Динамическое торможение асинхронной машины
Еще одним видом торможения асинхронного электродвигателя, применимого как для машин с короткозамкнутым ротором, так и с фазным, является динамическое торможение. Динамическое торможение довольно распространено в системах электроприводов, так как не требует большой сложности схемы, имеет устойчивые характеристики в отличии от конденсаторного торможения и торможения противовключением.
Одна из возможных схем включения ниже:
Принцип работы динамического торможения довольно прост – двигатель отключается от сети с помощью контактора КМ1 и с помощью контактора КМ2 подключают к двум фазам электродвигателя постоянный ток, в нашем случае полученный с выпрямителя. Постоянный ток, который начнет протекать по двум обмоткам статора, создаст постоянное магнитное поле. При вращении ротора асинхронной машины в этом постоянном магнитном поле в обмотках роторных индуктируется ЭДС, которая в свою очередь приведет к появлении в роторе тока. При взаимодействии тока ротора с магнитным полем статора возникает тормозной момент.
В таком режиме работы асинхронный электродвигатель будет представлять собой обычный синхронный генератор с неявно выраженными полюсами и работающим с переменной частотой. Нагрузкой этого генератора будет сопротивление включенное в роторную цепь, или же при использовании асинхронной машины с короткозамкнутым ротором – его обмотка. При торможении будет снижаться скорость асинхронного электродвигателя, и соответственно начнет снижаться ЭДС ротора, его ток и тормозной момент.
Симметричное подключение всех трех обмоток при динамическом торможении невозможно без специальной коммутирующей аппаратуры. Поскольку подключение всех трех фаз к цепи постоянного тока не окажет существенное влияние на характеристику и существенно усложнит схему, используют подключение двух фаз к цепям постоянного тока как показано ниже для соединения звезда:
И для соединения в треугольник:
Также при выборе источника постоянного напряжения для выполнения динамического замедления асинхронной машины необходимо учитывать то, что при подаче на статорные обмотки постоянного напряжения изменится сопротивления обмоток, а именно, исчезнет индуктивное сопротивление. Именно поэтому, при выборе устройства динамического торможения необходим перерасчет напряжения (постоянное будет значительно меньше переменного), что бы не «спалить» обмотку двигателя.
В качестве такого источника могут использовать обычные диодные выпрямители неуправляемые подключенные через трансформатор, тиристорные преобразователи или же для машин больших мощностей специальные генераторы постоянного тока с пониженным выходным напряжением.
Для анализа явлений, происходящих в асинхронном электродвигателе при динамическом торможении, более целесообразно заменить режим работы синхронного генератора переменной частоты (в этом режиме работает асинхронный двигатель при динамическом замедлении) заменить эквивалентным ему режимом, когда статор вместо постоянного тока питается переменным. В этом случае совместно обмотками ротора и статора будет создаваться результирующая магнитодвижущая сила МДС. При замене эквивалентной режима работы необходимо, что бы выполнялось равенство магнитодвижущих сил, то есть F
Где: а) подключение обмотки статора к источнику постоянного напряжения;
б) создание обмотками статора пространственно смещенных друг относительно друга магнитодвижущих сил;
в) результирующая МДС. Векторная диаграмма.
Из рисунка в) можем определить:
Амплитуда данной МДС, создаваемая переменным I1 статорной обмотки:
Из равенства Fn=Fϟ можно вычислить эквивалентное значение переменного тока постоянному:
Из этого выражения следует то, что для создания номинального магнитного потока постоянный ток должен быть больше, чем переменный.
Где: In – постоянный, а I1 – действующий токи статора.
W1 – количество витков в одной фазе статорной обмотки.
Характерные величины для питания других схем постоянным током показаны в таблице ниже:
После определения I1, который эквивалентен постоянному, можно асинхронную машину в режиме динамического торможения представить как нормальный асинхронный электродвигатель. Ниже показана векторная диаграмма для токов асинхронной машины в предположении того, что к частоте сети и числу витков статора приведена обмотка ротора.
Но, работа асинхронного электродвигателя в режиме динамического торможения существенно отличается от его работы в нормальном режиме. При работе в нормальном (двигательном) режиме магнитный поток машины остается практически неизменным. А при динамическом торможении с изменением скорости вращения вала электродвигателя будет меняться и магнитный поток. Это вызвано изменением результирующей МДC, которая складывается с МДС статора (постоянный I) и изменяющейся МДС ротора (переменный I переменной частоты).
Приведенный к числу витков статора намагничивающий ток:
Из векторной диаграммы:
Возведя в квадрат получим:
При фиксированном значении частоты сети, синхронной скорости ω
Очевидно:
Преобразовав предыдущие выражения:
Или:
Подставив значение в предыдущее уравнение:
Получим:
Развиваемый двигателем момент электромагнитный будет определятся потерями во вторичном контуре:
Из полученного выражения можно определить, что возникающий момент при динамическом торможении будет определятся током I1 и есть функцией скорости вращения вала электродвигателя ν.
Исследовав выражения на максимум и минимум, найдем критический момент при относительной скорости:
А критический момент:
Ниже показана характеристика динамического торможения при различных роторных сопротивлениях и разных значениях статорных токов:
На графике кривые 1 и 3 снятые при постоянном сопротивлении роторной цепи и изменении постоянного напряжения статора, а 2 и 4 – при неизменном напряжении статора и меняющемся сопротивлении ротора.
Выражения момента может принять вид:
При динамическом торможении асинхронного двигателя его можно рассматривать как генератор синхронный в режиме короткого замыкания и при переменной скорости вращения. Соответственно Iкз:
Роторное сопротивление функции скорости Е = сω, и Хd = 2πfLd = kω.
Поэтому, ток короткого замыкания Ik практически не зависит от скорости при больших скоростях вращения вала машины:
Однако при сильном снижении скорости индуктивное сопротивление тоже снижается, и оно становится соизмеримым с активным. Активное сопротивление, в свою очередь, начинает существенно влиять на Ik в сторону его уменьшения. Данная зависимость приведена ниже:
Вид данной механической характеристики будет определять зависимость активной составляющей Ik от скорости вращения:
Механические характеристики асинхронного электродвигателя в режиме динамического торможения по форме практически ничем не отличаются от механических характеристик в двигательном режиме. Однако в режиме динамического торможения характеризующие его кривые имеют сильные отличия от двигательного режима:
- При динамическом торможении результирующий магнитный поток неподвижен, в отличии от двигательного режиме, где он вращается с синхронной скоростью;
- В двигательном режиме статорный ток меняется в зависимости от скольжения, при динамическом замедлении он неизменен;
- Магнитный результирующий поток в двигательном режиме постоянен, при динамическом же торможении, особенно при малых скоростях, он увеличивается. Это вызвано малым размагничивающим действием ротора;
- Для двигательного режима все характеристики берут начало в точке синхронной скорости (n0 или ω0), а при динамическом торможении начало находится в точке, которая соответствует неподвижному ротору.
Расчет механической характеристики асинхронного электродвигателя в режиме динамического торможения заключается в необходимости определить основные параметры схемы, которые обеспечат получение характеристики нужного вида. Для данного случая характеристики определяют значения момента критического Мк и критической скорости νк.
По универсальной или же экспериментально снятой характеристике холостого хода определяют реактивное сопротивления контура намагничивания:
Где Uф.хх – фазное напряжение холостого хода; I0 – ток холостого хода соответственно. В случае если νк приближается к единице, то Хμ рекомендуется определять по начальной линейной части характеристики холостого хода (ХХ).
Для известных Хμ, νк и Х2/ приведенное активное сопротивление ротора будет равно:
Последнее необходимо для того, что бы определить добавочное сопротивление ротора, которое подключается, конечно же, только для асинхронных электродвигателей с фазным ротором. Зная Мк и Хμ:
После этого для выбранной схемы подключения устройства динамического торможения с помощью таблицы указанной выше или же с помощью расчетов находят необходимое значение постоянного Iн. после чего переходят к построению характеристики механической без учета насыщения.
Насыщение оказывает влияние на динамическое торможение асинхронным электродвигателем тем, что при изменении тока намагничивания индуктивное сопротивление намагничивания Хμ будет величиной переменной, что соответственно скажется на тормозном моменте (он тоже будет переменен).
Зависимость Хμ = f(Iμ) может определятся по кривой намагничивания Е1 = f(Iμ). Для этого могут использовать либо экспериментально снятую кривую, либо универсальную для данного типа асинхронного двигателя. Что бы получить характеристику Е1 = f(Iμ) к зажимам статора асинхронной машины, приводимой в движение другой машиной с синхронной скоростью, подключают изменяющееся по величине напряжение. Потребляемый из сети ток, при таких условиях, и будет Iμ, соответствующий приложенному напряжению.
С учетом насыщения механическая характеристика строится по точкам. Для этого задаются рядом значений Iμ в пределах от I1 до 0 и с помощью кривой намагничивания определяют соответствующие значения индуктивности намагничивания:
Если значения I1, Iμ, а также Хμ и выполнив соответствующие преобразования в уравнениях, получим две неизвестные: I2/ и ν. Исключив I2/:
Откуда:
Интересующее нас выражение примет вид:
После чего, располагая знаниями I1, Хμ, ν находят значение момента по формуле приведенной ранее, которое соответствует ν с учетом насыщения. Таким образом, находят точки механической характеристики для значений Iμ от максимального значения до нуля.
