С
для двухтактных дизелей………………………………………………………………….. 300° С
Для быстроходных двигателей температура отработавших газов несколько выше.
Окраска отработавших газов также дает возможность выяснить перегрузку двигателя в целом или по отдельным цилиндрам. Кроме того, окраска газов указывает на качество сгорания топлива. При номинальной нагрузке выходящие газы должны быть почти бесцветными. Черный цвет (или темно-серый) указывает на неполное сгорание топлива, что характеризует перегрузку двигателя, ненормальную работу топливной системы или системы продувки. При ненормальном цвете выхлопных газов путем поочередного кратковременного открытия индикаторных кранов определяют дымящий цилиндр, а затем находят и при первой возможности устраняют причины дымления.
Нормальное эксплуатационное число оборотов следует поддерживать по показанию тахометра. Повышение числа оборотов свыше нормального вызывает перегрузку двигателя. Число оборотов можно регулировать затяжкой пружин регулятора. При большом колебании числа оборотов необходимо немедленно выяснить и устранить его причину или остановить двигатель.
- Наблюдать за давлением и правильной подачей масла своевременной чисткой фильтров. У двигателей с циркуляционной системой смазки необходимо следить за разностью давления масла до и после фильтра, для чего устанавливают в этих местах манометры.
При увеличении разности давления до определенного предела, согласно инструкции, масло переключают на другой парный фильтр» а работавший ранее вскрывается для чистки. При включении фильтра в работу из него выпускают воздух через воздушный кран. Снижение разности давлений до и после фильтра указывает на повреждение фильтра. В этом случае надо немедленно переключить поток масла на парную секцию фильтра, а поврежденный фильтрующий элемент заменить другим.
Один-два раза в смену следует проверить уровень масла в маслосборнике и при необходимости добавлять масло в соответствии с меткой, нанесенной на маслоуказательном щупе.
Температура в циркуляционной системе смазки контролируется по термометрам, установленным до и после холодильника. Максимальная температура в системе смазки, а также перепад температур масла до и после холодильника должны укладываться в нормы, установленные заводской инструкцией.
Максимальная температура в системе смазки двигателей (до холодильника) 55—90° (предельно допустимая 95? С). Если при полном включении холодильника максимальная температура масла превысит норму, установленную инструкцией, необходимо устранить причину повышения температуры. Если повышенный нагрев масла не может быть устранен, необходимо остановить двигатель.
При внезапном уменьшении давления масла в циркуляционной системе следует выяснить причину и устранить. Если не удастся повысить давление масла до нормы, нужно двигатель остановить. При уходе за масляной системой необходимо систематически наблюдать за движущимися частями, к которым масло не подается от циркуляционной системы. Следует следить за работой капельниц, смазывающих колец при кольцевой смазке и пр.
В двигателях с картерной продувкой необходимо следить, чтобы в картере не скоплялось масло, так как возможен захват его продувочным воздухом в цилиндр. Это может привести к самопроизвольному повышению оборотов и разносу двигателя.
- Наблюдать за температурой охлаждающей воды, отрегулировав подачу ее таким образом, чтобы температура выходящей из крышек цилиндров воды была в пределах 40—45? С при жесткой воде и при мягкой воде не превышала 70° С. При циркуляционном охлаждении рекомендуется перепад температур воды К) 15° С.
Если по какой-либо причине температура выходящей воды становится слишком высокой, то ни в коем случае нельзя резко увеличивать подачу холодной воды. Увеличить подачу охлаждающей воды следует постепенно. Если увеличить подачу невозможно и температура выходящей воды не падает, следует снизить нагрузку двигателя или остановить его.
- Следить за нормальным поступлением топлива к топливным насосам (с помощью пробных краников), за чистотой фильтров, за уровнем топлива е расходных баках и периодически выпускать отстоявшуюся воду из расходных баков и фильтров. Периодически выпускать воздух из топливной системы.
5. У двухтактных двигателей следить за давлением продувочного воздуха по ртутному U-образному манометру.
6. Следить за давлением в баллонах. Нужно продувать (удалять масло, воду) пусковые баллоны при каждом заполнении, а рабочие баллоны (компрессорных дизелей) — через каждые 4—5 час. работы.
- Следует периодически производить обход двигателя и проверять состояние всех доступных для осмотра частей. Путем ощупывания рукой крышек картера, расположенных против шатунных подшипников, можно примерно судить о степени нагрева различных шатунных подшипников. Нагревание щитов происходит вследствие отбрасывания на них горячего масла, вытекающего из указанных подшипников. Если подача масла в шатунные подшипники совсем прекратится, то крышки картера станут холодными.
Следует периодически проверять ощупыванием температуру корпуса и кожухов трущихся деталей двигателя (регулятора, привода распределительного вала и пр.).