Наиболее широко динамическое торможение распространено в электроприводах шахтных подъемных машин, но оно не менее активно применяется и в других отраслях промышленности.
Динамическое торможение асинхронного двигателя (схема, видео)
Электропривод является основой практического большинства современных механизмов. Одной из форм его работы является динамическое торможение асинхронного двигателя. Почему этот режим имеет такое значение и как он организовывается, попытаемся разобраться в этой статье.
Асинхронный двигатель и его работа
Очевидно, что режимы функционирования электродвигателей асинхронного типа напрямую зависят от их конструкции и общих принципов работы. Этот силовой агрегат совмещает в себе два ключевых компонента:
- Неподвижный статор. Пластинчатый цилиндр, в продольные пазы на внутренней поверхности которого укладывается проволочная обмотка,
- Вращающийся ротор. Совмещенный с валом сердечник (магнитопровод), который содержит прутковую обмотку на внешней стороне.
За счет различных частот вращения статора и ротора между ними возникает ЭДС, которая приводит вал в движение. Стандартное значение этого параметра может достигать 3000 об/мин, что требует определенного усилия для ее остановки. Из логических соображений можно заключить, что раз стартует двигатель за счет ЭДС, то и останавливать его тоже нужно электродинамическим путем.
Что такое динамическое торможение?
На этом месте может возникнуть закономерный вопрос: зачем что-то придумывать, если можно отключить двигатель от электросети, и он сам остановится? Это бесспорно так, но учитывая высокую частоту вращения и массо-центровочные характеристики, пройдет некоторое время до того момента, когда ротор полностью остановится. Этот период называется свободным выбегом и каждый в детстве его наблюдал, запуская простую юлу. Тем не менее, если работа оборудования предполагает частое использование пускателей, то такой режим приводит к очевидной потере времени.
Для быстрой остановки используются режимы торможения, которые предполагают трансформацию механической (в данном случае – кинетической) энергии искусственным путем. Все выделяют два основных вида торможения, которые подразделяются затем на подвиды:
- Механическое. Вал двигателя сообщается физически с тормозными колодками, вследствие чего возникает трение, быстрая остановка и выделение теплоты,
- Электрическое. Асинхронный двигатель останавливается за счет преобразования цепи подключения, вследствие чего механическая энергия трансформируется сперва в электрическую. Далее возможны два варианта ее израсходования, зависящие от схемы: либо избыток электричества выбрасывается в резервную цепь сети, либо трансформируется в тепло, за счет нагрева обмоток и сопротивления.
Динамическое торможение асинхронного двигателя относится к электрическому типу, так как в процессе обмотка статора отключается от сети с переменным током (две из трех фаз) и переводится в замкнутую цепь постоянного тока. При этом магнитное поле в статоре преобразуется из вращающегося в неподвижное. В роторе по-прежнему будет наводиться ЭДС, но момент будет направлен в обратную сторону, что приводит к торможению.
Классическая схема, как можно видеть на иллюстрации, предусматривает отключение от сети одной фазы контактором КМ1. При этом две другие фазы за счет контактора КМ2 переключаются в цепь с постоянным током через диодный мост.
Главным преимуществом такого способа торможения является возможность плавно контролировать тормозящий момент (за счет изменения напряжения или сопротивления) и осуществлять точную остановку.
Основные виды динамического торможения
Организация принудительной остановки асинхронного двигателя по электрическому принципу может быть осуществлена несколькими способами:
- Электродинамическим. Это классический вариант, при котором две фазы нужно закоротить и перевести на питания от цепи постоянного тока,
- Рекуперативным (генераторным). Характеризуется возвратом лишней электроэнергии в сеть,
- Противовключением. Этот вариант реализуется по схеме реверса, то есть с подключением фаз через пару магнитных пускателей,
- Самовозбуждением. Подключением к обмоткам статора батареи конденсаторов.
Виды динамического торможения
Классическое динамическое торможение
Эффективность такого режима работы зависит от расчета и значения следующих параметров:
- Величина тока, который подается через параллельную цепь на обмотки статора. Чем выше этот показатель, тем больше момент торможения,
- Величина сопротивления, которое вводится в цепь ротора. Чем выше по расчету сопротивление, тем быстрее тормозится двигатель,
- Величина магнитной движущей силы (МДС). Иногда ее называют ампер витками, поскольку расчет ведется по формуле F = I×W, где I – величина тока, а W – количество витков.
Обмотка статора при этом может подключаться как минимум пятью разными способами:
- Треугольником,
- Треугольником с закороченными фазами,
- Звездой,
- Звездой с закороченным нулем,
- Звездой с закороченными двумя фазами.
В каждом случае на основании векторной диаграммы ведется расчет МДС, тормозного сопротивления и напряжения цепи.
Рекуперативное торможение
Режим рекуперативного торможения
Поскольку избыток электроэнергии, который высвобождается в процессе торможения, направляется обратно в сеть через мост/батарею конденсаторов, то этот режим работы считается наиболее экономичным. Наиболее часто этот способ применяется в подъемно-транспортной технике и оборудовании, которое работает на перемещение грузов или собственного веса под уклон. Классический пример – лифт, где рекуперативное торможение приводного двигателя используется для начального подтормаживания. Также подобная схема широко используется в электрифицированном транспорте, например, в трамваях, троллейбусах, электричках. Применяют ее и в специальной технике, например, экскаваторах, широко используемых на строительстве мостов, дорог, зданий и т. п.
Принцип расчета и организации генераторного режима заключается в превышении частотой вращения ротора ее синхронного значения. В таком случае электромагнитный момент меняет направление, что приводит к торможению.
Торможение противовключением
Схема торможения противовключением
На практике режим противовключения может быть организован несколькими разными способами. Классическим является использование пары магнитных пускателей, подключенных по реверсной схеме. В этом случае, быстрая остановка агрегата осуществляется за счет изменения положения фаз (противовключение).
Основной пускатель КМ2 производит отключение двигателя М от сети. После этого параллельный пускатель КМ1 опять включает двигатель, меняя при это крайние фазы местами, то есть заставляя его вращаться в обратную сторону. Чтобы не допустить чрезмерного перегрева в цепь может быть введено дополнительное сопротивление. Также схема противовключения может быть реализована, если двигатель использовать в качестве тормоза для груза.
Торможение самовозбуждением
Схема торможения самовозбуждением
Этот вариант реализуется за счет подключения обмоток статора к параллельной конденсаторной батарее или мосту (расчет емкости придется вести). Когда двигатель отключается от сети и должен наступить режим выбега, угасающее магнитное поле начинает питать конденсаторы, а через них возвращается обратно в обмотку, создавая тормозной момент.
Как можно видеть, на практике используется целая гамма специфических режимов работы асинхронных двигателей, которыми можно добиться быстрой и точной его остановки. При частых пусках и остановках динамическое, рекуперативное, реверсное (на пускателях) или конденсаторное торможение (через расчет моста или батареи) могут повысить эффективность работ оборудования и снизить потери времени.
Обкатка двигателя: способы и особенности | ||||||||||||||||||||||||||||||||||||||||||||
|
Сборка, обкатка и испытание машин и агрегатов после капитального ремонта
Сборка является заключительным этапом производственного процесса ремонта машин и агрегатов. Сборочные работы составляют, как правило, большую долю в общей трудоемкости работ, выполняемых при ремонте. При этом в их составе значительное место занимают слесарные пригоночные работы. С помощью пригоночных работ достигается необходимое взаимное положение узлов и в ряде случаев требующийся характер сопряжений и посадок. От качества пригоночных работ в большой степени зависят точность отремонтированной машины, жесткость и стабильность размеров ее конструкции. При этом качество пригоночных работ во многом обусловлено квалификацией, навыками и интуицией рабочих. Поэтому при ремонте машин качеству выполнения слесарных работ со стороны работников отдела технического контроля уделяется большое внимание.
Технологический процесс сборки – это совокупность операций по соединению деталей в определенной последовательности с целью получения изделия, отвечающего заданным эксплуатационным требованиям. Сборочная операция – это технологическая операция установки и получения соединений сборочных единиц (узлов) изделия. Сборку начинают с установки и закрепления базовой детали. Поэтому в каждой сборочной единице должна быть заранее определена базовая деталь, с которой начинают сборку изделия, присоединяя к ней другие детали и сборочные единицы.
По последовательности выполнения различают:
- промежуточную сборку, под которой понимают сборку мелких элементов на слесарно-механических участках или сборку двух деталей перед окончательной обработкой;
- узловую сборку, под которой понимают сборку сборочных единиц изделия;
- общую сборку, под которой понимают сборку изделия в целом. При сборке объекта ремонта большое внимание уделяется восстановлению точности заложенных конструктором размерных цепей.
Размерной цепью называют систему взаимосвязанных размеров (звеньев размерной цепи), определяющих относительное положение поверхностей детали, деталей в узле или узлов в машине. В каждой размерной цепи один из размеров является замыкающим, а все остальные – составляющими. Замыкающим называют размер, величина которого в порядке выполнения технологических операций восстановления (изготовления) детали или сборки узла является функцией величин всех остальных размеров (составляющих). Составляющие размеры делятся на увеличивающие, которые при своем возрастании увеличивают замыкающий размер, и на уменьшающие, которые при своем возрастании уменьшают замыкающий размер. К точности замыкающего размера предъявляются особо высокие технические требования.
В процессе эксплуатации агрегатов установленная при их изготовлении точность размерных цепей нарушается вследствие изнашивания поверхностей или деформации деталей. Причем, как правило, в конкретной размерной или кинематической цепи изнашивание и деформация происходят у нескольких составляющих ее звеньев.
Восстановление точности размерной цепи (рис. 28) сводится к восстановлению точности ее замыкающего размера, которое может быть выполнено тремя методами: путем восстановления всех изношенных звеньев до их первоначальных размеров и отклонений, заданных конструктором; методом компенсации износа посредством перераспределения допусков и отклонений между составляющими размерами; методом введения при ремонте компенсирующих звеньев.
Первый метод, очевидно, наиболее трудоемкий и наименее технологичный, так как с увеличением деталей в размерной цепи уменьшается допуск на каждую деталь. Для его реализации весь объем работ, связанный с конструкторской, технологической, организационной подготовкой изготовления новых деталей, аналогичных изношенным звеньям, дополняется объемом работ, связанных с восстановительными операциями. Поэтому данный метод можно реализовать лишь в условиях крупносерийного или массового ремонтного производства или когда иные методы восстановления точности размерной цепи неприемлемы из-за условия, например, сохранения ее кинематической точности.
Рис. 28. Схема восстановления точности размерной цепи шкворневого соединения передней оси автомобиля ЗИЛ: а – шкворневое соединение; б – размерная цепь
В тех же случаях, когда выполнение последнего условия необязательно, а главным условием является достижение первоначальной точности замыкающего звена размерной цепи, применяют второй или третий методы.
Метод компенсации износа путем перераспределения допусков между составляющими размерами реализуется в два этапа. На первом этапе выполняется инженерный анализ размерной цепи: выявление замыкающего размера цепи; установление составляющих звеньев, подверженных механическому изнашиванию; выбор звена цепи, за счет которого можно восстановить ее точность; расчет номинального ремонтного размера звена, изменением которого восстанавливается точность цепи.
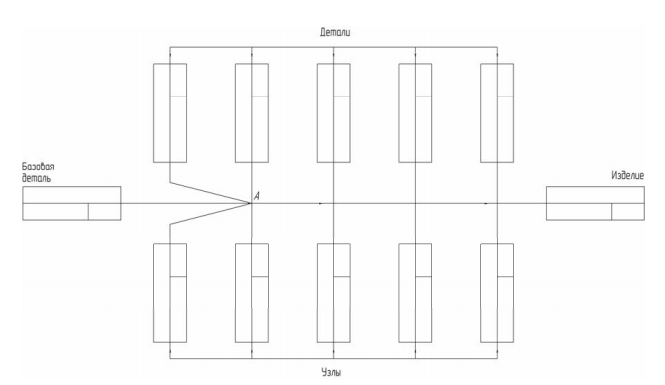
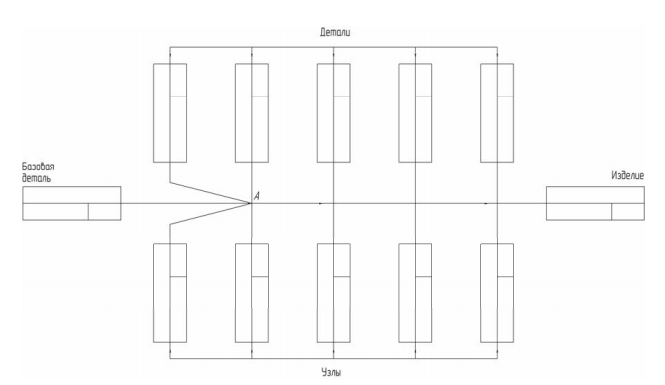
Рис. 29. Технологическая схема общей сборки агрегата
Рис. 30. Технологическая схема узловой сборки агрегата
В ремонтном производстве наиболее часто для восстановления точности размерных цепей применяют метод пригонки и регулирования, предусматривающий наличие в размерной цепи компенсирующего звена, положение которого регулируется в процессе сборки (регулировка зазоров, прокладки и т. п.). В этом случае инженерный анализ сводится к определению величины компенсатора.
Разработке технологических схем общей (рис. 29) и узловой сборки (рис. 30) предшествует изучение сборочных чертежей объекта ремонта, рабочих чертежей деталей, технических требований на сборку и приемку собираемых машин и агрегатов. На технологических схемах сборки каждый сборочный элемент изделия обозначается прямоугольником, разделённым на три части (рис. 31). Перед числовым индексом сборочной единицы изделия ставятся буквы сб (сборка) и номер порядка: 1сб, 2сб и т. д.
Рис. 31. Условное изображение сборочных единиц
Процесс общей сборки изображают на схеме горизонтальной линией. Её проводят в направлении от базовой детали изделия к собранному объекту.
В верхней части технологических схем в порядке последовательности сборки располагают условные обозначения всех непосредственно входящих в изделие деталей, в нижней части – сборочных единиц. На технологических схемах узловой сборки сборочные единицы разделяют на сборочные единицы высших порядков и детали.
Технологические схемы сборки по мере необходимости снабжают надписями-сносками, поясняющими характер сборочных работ (например, «Запрессовать», «Паять», «Клепать», «Регулировать» и др.) и выполняемый при сборке контроль (например, «Проверить зазоры» и др.). Контроль слесарных работ осуществляют с целью проверки полноты и качества их выполнения.
Технологические схемы отражают возможность одновременной установки нескольких составных частей изделия на его базовую деталь (рис. 29, точка А), что позволит повысить эффективность и
сократить длительность процесса сборки. В прямоугольнике, обозначающем сборочную единицу, в части А указывается наименование элемента, в части Б – числовой индекс согласно спецификации, в части В – число элементов, входящих в данное соединение.
После общей сборки проводят контроль агрегатов и машин с целью проверки комплектности, качества сборочных, регулировочных и крепежных работ.
Необходимо отметить, что эксплуатация собранных после капитального ремонта агрегатов с полной нагрузкой недопустима, так как относительно небольшая опорная площадь профиля механически обработанных рабочих поверхностей деталей приводит к высоким контактным давлениям. Эти давления вызывают разрыв разделяющей поверхности масляной пленки. В результате поверхности трущихся деталей на начальном этапе эксплуатации автомобиля попадают в состояние задира, которое сопровождается интенсивным износом деталей и сокращением их ресурса. Поэтому после сборки агрегаты подвергают обкатке и испытанию, задачами которых являются:
- подготовка агрегатов и машин к восприятию эксплуатационных нагрузок;
- выявление возможных дефектов, возникающих при недостаточно качественном восстановлении деталей и сборке агрегатов;
- выявление соответствия технических характеристик агрегатов и машин требуемым значениям.
Под обкаткой понимают подконтрольный процесс изменения геометрических и физико-механических параметров поверхностей трения деталей с целью получения их оптимальных значений, которым соответствуют наибольшая износостойкость и долговечность.
Сформировать оптимальные значения параметров качества рабочих поверхностей изделий (прежде всего шероховатости) и сократить время обкатки можно за счет применения специальных приработочных (обкаточных) масел.
Обкаточные масла, содержащие серу, олеиновую кислоту и другие вещества, способствуют быстрому формированию износостойкой поверхности трения за счет «омыления» металла. Имеется опыт использования обкаточных масел с добавлением мелкодисперсной алмазной пудры, позволяющей при обкатке узла на особых нагрузочных
и скоростных режимах быстро подготовить трущиеся поверхности к нормальной работе. Сам эффект обкатки собранных узлов автомобиля заключается в том, что в эксплуатацию они поступают с поверхностями трения, подготовленными для восприятия рабочих нагрузок.
Процесс обкатки делится на кратковременную обкатку на стендах и последующую, которая завершается в первоначальный период эксплуатации (в период подконтрольной эксплуатации).
Обкатка двигателей, как правило, состоит из следующих стадий: холодная обкатка (обкатка на холостом ходу), горячая обкатка без нагрузки, горячая обкатка под нагрузкой. В процессе обкатки проводят все необходимые регулировки и устраняют выявленные неисправности. После стендовой обкатки двигатель подвергают испытаниям на соответствие техническим требованиям.
Перед обкаткой двигателя проверяют возможность проворачивания коленчатого вала. Если коленчатый вал не проворачивается, двигатель снимается со стенда и отправляется на специальный стенд для устранения данной неисправности.
Обкатка двигателей может производиться на стендах, оборудованных электрическим асинхронным двигателем с фазным ротором и устройствами для измерения мощности двигателя, его крутящего момента и расхода топлива. Стендовая обкатка на холостом ходу начинается при температуре масла не менее 50С. В начале холодной обкатки проверяют герметичность уплотнений форсунок и головок цилиндров, надежность работы систем смазывания и охлаждения. При испытании на холостом ходу обкатку проводят последовательно на всех режимах, начиная с низших и заканчивая высшими скоростями. Обкатку на малых скоростях без нагрузки осуществляют при обильном смазывании не менее получаса, после чего меняют масло.