При нагреве какой-либо части двигателя следует прежде всего усилить смазку, повышая по возможности давление масла. Если это не поможет, следует понизить нагрузку двигателя.
8. Следует внимательно прислушиваться к стуку в цилиндрах, в приводах впускных и выпускных клапанов, в шестернях и топливных насосах. В случае внезапного появления ненормальных стуков необходимо установить их место и причины. При быстром нарастании сильных стуков двигатель должен быть немедленно остановлен.
9. У калоризаторных двигателей необходимо следить за степенью нагрева калоризатора, не допуская охлаждений и перегревов (держать вишнево-красный накал).
При работе газогенераторной установки контролируется уровень топлива в газогенераторе и производится систематическая его загрузка. В зависимости от сорта и состава газифицируемого топлива через 2—3 часа очищают колосниковую решетку газогенератора. Уровень воды в испарителе поддерживают постоянным; температура газа после охлаждения в скруббере контролируется и регулируется путем изменения давления поступающей в скруббер воды. Разрежение в газовой магистрали контролируется пьезометрами. Температура газа по выходе из газогенератора поддерживается постоянной. Следует проверять поступление воды в скруббер, испаритель и зольник.
За последнее время для контроля за двигателем при его работе все большее применение получают дистанционные приборы непрерывного контроля. У большинства быстроходных двигателей приборы управления и контроля установлены на одном щитке (фиг. 169).
Контроль за работой двигателя необходимо отражать в журнале. В журнал нужно периодически записывать температуру охлаждающей воды, масла, отходящих газов и топлива перед насосом (если топливо подогревается). Здесь должно фиксироваться давление циркуляционного масла до и после фильтра. Число оборотов двигателя также отображается в журнале. Запись в журнале производится обычно через каждый час.
Регистрация всех указанных данных дает возможность быстро определить состояние двигателя и обнаружить изменения в его работе. В журнале должно быть отведено место для подробного изложения неполадок, происходящих во время работы двигателя, их причин и принятых мер.
vdvizhke.ru
Техническое обслуживание системы смазки двигателя
Система смазывания двигателя должна обеспечивать бесперебойную подачу масла к трущимся поверхностям с целью снижения потерь мощности на трение, уменьшения износа деталей, защиты их от коррозии, отвода тепла и продуктов износа от трущихся поверхностей,
Система смазки предназначена для подвода масла к трущимся поверхностям деталей двигателя, что уменьшает трение между ними и износ, способствует охлаждению нагретых поверхностей и удаляет продукты износа из зон трения. Основными неисправностями системы смазки являются: негерметичность системы, низкое или повышенное давление масла и его загрязненность (таблица 1).
Таблица 1 – Признаки неисправности системы смазки
Признак | Неисправность | Способ устранения |
1. Давление масла превышает допустимые значения | Неисправен датчик или указатель давления. Загрязнены каналы смазки. Используется вязкое масло. Загрязнение масляного фильтра | Заменить датчик или указатель давления. Промыть систему смазки. Заменить масло в соответствии с рекомендациями. Замена или очистка фильтрующего элемента |
2. Низкое давление масла | Низкий уровень масла. Разрегулирован или изношен редукционный клапан. Неисправен масляный насос. Износ коренных и шатунных шеек Засорена сетка маслозаборника | Долить масло. Отрегулировать или заменить редукционный клапан. Заменить шестерни или масляный насос в сборе. Произвести ремонт кривошипношатунного механизма. Очистить сетку маслозаборника |
3. Загрязнение масла | Засорены фильтрующие элементы. | Заменить или очистить фильтрующие элементы |
4. Снижение уровня масла | Негерметичность системы смазки. Угар масла. | Заменить сальники коленвала и уплотнение поддона, клапанных крышек и т.д. Заменить маслосъемные колпачки и (или) провести ремонт цилиндропоршневой группы |
Диагностирование системы смазки осуществляется визуально (по наличию подтеканий) и переносными приборами. Места течи определяют по пятнам и подтекам масла на двигателе и под автомобилем при его стоянке.
От исправного состояния системы смазывания, своевременного проведения ТО и устранения неисправностей в процессе эксплуатации автомобиля в значительной степени зависит надежность работы двигателя.
В процессе эксплуатации автомобиля необходимо периодически проверять уровень и состояние масла в картере двигателя, своевременно менять масло, очищать и промывать фильтры, менять фильтрующий элемент тонкой очистки, следить за давлением масла в системе смазывания и не допускать подтекания масла из фильтров, масляного радиатора, картера двигателя и соединений маслопроводов.
а-щуп дизельного двигателя; б-щуп бензинового двигателя
Рисунок 17 – Метки маслоизмерительного щупа
При проверке уровня масла автомобиль должен находиться на ровной горизонтальной площадке. После остановки двигателя должно пройти 3…5 минут, чтобы масло стекло в поддон картера. Затем вынимают и протирают щуп, замеряют уровень масла, который должен находится между метками «min» и «max». При необходимости масло доливают через маслозаливную горловину через воронку с сетчатым фильтром.