При холодной обкатке асинхронный двигатель работает как электродвигатель, который приводит во вращение коленчатый вал, а при горячей, когда частота вращения коленчатого вала превышает синхронные обороты (1400 об/мин), – как генератор, приводимый во вращение испытуемым двигателем, создающий тормозной момент. При этом энергия двигателя внутреннего сгорания рекуперируется и передается в электрическую сеть. Для плавного повышения оборотов коленчатого вала двигателя обычно используют частотный регулятор.
В начальный период обкатки, когда происходит интенсивное изнашивание и формирование оптимальной, с точки зрения износа, шероховатости рабочих поверхностей, контролируют частоту вращения коленчатого вала, температуру масла в картере двигателя, потери на трение и др.
Необходимо отметить, что при стендовой обкатке двигателя не должны слышаться резкие стуки и шумы, выделяющиеся из общего шума работы двигателя. Также не допускается резкое изменение нагрузки и частоты вращения двигателя, течь масла и прорыв отработавших газов в картер. Горячую обкатку завершают при стабилизации контролируемых параметров.
После обкатки двигателя на холостом ходу и под нагрузкой проводят испытания автомобиля на стенде тяговых качеств, который позволяет оценить его техническое состояние по тягово-экономическим характеристикам. Основное влияние на эти характеристики оказывает техническое состояние двигателя. Если в процессе испытания на стенде выявлено несоответствие технических показателей требуемым значениям, то для определения неисправности двигателя проводятся углубленная диагностика и устранение неисправностей.
Необходимо отметить, что для испытаний автомобилей в основном применяют стенды тяговых качеств, оснащенные тормозными устройствами, расходомером топлива и беговыми барабанами, на которые устанавливают ведущие колеса. Стенды позволяют оценить мощность двигателя, тяговое усилие на ведущих колесах, расход топлива на различных скоростных и нагрузочных режимах, путь и время разгона до заданной скорости, потери мощности на трение в трансмиссии и др.
Для оценки мощностных характеристик двигателя могут также использоваться динамические стенды, содержащие большие инерционные массы, по интенсивности раскручивания которых колесами автомобиля можно судить о мощности двигателя и общем состоянии силового агрегата и трансмиссии.
Мощность двигателя может быть оценена и по его реакции на нагрузку при поочередном кратковременном отключении цилиндров (прекращение подачи топлива форсункой дизеля или искры – для карбюраторного двигателя). Степень уменьшения частоты вращения коленчатого вала будет характеризовать вклад отключенного цилиндра в общую мощность двигателя.
Информативным показателем состояния цилиндропоршневой группы является давление в камере сгорания на такте сжатия, которое измеряют компрессометром. Компрессию измеряют при подключении прибора к цилиндру через отверстие для свечи зажигания или форсунки.
Для оценки технического состояния топливной аппаратуры и системы зажигания вместо расходомера можно использовать газоанализатор и по наличию токсичных компонентов в выхлопных газах работающего двигателя делать заключение о состоянии двигателя. Действие серийно выпускаемых газоанализаторов основано:
- на определении теплового эффекта сгорания окиси углерода на предварительно нагретой каталитически активной платиновой нити (принцип дожигания СО до СО2). Чем больше концентрация окиси углерода, тем выше температура платиновой нити и выше ее электрическое сопротивление, что и является сигналом концентрации СО;
- на поглощении инфракрасной энергии излучения анализируемым компонентом газа (СО или углеводородами), в результате чего последний нагревается тем больше, чем выше его концентрация в газовой смеси. Оптико-абсорбционным датчиком температурные изменения преобразуются в электрические сигналы, которые фиксируются измерительным прибором;
- на методах газовой хроматографии, позволяющих определить чис-
ло компонентов, входящих в состав отработавших газов. Это возможно благодаря различной скорости движения каждого из компонентов вдоль оси адсорбента.
Степень задымленности выхлопных газов дизеля определяют дымомером, принцип работы которого основан на фотоэлектрической регистрации поглощения светового потока мерным объемом отработавших газов. Прибор содержит рабочую трубу, в которую поступает анализируемый газ, и эталонную трубу, куда вентилятором нагнетается чистый воздух. При расположении электрической лампы и фотоэлемента по торцам эталонной трубы показания прибора настраивают на нулевое значение поглощения (0%). После этого поворотом рукоятки лампу и фотоэлемент переводят к торцам рабочей трубы и производят измерение дымности. Полное поглощение светового потока соответствует 100% дымности.
Контроль состояния двигателей с системой электронного управления впрыском топлива осуществляется специальными тестерами и компьютерными программами, позволяющими выявлять ошибки в работе датчиков, сигналы которых используются при задании режимов работы двигателя. На рис. 32 показано диагностическое оборудование, используемое для контроля современных автомобилей.
Рис. 32. Диагностическое оборудование для электронных систем автомобилей
Диагностируемые неисправности определяются системой самодиагностики установленного на автомобиле блока управления и отображаются появлением кода ошибки при проведении диагностики с помощью подключаемых к блоку управления тестеров (сканеров). Считываемые тестерами с электронного блока управления параметры могут представляться в текстовом или графическом виде. Для обработки данных диагностики автомобиля и введения базы данных тестеры работают в режиме использования компьютера типа IBM®PC. Обмен ведется через канал связи тестера с помощью специального адаптера или без его применения в зависимости от конструкции тестера.
Проще всего определить неисправность, связанную с выходом из строя (поломкой) какого-либо элемента системы управления. Такие ошибки, как правило, относятся к простым неисправностям, потому что имеют четкий алгоритм их выявления и последующего ремонта. Эти алгоритмы приведены в книгах по руководству и обслуживанию электронных систем управления. Однако не всегда появление кода ошибки однозначно определяет причину сбоя в работе двигателя или автомобиля.
Гораздо труднее понять, что датчик или элемент системы не удовлетворяет техническим требованиям и его работа приводит к сбоям в функционировании системы. Неопределенные неисправности не отображаются системой самодиагностики блока управления, об их возникновении можно судить только по поведению двигателя или автомобиля.
В управляющей программе электронного блока управления подсистема самодиагностики позволяет при появлении аварийных отклонений вызывать переход на резервные режимы работы системы управления, которые призваны сохранить работоспособность двигателя и возможность движения автомобиля при отказах элементов системы управления. Например, при отказе датчика температуры блок управления включает электродвигатель вентилятора, и он постоянно работает вне зависимости от температурного режима двигателя.
Для проверки и обслуживания стартера используют специальное оборудование, с помощью которого измеряют максимальный крутящий момент в режиме полного торможения ротора, величину потребляемого тока, частоту вращения ротора в режиме холостого хода. При испытании генератора на специальном стенде определяют напряжение и величину генерируемого тока при номинальной скорости вращения и в режиме начала отдачи. Для проверки работы приборов системы зажигания также имеется серийно выпускаемое технологическое оборудование, позволяющее оценивать бесперебойность искрообразования, момент подачи искры, проверять работу центробежного и вакуумного регуляторов распределителя зажигания.
Стендовая обкатка собранной коробки передач осуществляется с целью проверки правильности работы шестерен на всех передачах, легкости включения и отсутствия самопроизвольного выключения шестерен, а также определения виброустойчивости агрегата.
Следует отметить, что в процессе обкатки допускается равномерный шум без стуков и ударов. Проверка на вибрацию и шум позволяет оценить качество восстановления деталей и выполнения сборочных работ зубчатых передач, качество балансировки вращающихся деталей и узлов, выявить неисправность и неточность подшипников качения и т. п.
Для проверки на вибрацию и шум используют различные приборы: виброметры, вибрографы, микровибрографы, шумомеры и т. п.
При отсутствии соответствующих норм отремонтированный агрегат проверяют на вибрацию и шум путем сравнения замеренных величин с данными, относящимися к этому же или аналогичному агрегату в новом состоянии.
Сначала обкатку коробки передач производят на всех передачах без нагрузки. При этом на высшей передаче коробка должна проработать до достижения установленной температуры подшипников, но не менее 1 часа. Потом агрегат обкатывают при постоянной нагрузке с частотой вращения ведущего вала в пределах 1000…1400 об/мин.
Для испытания коробок передач под нагрузкой применяют стенды различной конструкции: электромагнитные, стенды с асинхронным электродвигателем, стенды с нагрузкой внутренними силами (по замкнутому контуру) и с гидравлическим тормозом.
При обкатке коробок передач, а также задних мостов на стендах с замкнутым силовым контуром их электродвигатель предназначен для преодоления сил трения в зубчатых передачах и подшипниках. Нагружение агрегатов производится за счет внутренних сил системы, например упругих сил закрученного торсиона.
Эффективность тормозной системы автомобиля может быть оценена по результатам испытаний на тормозных стендах. Простейший стенд, позволяющий производить экспресс-контроль, представляет собой четыре установленные на уровне пола подвижные площадки, датчики для контроля усилий, прилагаемых к площадкам при их сдвиге, и измерительную аппаратуру. Расположение подвижных площадок соответствует колесной базе и ширине колеи испытываемых автомобилей.
Автомобиль со скоростью 6…8 км/час наезжает на площадки, и в этот момент производится его торможение. Возникающие на колесах тормозные силы, гасящие инерцию движущейся массы, воспринимаются датчиками подвижных площадок, что позволяет судить о величине этих сил и равномерности тормозных сил по разным колесам автомобиля.
На другом тормозном стенде, принцип работы которого основан на использовании инерционных сил, автомобиль устанавливается всеми колесами на массивные ролики (или барабаны), связанные между собой приводом. Автомобиль начинает движение и раскручивает ролики до скорости 80…100 км/час. После отключения привода от вращающихся по инерции роликов начинается торможение колес. Об эффективности торможения каждого колеса судят по угловому замедлению вращающихся роликов или общему числу оборотов до их остановки. Для того чтобы учесть возможную разницу трения в подшипниках роликов стенда, его периодически тарируют, раскручивая соединенные приводом ролики электродвигателем с последующим отключением привода и замером выбега свободных от автомобиля роликов.
Конструкция рассмотренного динамического стенда позволяет оценивать работу тормозной системы в реальном диапазоне скоростей автомобиля и производить испытания тормозов с антиблокировочной системой.
В соответствии с требованиями ГОСТ стендовые испытания тормозной системы автомобилей на роликовых стендах (рис. 33) необходимо проводить при скорости вращения колес не более 3…5 км/час, контролируя поочередно тормозные силы колес каждой оси автомобиля (рис. 34).
Рис. 33. Общий вид тормозного стенда
Рис. 34. Схема тормозного стенда силового типа
Каждая пара замкнутых цепной передачей роликов для левого и правого колеса приводится в движение электродвигателем (моторредуктором), о величине тормозной силы судят по реактивному моменту балансирного мотор-редуктора. Для выключения привода при полной остановке испытуемого колеса к нему упруго поджимается ролик с датчиком блокировки колеса, как только ролик прекращает вращаться, мотор-редуктор отключается.
Испытания тормозной системы начинают при «холодных» тормозах, накачанных до нормального давления чистых и сухих шинах, работающем на малых оборотах двигателе (это необходимо, если в системе имеется вакуумный усилитель). На педаль тормоза легковых автомобилей прикладывают усилие, равное 490 Н, а грузовых и автобусов – 686 Н (величину усилия контролируют специальным датчиком, устанавливаемым на педаль, и ногой давят на этот датчик). Аналогично испытывают эффективность стояночного тормоза.
Удельная тормозная сила, определяемая как отношение суммы тормозных сил к весу автомобиля, в соответствии с требованиями ГОСТ должна быть равна 0,53 для легковых автомобилей (категория М1 по действующей классификации), 0,46 – для пассажирских автомобилей с числом мест более 8 и грузовых автомобилей, 0,45 – для многоосных прицепов. Неравномерность тормозных сил колес одной оси выражают отношением разницы сил к величине максимальной тормозной силы (в процентах). Для осей с дисковыми тормозами допустима неравномерность в 20%, для барабанных тормозов – 25%.
Контроль состояния рулевого управления производится серийно выпускаемым люфтомером, который состоит из пружинного динамометра, устанавливаемого на рулевом колесе, соединенной с ним шкалы для контроля угла поворота руля и стрелки, закрепляемой на рулевой колонке. Прибор позволяет замерять трение в рулевом управлении, для чего передние колеса вывешивают, и руль за рукоятку динамометра медленно поворачивают от крайнего левого до крайнего правого положения, наблюдая за показаниями динамометра. Для определения люфта правое колесо фиксируют в положении прямолинейного движения и, воздействуя на рукоятку динамометра, покачивают рулевое колесо вправо и влево, наблюдая за положением неподвижной стрелки относительно перемещающейся с рулевым колесом шкалы.
Суммарный люфт в рулевом управлении не должен превышать предельных значений, установленных изготовителем автомобиля в эксплуатационной документации, а при отсутствии таких данных – следующих предельных значений:
- легковые автомобили и созданные на базе их агрегатов грузовые
автомобили и автобусы………………………………………………………….10°
- автобусы………………………………………………………………………………20°
- грузовые автомобили…………………………………………………………….25°.
Суммарный люфт в рулевом управлении можно также определить серийно выпускаемым научно-производственной фирмой «МЕТА» электронным люфтомером ИСЛ-М (рис. 35), состоящим из телескопического захвата, который крепится на ободе рулевого колеса; приборного электронного блока, где размещаются оптико-механический преобразователь угла поворота, буквенно-цифровой индикатор и микропроцессорный преобразователь сигналов; датчика движения колеса, связанного с приборным блоком; тяги, необходимой для обеспечения проведения измерений при наклонах оси рулевой колонки менее 30° от вертикальной оси.
Принцип действия прибора ИСЛ-М основан на измерении угла поворота рулевого колеса автомобиля посредством преобразования импульсного сигнала оптико-механического датчика угла поворота в интервале срабатываний индуктивного датчика движения управляемых колес при выборе люфта рулевого управления в обоих направлениях вращения руля.
Рис. 35. Схема определения суммарного люфта в рулевом управлении: 1 – захват; 2 – приборный блок; 3 – индуктивный преобразователь перемещения; 4 – стойка; 5 – датчик движения; 6 – управляемое колесо
Для визуального наблюдения источников повышенного люфта в рулевом управлении могут быть использованы специальные стенды, состоящие из поворачивающихся площадок, на которые устанавливают передние колеса автомобиля. Под действием привода, в качестве которого могут использоваться пневматические камеры тормозной системы, площадка поворачивается вправо и влево, а слесарь, находящийся под автомобилем, наблюдает, в сопряжении каких элементов обнаруживается люфт.
Автомобили после испытаний на соответствие техническим требованиям проходят предварительную техническую приемку, а после подконтрольной эксплуатации в дорожных условиях – окончательную приемку. При сдаче отремонтированных агрегатов и машин отделу технического контроля их качество должно соответствовать техническим условиям на выдачу автомобилей из ремонта.
Подконтрольная эксплуатация в дорожных условиях, например, автомобилей КамАЗ производится на дорогах с твердым покрытием на расстояние 40…50 км с максимальной скоростью движения не более 40 км/ч и нагрузкой, не превышающей 75% номинальной грузоподъемности автомобиля.
В процессе обкатки в дорожных условиях проверяются исправность и надежность работы всех систем, узлов и агрегатов автомобиля. Так, контроль эффективности тормозной системы в дорожных условиях помимо измерения тормозного пути может включать измерение установившегося замедления, которое для грузовых автомобилей должно быть 4,5 м/с2. Контроль замедления осуществляют устанавливаемым в автомобиле механическим деселерометром или прибором, датчик которого состоит из пьезокристалла с приклеенной к нему некоторой массой. Как известно, произведение ускорения на массу выражает силу инерции, при воздействии которой на гранях кристалла возникает электрический потенциал, являющийся сигналом замедления.
После обкатки автомобиль тщательно осматривают, устраняют все выявленные неисправности и проводят дополнительные регулировки. В паспорте автомобиля заносят отметки о выполненном ремонте, фиксируют его комплектность, техническое состояние и соответствие отремонтированного автомобиля техническим условиям на капитальный ремонт. Соответствие техническим условиям гарантирует работоспособность автомобиля в течение определенного времени эксплуатации при проведении соответствующего технического обслуживания и ремонта.
В настоящее время гарантийный срок эксплуатации автомобилей составляет 12 месяцев со дня выдачи из ремонта при пробегах:
не более 20 тыс. км – для автобусов;
не более 16 тыс. км – для прочих автомобилей.
Передача автомобилей, прошедших капитальный ремонт, автотранспортным предприятиям производится на основании приемосдаточного акта.
Просмотров: 1 130
За и против обкатки мотора нового авто: пояснения и советы
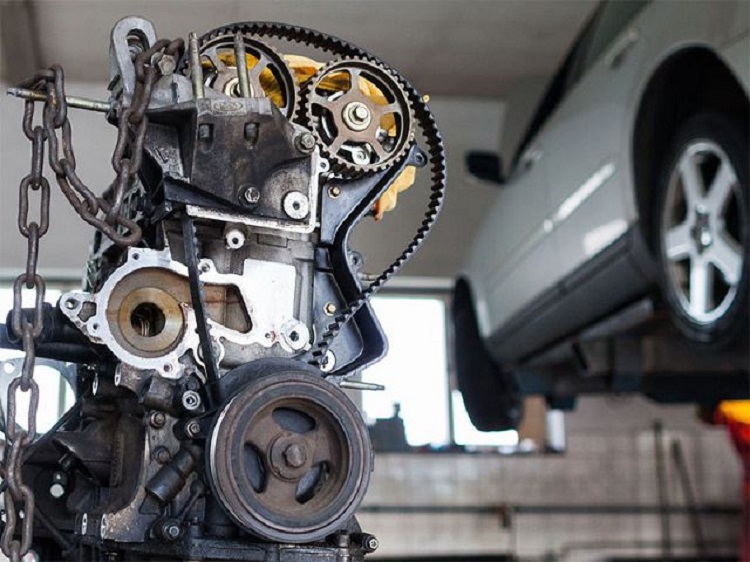
Автомобиль представляет собой сложный агрегат, который состоит из множества трущихся деталей, механизмов. Они работают синхронно, поэтому все подвижные элементы проходят этап так называемой притирки. По этой причине только что изготовленные агрегаты нуждаются в обкатке. Данную процедуру сегодня часто проводят на заводе.