Низкий уровень масла в картере двигателя приводит к нарушению его подачи к трущимся поверхностям, к их перегреву и даже к выплавлению антифрикционного сплава вкладышей подшипников коленчатого вала.
При повышенном уровне масла появляется нагар на стенках головки цилиндров, днищах поршней и головках клапанов. Избыток масла приводит к утечке его через сальники и уплотнительные прокладки.
Причинами повышенного расхода масла могут быть: износ, пригорание или поломка поршневых колец, закоксование отверстий в кольцевых канавках поршня, износ канавок поршневых колец по высоте, износ цилиндров, образование на них царапин. Изношенные поршневые кольца, поршни и гильзы цилиндров следует заменить.
Повышенный расход масла может быть также от засорения клапана или трубки вентиляции картера двигателя.
Во время работы двигателя (вследствие нагрева и распыливания) масло в картере интенсивно окисляется, в результате чего образуются твердые (кокс) и мягкие (смолы) продукты окисления. Смолы, отлагаясь на горячих деталях картера, клапанной коробки и в маслопроводах, ухудшают условия подачи масла к трущимся частям. Образующиеся кислоты вызывают коррозию трущихся поверхностей и особенно сильно воздействуют на антифрикционный сплав тонкостенных вкладышей.
В результате неполного сгорания пары топлива в виде конденсата попадают из цилиндра в картер, разжижают масло, ухудшают его смазочные свойства — вязкость и липкость.
При заправке двигателя маслом необходимо соблюдать требуемую чистоту заправочного шланга с наконечником, заправочной посуды и маслозаливной горловины, так как в картер могут попадать механические примеси, которые увеличивают абразивный износ трущихся деталей двигателя.
Причинами понижения давления масла могут быть: снижение уровня масла в поддоне двигателя, повышение его температуры, загрязнение маслосборника, фильтрующего элемента фильтра грубой очистки или трубопроводов (масляных каналов), течь масла в соединениях, недостаточная производительность масляного насоса, неплотное прилегание редукционного клапана или износ подшипников коленчатого вала. Для устранения причин пониженного давления масла прежде всего надо убедиться в наличии необходимого количества масла в поддоне двигателя, исправности указателя давления масла и его датчика.
Исправность указателя давления масла проверяют заменой его контрольным прибором. Пониженная вязкость масла может быть вызвана попаданием топлива в цилиндры из-за неполного его сгорания. Повышенная температура масла (свыше 120°С) возможна из-за неисправной системы охлаждения. Уменьшение вязкости масла в поддоне может быть связано с разжижением его топливом. Эта неисправность устраняется подтяжкой соединений сливной топливной магистрали у дизеля или устранением причин, вызывающих перебои в работе свечей зажигания, повышение уровня топлива в карбюраторе.
При обнаружении течи масла следует ее устранить подтяжкой штуцеров, пробок и креплений приборов системы смазывания.
Своевременное и качественное ТО системы смазывания обеспечивает постоянную техническую готовность механизмов, агрегатов и двигателя в целом.
При падении давления масла в системе смазывания двигателей на щитке приборов загорается сигнализатор аварийного давления масла. Загорание сигнализатора на средней и большей частотах вращения коленчатого вала двигателя указывает на наличие неисправности. При этом двигатель необходимо остановить и устранить неисправность.
Редукционный клапан регулируется шайбами, установленными между колпачком клапана и пружиной.
При температуре воздуха более 15…20°С необходимо включить масляный радиатор. Его также следует включать независимо от температуры окружающей среды при езде в тяжелых дорожных условиях с большой нагрузкой и малыми скоростями движения.
Если давление масла занижено или завышено, его проверяют с помощью механического манометра, устанавливаемого на место масляного датчика, так как автомобильные указатели давления могут иметь значительную погрешность. Техническое состояние насоса можно определить только после его снятие на стенде (рисунок 18)
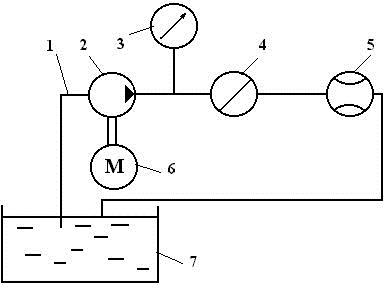
1 – всасывающая магистраль; 2 – испытуемый насос; 3 – манометр; 4 – двухходовой кран; 5 – расходомер; 6 – электромеханический привод насоса; 7 – расходный бак с маслом
Рисунок 18 – Схема установки для испытания насосов
При включенном приводе и закрытом кране 4 определяют давление начала открытия редукционного клапана, которое должно быть в пределах 0,35…0,45 МПа. Наиболее чувствительным параметром, комплексно оценивающим состояние насоса является его производительность. Она характеризует степень износа шестерен и корпуса насоса. Включив привод 6 и открыв кран 4 с помощью расходомера 5 определяют производительность в л/мин. Нормативное значение составляет 10…30 л/мин (большие значения соответствуют двигателям грузовых автомобилей).