Нужно ли проводить обкатку нового автомобиля после покупки – вопрос неоднозначный. Во многих инструкциях этому моменту уделяется всего несколько слов. Каждый владелец нового авто должен разобраться в этом.
Обкатывают ли современные моторы
Всего лишь несколько лет назад сторонников обкатки новых силовых агрегатов было значительно больше, чем противников. В последнее время все большую популярность получило мнение о том, что из-за продвинутых технологий изготовления современных двигателей обкатывать их нет особой необходимости. Данную точку зрения подтверждают известные автомобильные производители.
С другой стороны, даже концерн BMW отдает предпочтение проверенным методам эксплуатации нового авто. В рекомендациях по эксплуатации советуют первые 2000 км не перегружать силовой агрегат, разгоняя машину на больших оборотах. Такую позицию поддерживают компании Alfa Romeo и Dodge.
Другие производители не уделяют моменту обкатки слишком большого внимания:
- Renault рекомендует, но не настаивает, первую тысячу километров не ездить быстрее, чем 130 км/ч на оборотах 3000-3500 в минуту.
- Китайские производители не предъявляют никаких особых требований. Их рекомендации сводятся только к ограничениям скорости и оборотов.
- Honda рекомендует избегать начала движения «при полной подаче топлива», не буксировать прицепы первые 1000 километров. Также производитель не советует менять моторное масло раньше срока.
- Компания Mitsubishi заявляет о том, что требования к авто этой марки по обкатке полностью отсутствуют.
- Toyota для своего седана Avalon советует на протяжении первых 3000 километров избегать агрессивных торможений, рывков, а также ездить на высоких скоростях или пониженной передаче с постоянной скоростью.
- GM до первых 800 километров пробега категорически не рекомендует тормозить двигателем и выжимать педаль акселератора до упора.
- Отечественный производитель ВАЗ не предъявляет никаких особых требований по эксплуатации своих авто с целью “притирки” элементов мотора.
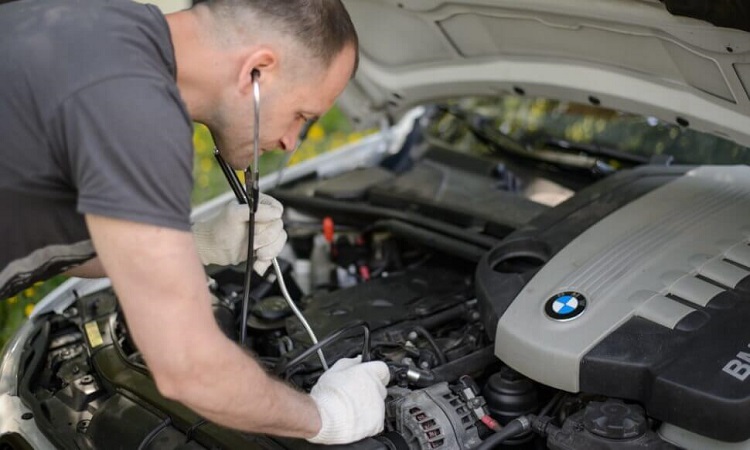
Смотрите также:
Виды обкатки
Двигатель новой машины нельзя нагружать на «все сто» до того момента, пока движущиеся детали полностью не притрутся друг к другу. Лучшими условиями для этого будет умеренная нагрузка. С другой стороны, современная технология производства силовых агрегатов подразумевает обязательную их подготовку в заводских условиях.
Обкатка нового автомобиля, сошедшего с конвейера завода, или после капитального ремонта производится несколькими способами.
С помощью специального стенда
В профессиональных автомобильных мастерских и СТО используются приспособления для обкатки двигателя после капитального ремонта. Их можно использовать двумя способами. При первом из них используется электромотор, приводящий в движение коленчатый вал.
Количество оборотов контролирует ЭБУ (компьютер), на который от разных деталей и узлов поступает информация через датчики. Электроника поддерживает заданную температуру, поэтому данный метод называется «холодная обкатка».
При горячем способе:
- Установленный на стенд двигатель работает в цикличном режиме.
- Каждый цикл состоит из 4-минутной работы с перерывом на 40 минут для полного остывания.
- Главное – не допускать нагрев силового агрегата выше 80 градусов.
- Данная процедура повторяется 3-4 раза.
Буксировка
Для решения задач обкатки можно использовать другой автомобиль и жесткую сцепку, с помощью которой присоединяется обкатываемое авто. На нем нужно выкрутить свечи, перевести рычаг переключения передач в нейтральное положение.
Буксирующая машина должна плавно передвигаться по трассе исключительно на третьей скорости в течение часа.
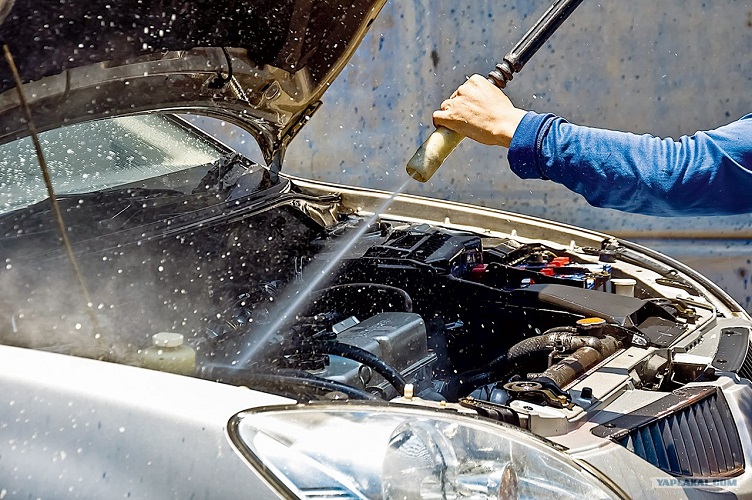
Смотрите также:
Самый простой способ
Наиболее популярным способом обкатки двигателя является аккуратное вождение. Для этого следует придерживаться во время езды средних оборотов, не впадая в крайности. Некоторые производители рекомендуют первую замену масла производить после 2000 километров пробега.
Нельзя допускать следующих ситуаций:
- длительной работы на холостом ходу;
- оборотов выше 3000 в минуту;
- резких разгонов и торможений.
Перед обкаткой следует проверить состояние авто и подготовить его при необходимости:
- В первую очередь проконтролировать уровень охлаждающей, тормозной жидкости, масла с помощью щупа.
- Проконтролировать давление в шинах.
- Проверить герметичность систем авто, заправить машину качественным топливом.
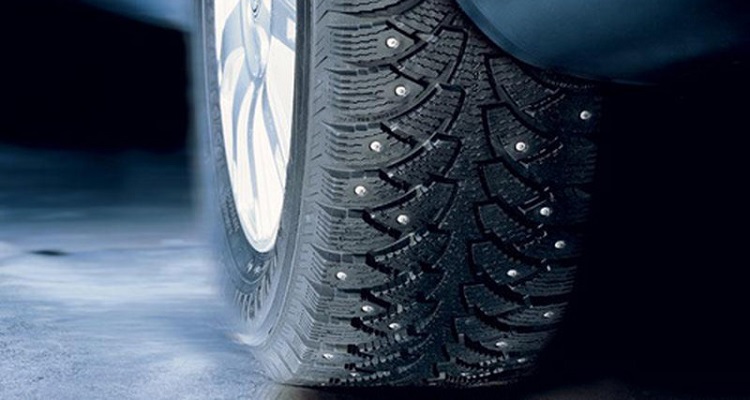
Смотрите также:
Правильная эксплуатация, качественное техническое обслуживание, аккуратная езда станет залогом качественной обкатки нового автомобиля.
[democracy]
[democracy]
Назначение и режимы обкатки двигателей автомобилей — Студопедия
Выявление скрытых дефектов деталей методом красок
Гильзу проводится по следующей методике.
Контроль подбора группы поршень-гильза методом опускания поршня в
Подбор поршня по гильзе цилиндра двигателя ЗМЗ 53 и проверка качества подбора
1. На ровную поверхность стола укладывается кусок толстой резины.
2. Острый край нижнего бурта гильзы смазывается моторным маслом и плотно
устанавливается на резиновый коврик.
3. Наружная поверхность поршня смазывается моторным маслом.
4. Поршень опускается в гильзу, при этом плоскость оси поршневого пальца
должна быть перпендикулярна плоскости сечения гильзы в месте
расположения маркировки группы (в соответствии с требованиями по
установке гильзы в блок цилиндров).
5. При правильном подборе поршень должен плавно опуститься вниз.
Этот метод применяют для выявления трещин на поверхности, размером меньше 20 мкм. Для этого поверхность окрашивают красной краской разбавленной керосином, затем убирают её и окрашивают поверхность белой краской. Через несколько секунд на белом фоне появляется трещина.
Обкатка — завершающая операция технологического процесса капитального ремонта двигателей внутреннего сгорания. В процессе обкатки и испытания отремонтированного двигателя происходит приработка поверхностей трения двигателя, подготовка его к эксплуатации под нагрузкой и всесторонний контроль за качеством капитального ремонта.
Оборудование и приборы для обкатки и испытания двигателей. Обкатывают и испытывают двигатели на ремонтных предприятиях на электрических тормозных стендах переменного тока КИ-5274, КИ-21118А и др.
Холодная обкатка. Холодная приработка двигателя проводится с ввернутыми форсунками. Перед пуском стенда двигатель прогревают горячей водой в течение 5—7 мин; коленчатый вал несколько раз проворачивают вручную для проверки исправности двигателя и правильной его установки на стенде; проверяют и при необходимости вновь регулируют тепловые зазоры в клапанном механизме. Начальную частоту вращения коленчатого вала при холодной приработке выбирают из условий надежного обеспечения подачи масла к трущимся поверхностям и его разбрызгивания.
В процессе холодной приработки с помощью стетоскопа прослушивают шумы и стуки распределительных шестерен, шатунных и коренных подшипников, поршневых пальцев и поршней. Проверяют давление масла в системе, которое должно быть не менее 0,1 МПа при частоте вращения коленчатого вала 500 об/мин; подачу масла к подшипникам коромысел и герметичность уплотнения форсунок в головках цилиндров; отсутствие течи воды и масла на двигателе.
При обнаружении дефектов приработку приостанавливают и продолжают ее только после их устранения.
По окончании холодной приработки проверяют и при необходимости регулируют тепловые зазоры между торцами клапанов и коромыслами.
Горячая обкатка без нагрузки. Перед горячей приработкой двигателя необходимо отрегулировать угол опережения впрыска топлива с погрешностью +1° и прокачать топливную систему ручным насосом, предварительно ослабив пробки топливного насоса высокого давления. При отсутствии пузырьков воздуха в топливе, выходящем из-под пробок, последние снова затягивают.
После пуска двигателя стетоскопом прослушивают шумы и стуки распределительных шестерен, шатунных и коренных подшипников, поршневых пальцев и поршней; проверяют герметичность всех соединений топливной системы двигателя, отсутствие течи масла, воды, пропуска воздуха и отработавших газов.
При обнаружении дефекта приработку приостанавливают и продолжают только после его устранения.
Горячая обкатка под нагрузкой. На этапе горячей обкатки под нагрузкой происходит приработка поверхностей трения, работающих под действием только инерционных сил (на тактах выхлопа и всасывания), а также поверхностей, работающих под действием суммарных сил (на такте рабочего хода). Режимы горячей обкатки под нагрузкой двигателей А-01М при частоте вращения коленчатого вала 1665—1735 об/мин приведены в табл. 17.
В ходе горячей приработки под нагрузкой прирабатываемый двигатель тщательно осматривают и прослушивают.
Торможение электродвигателя: способы и схемы
Торможение электродвигателя применяют, если необходимо сократить время свободного выбега и фиксацию механизма в конкретном положении. Существует несколько видов принудительной остановки устройства. Это механическое, электрическое и комбинированное. Механическое устройство представляет собой тормозной шкив, закрепленный на валу, с колодками. После отключения устройства колодки прижимаются к шкиву. За счет трения кинетическая энергия преобразуется в тепловую, т.е. происходит процесс торможения. Остальные способы и схемы торможения электрического двигателя будут рассмотрены далее в статье.
Способы электрического торможения электроприводов
Для того чтобы быстро остановить устройство или обеспечить постоянную скорость вращения используют электрические способы остановки. В зависимости от схемы включения тормозные режимы подразделяют на:
- противовключения;
- динамический;
- рекуперативный.
Противовключения
Режим противовключения применяется при необходимости быстрой остановки механизма. Представляет собой смену полярности на обмотке якоря двигателя постоянного тока или переключения двух фаз на обмотках асинхронного электродвигателя.
В этом случае ротор вращается в противоположном направлении магнитного поля статора. Вращение ротора замедляется. При скорости вращения близкой к нулю с реле контроля скорости поступает сигнал, отключая механизм от сети.
На нижеприведенном рисунке представлена схема противовключения асинхронного электромотора.
После переключения обмоток возникает повышенное действующее напряжение и увеличение тока. Для его ограничения, в обмотки ротора или статора устанавливают дополнительные резисторы. Они ограничивают токи в обмотках в режиме торможения.
Динамическая остановка электропривода
Этот способ применяют на асинхронных машинах, подключенных к сети переменного тока. Он заключается в отключении обмоток от сети переменного напряжения и подачи постоянного тока на обмотку статора.
На вышеприведенном рисунке представлена схема торможения трехфазного двигателя постоянным током.
Подача постоянного напряжения осуществляется с помощью понижающего трансформатора для динамического торможения. Пониженное переменное напряжение преобразуется в постоянное диодным мостом и подается на статорную обмотку. Для торможения электромотора может применяться дополнительный источник постоянного тока.
При этом ротор может быть выполнен в виде «беличьей клетки» или ее обмотку подключают к добавочным резисторам.
Постоянное напряжение создает неподвижный магнитный поток. При вращении ротора в нем наводится ЭДС, т.е. электромотор переходит в режим генератора. Возникающая электродвижущая сила рассевается на обмотке ротора и добавочных резисторах. Создается тормозной момент. В момент остановки механизма постоянное напряжение отключается по сигналу реле скорости.
Механизмы, где применяется электродвигатель с самовозбуждением, динамическую остановку выполняют с помощью подключения конденсаторов. Они соединяются треугольником или звездой.
Схема приведена на нижеприведенном рисунке.
На выбеге остаточная энергия магнитного поля переходит в заряд конденсаторов, а затем она питает обмотку статора. Возникающий тормозной эффект останавливает механизм. Конденсаторная батарея может быть подключена постоянно или подсоединяться в момент отключения от сети. Такая схема получила название «конденсаторное торможение асинхронного двигателя».
Если необходимо быстро остановить двигатель, то после отключения от сети, замыкают контакты накоротко без гасящих резисторов. При соединении обмоток закорачиванием в них возникают большие токи. Для уменьшения токов к обмоткам подключают токоограничивающие резисторы.
На нижеприведенном рисунке представлена схема с токоограничивающими резисторами.
Режимы торможения моторов постоянного тока
Динамическое торможение электродвигателя постоянного тока осуществляется после отключения его от сети с замыканием обмотки ротора на тормозной реостат. Выделенная электрическая энергия рассеивается на реостате.
На вышеприведенном рисунке представлены схемы реостатного торможения двигателя постоянного тока.
Рекуперативное торможение электрических машин
Рекуперативное торможение электродвигателя характеризуется переводом двигателя в генераторный режим. При этом вырабатываемая электроэнергия возвращается в сеть или используется для подзарядки аккумулятора.
Этот режим широко применяется в электровозах, электричках, трамваях и троллейбусах. В момент торможения, вырабатываемая электроэнергия возвращается в электрическую сеть.
Режим рекуперативного торможения применяется для подзарядки аккумуляторов в гибридных автомобилях, электромобилях, электросамокатах, электровелосипедах.
Этот режим является наиболее экономичным и возможен при условии: если частота вращения ротора превышает частоту вращения холостого хода. Это условие выполняется, когда ЭДС электродвигателя превышает напряжение питающей сети. А ток якоря и магнитный поток меняют свое направление. Электрическая машина переходит в генераторный режим, возникает момент торможения.
На рисунке представлена схема торможения тягового двигателя а) с независимым возбуждением и стабилизирующим сопротивлением, б) с противовозбуждением возбудителя.
Режим рекуперации в асинхронных электрических машинах
Режим рекуперации применяется не только в двигателях постоянного тока. Его можно применять и в асинхронных двигателях.
При этом такой режим возможен в следующих случаях:
- Если изменить частоту питающего напряжения при помощи частотного преобразователя. Что возможно при условии питания асинхронного электродвигателя от устройства с возможностью регулирования частоты питающей сети. Эффект торможения наступает при уменьшении частоты питающего напряжения. При этом переход в генераторный режим происходит, когда скорость вращения ротора становится больше номинальной (синхронной).
- Асинхронные машины, которые конструктивно имеют возможность переключения обмоток, для изменения скорости.
- В грузоподъёмных механизмах, где применяется силовой спуск. В них монтируется электромотор с фазным ротором. В этом случае скорость регулируется с помощью изменения величины резистора, подсоединяемого к обмоткам ротора. Магнитный поток начинает обгонять поле статора, а скольжение становится больше 1. Электромотор переходит в режим генератора, вырабатываемая электроэнергия возвращается в сеть, возникает тормозной эффект.
Комбинированный режим
Комбинированные тормозные режимы применяются в электрических машинах, если необходимо быстро остановить и зафиксировать механизм. Для этого используют механический блок торможения в комбинации с электрическим торможением. Комбинация может быть различной. Это может быть и электрическая схема с противовключением, динамическим и рекуперативным режимами.
Вот мы и рассмотрели основные способы и схемы торможения электродвигателей. Если возникнут вопросы, задавайте их в комментариях под статьей!
Материалы по теме:
Что такое динамическое торможение и когда оно используется?
Когда двигатель находится в состоянии капитального ремонта, то есть нагрузка движется со скоростью, превышающей заданную скорость двигателя, двигатель действует как генератор и вырабатывает электрическую энергию из механической энергии. Однако этой электрической энергии нужно куда-то деваться, и наиболее распространенный способ ее высвобождения — динамическое торможение.