Масляные фильтры служат для очистки масла от механических примесей (частиц металла, нагара и пыли) с целью увеличения продолжительности его работы, а также уменьшения износа деталей двигателя.
Замена масла в двигателе проводится при техническом обслуживании № 2 примерно через каждые 10…15 тыс. км пробега автомобиля или один раз в год (в инструкциях по эксплуатации каждой модели автомобиля указаны более точные значения пробегов). Если применяются синтетические или полусинтетические масла, то сроки их замены могут быть увеличены.
Отработавшее масло сливают из системы смазки прогретого двигателя, так как в этом случае оно сливается быстрее, более полно и вместе с ним из системы удаляется большее количество загрязнений. Большинство современных двигателей имеет два фильтра: полнопоточный (грубой очистки) и центробежный (тонкой очистки). У полнопоточных фильтров заменяют фильтрующие элементы, а центробежные разбирают, осматривают и промывают. Полнопоточный масляный фильтр меняют не только из-за его загрязненности, но и в связи с тем, что в фильтре остается до 0,3 л загрязненного масла.
В обычных условиях эксплуатации, когда центрифуга работает исправно, в колпаке ротора скапливается 150…200 г отложений, а в тяжелых условиях – до 600 г (4 мм толщины слоя отложений соответствует примерно 100 г). Отсутствие отложений указывает, что ротор не вращался, и грязь вымыта циркулирующим маслом. Это может быть либо из-за сильной затяжки барашковой гайки кожуха, либо в результате самопроизвольного отворачивания гайки крепления ротора.
У правильно собранного и чистого фильтра после остановки двигателя ротор продолжает вращаться 2…3 мин, издавая характерное гудение. Степень загрязненности фильтра можно оценить по его температуре. Если фильтр холодный, то он сильно засорен и масло проходит через редукционный клапан, минуя фильтр.
Перед заливкой свежего масла, систему смазки необходимо промыть. Если в двигателе использовалось синтетическое масло, имеющее в своем составе моющие средства, то промывка не производится, если минеральное, то промывка осуществляется через 2…3 замены, если полусинтетическое – через 5…6 замен. Промывка осуществляется следующим образом. После сливания отработавшего масла, не снимая масляный фильтр, в двигатель заливают специальную промывочную жидкость или промывочное масло (ВНИИНП-ФД, МПС-1, МПТ-2М, «Олиофиат Л-20» и др.). При отсутствии такого масла можно использовать смесь, состоящую из 50 % моторного масла и 50 % дизельного топлива, или маловязкое масло типа веретенного (МГ-22А). Промывочное масло заливают до отметки «МIN» на щупе. Запускают двигатель, оставляют его работать примерно 10 мин, потом глушат и сливают промывочное масло. По окончании промывки снимают масляный фильтр.
После замены фильтра в двигатель заливают свежее масло до середины между отметками «МIN» и «МАХ». Двигатель запускают и оставляют его работать на минимальных оборотах примерно 1 мин. После выключения двигателя через 3…5 минут (чтобы все масло стекло в масляный картер) проверяют уровень масла и при необходимости пополняют его.
После длительной эксплуатации или при недостаточной производительности масляный насос снимают и разбирают, все его детали промывают в керосине и продувают сжатым воздухом. При наличии трещин в корпусе или крышке насоса эти детали заменяют. Осматривают ведущую и ведомую шестерни насоса. Измеряют диаметр шестерен и определяют зазор между осью и ведомой шестерней, который должен находиться в пределах 0,017…0,057 мм, а также зазор между валиком насоса и отверстием в корпусе, который должен находиться в пределах 0,016…0,055 мм. При наличии значительного износа их заменяют на новые. Обе шестерни, установленные в корпусе насоса, должны легко вращаться рукой при прикладывании усилия к ведущему валику. Щупом проверяют зазор между корпусом насоса и зубьями шестерен.
Также проверяют зазор между зубьями шестерен, который не должен превышать 0,20 мм. С помощью линейки и щупа измеряют зазор между торцами шестерен и плоскостью корпуса насоса. Предельно допустимый зазор составляет (в зависимости от марки насоса) 0,15…0,20 мм, номинальный – 0,05…0,16 мм.
Крышка насоса может иметь неплоскостность до 0,05 мм. Если она больше, то крышку фрезеруют или шлифуют; при этом толщина припуска на обработку не должна превышать 0,2 мм.
Просмотров: 583
extxe.com