Как работает динамическое торможение
При динамическом торможении электрическая энергия, генерируемая при остановке, выделяется в виде тепла через транзистор и резистор с регулируемым напряжением.Фактически существует две версии схемы динамического торможения: «прерыватель» и «динамический тормоз». Схема динамического торможения включает в себя переключающее устройство (биполярный транзистор с изолированным затвором или IGBT), схему управления и резистор.
Прерыватель, с другой стороны, включает в себя только регулирующую схему и коммутационное устройство, а резисторы являются отдельными компонентами. Это позволяет подбирать резисторы соответствующего размера и устанавливать их удаленно, что может быть важно, поскольку резисторы выделяют значительное количество тепла.Комбинацию коммутационного устройства и схемы управления обычно называют «модулем прерывателя», а резистор — «резистором динамического торможения». Динамические тормоза обычно рассчитаны на рабочий цикл в диапазоне 20 процентов, а прерыватели часто используются в более тяжелых условиях.

Упрощенная схема цепи динамического торможения.
Изображение предоставлено: Rockwell Automation, Inc.
Существует два типа управления динамическим торможением: управление гистерезисом и управление ШИМ (широтно-импульсной модуляцией).При гистерезисном управлении схема управления отслеживает уровень напряжения на шине постоянного тока и включает транзистор, когда напряжение достигает заданного уровня, чтобы избежать сбоя из-за перенапряжения в приводе. Когда ток течет к резистору, энергия превращается в тепло, что вызывает уменьшение постоянного напряжения. Когда напряжение падает до заданного «низкого» уровня, транзистор отключается.
Если управление гистерезисом включает транзистор и оставляет его включенным до тех пор, пока напряжение не упадет до заданного уровня, управление ШИМ включает и выключает резистор в соответствии с уровнем напряжения шины постоянного тока.В общем, методы гистерезисного и ШИМ-управления эквивалентны по функциям, но ШИМ-управление предпочтительнее для приложений с общей шиной постоянного тока, поскольку это помогает избежать ситуации, когда один привод выполняет непропорциональную долю работы динамического торможения.

Соединение шины постоянного тока между
двумя частотно-регулируемыми приводами через плавкие соединения делает
одной простой формой общей шины. Привод
увеличенного размера обеспечивает выпрямление переменного тока в постоянный.
Изображение предоставлено: Yaskawa America
В общей шине постоянного тока один выпрямитель подает питание на шину постоянного тока для всех инверторов постоянного тока в переменный, а не на отдельный выпрямитель в каждом приводе переменного тока.
Динамическое торможение или регенерация?
Динамическое торможение используется, когда необходимо периодически рассеивать энергию, а регенерация обычно предпочтительна, когда двигатель часто работает как генератор. С точки зрения приложения, капитальный ремонт нагрузок (состояние, при котором нагрузка движется со скоростью, превышающей заданную скорость двигателя), таких как конвейеры и краны, приводит к непрерывной выработке энергии и делает восстановление и повторное использование более рентабельным. Но приложения, в которых скорость замедления меняется, например вентиляторы, подходят для динамического торможения.В то время как регенерация снижает потребление энергии, динамическое торможение снижает износ тормозных компонентов, которые зависят от трения. И хотя энергия теряется в виде тепла при динамическом торможении, ее первоначальная стоимость значительно меньше, чем у рекуперативных приводов.
,Все аспекты торможения двигателем
Вот краткая информация о том, как происходит торможение двигателем в бензиновых и дизельных двигателях, а также о том, где его можно использовать!
Искусство торможения двигателем может быть либо помощью, либо помехой при вождении, используя всасывание, удар и удар внутреннего сгорания в обратной форме.Торможение двигателем, наблюдаемое при остановке ускорения и при 0% дроссельной заслонке, может использоваться для максимального замедления автомобиля в тандеме с тормозами. Торможение двигателем может сделать движение накатом при выключенной дроссельной заслонке немного неприятным, поскольку оно снижает вашу скорость на дороге со скоростью, которая требует дальнейшего увеличения газа на дороге. Но у него есть свои применения, поэтому давайте посмотрим, как происходит торможение двигателем и как оно работает в бензиновых и дизельных двигателях.
Тормозная система бензиновым двигателем
Видео на YouTube-канале Morozov AutomotiveВ простейшей форме торможение двигателем происходит в бензиновом двигателе при отпускании дроссельной заслонки.При нажатии педали дроссельной заслонки на впуске двигателя открываются дроссельные заслонки, позволяя воздуху поступать во впускной коллектор и смешиваться с топливом для сгорания. Таким образом, когда дроссельная заслонка отпускается, эта дроссельная заслонка закрывается, пропуская лишь очень небольшое количество воздуха к двигателю.
Это внезапное закрытие воздуховода создает разрежение во впускном коллекторе, которое создает силу, противоположную поршням, совершающим возвратно-поступательное движение внутри двигателя. Представьте, что вы кладете палец на конец футбольного насоса, а затем пытаетесь переместить поршень вверх — большая противодействующая сила, создаваемая вакуумом внутри цилиндра, будет означать, что поршень откачки вообще не будет сильно сдвигаться.
Во впускном коллекторе создается разрежение после закрытия дроссельной заслонки.Усилие, которое поршни должны прилагать, чтобы противодействовать вакууму в коллекторе, отбирает энергию их возвратно-поступательного движения, заставляя их замедляться и, таким образом, вращать коленчатый вал медленнее, уменьшая скорость движения.Это торможение, таким образом, усиливается при высоких оборотах двигателя, поскольку большое количество воздуха, ранее входившего в цилиндры, внезапно отключается, создавая вакуум, который противодействует более высокой силе вращения от цилиндров.
Помимо вакуумного элемента, минимальное торможение двигателем также достигается за счет трения между движущимися частями двигателя. Хотя масляная система обеспечивает более чем подходящее количество смазки, чтобы движущиеся компоненты не сваривались друг с другом из-за тепла, между каждой движущейся частью двигателя возникает естественное трение, поскольку они взаимодействуют друг с другом.Это трение отрицательно влияет на положительную энергию движущегося двигателя, тем самым снимая энергию вращения с коленчатого вала и «тормозя» двигатель.
Торможение дизельным двигателем
К сожалению, в дизельных двигателях нет дроссельной заслонки, поэтому вместо них используется выпускной клапан, который закрывается во время такта выпуска двигателя.Затем создается противодавление, которое сопротивляется движению поршней, замедляя их.
Другой метод, используемый в дизельных двигателях, — это так называемый джейк-тормоз; это устройство, которое использует коромысло для открытия выпускного клапана в верхней части такта сжатия, что позволяет небольшому количеству воздуха уходить вниз по выпускному коллектору вместо того, чтобы полностью сжаться и затем воспламениться. Это приводит к снижению объемного КПД двигателя и, следовательно, к снижению мощности.Несмотря на эти два метода, дизельные двигатели гораздо более эффективны при движении накатом без дроссельной заслонки из-за отсутствия обратной силы, действующей на поршни, по сравнению с мощным вакуумом, создаваемым в бензиновом двигателе.
Тормоза Jake популярны на больших транспортных средствах, и иногда их можно запретить из-за шума, который они создают во время торможения двигателем.Видео через аккаунт YouTube stealthwavef22raptor
Торможение двигателем имеет свои реальные преимущества, одним из которых является безопасность на дороге. Эта дополнительная тормозная сила всегда помогает автомобилю замедляться быстрее и — при регулярном целенаправленном использовании — показывает, что водитель осознает свое окружение и сознает возможности и поведение своего автомобиля. Ваши тормозные колодки и диски также будут вам благодарны в долгосрочной перспективе, так как они должны уменьшать скорость, чем если бы сцепление было выключено, и вся тормозная сила изолирована от ваших тормозов.
Другой сценарий, в котором есть свои преимущества, — это когда земля покрыта снегом. Вместо внезапного торможения, которое может вызвать внезапную потерю трения между шинами и дорогой, можно использовать торможение двигателем для более плавного снижения скорости.
В следующий раз, когда вы отправитесь в путь, попробуйте хорошо продуманное торможение двигателем, чтобы дать им отдохнуть!Торможение двигателем может напоминать искусство, если вы полностью осознаете дорогу впереди, и может быть реализовано в повседневном вождении с некоторой концентрацией и здравым смыслом.Хотя в некоторой степени это показывает, что двигатель внутреннего сгорания по своей природе работает против самого себя, хорошо знать, что у вашей силовой установки есть потенциальная рука помощи, которую можно протянуть вам в случае необходимости. И, честно говоря, если у вас довольно массивная выхлопная система, нет ничего лучше, чем перекрыть подачу воздуха в двигатель простым нажатием на дроссельную заслонку, позволяя оборотам медленно снижаться, постепенно уменьшаясь с треском и треском.
,Два основных метода, используемых для торможения двигателя
Торможение двигателя
Два общих основных метода, используемых для торможения двигателя, — это торможение постоянным током и динамическое торможение. Мы рассмотрим оба аспекта подробно, начиная с электрического торможения.

- Торможение впрыском постоянного тока
- Динамическое торможение
1. Торможение постоянным током впрыском
Торможение постоянным током — это метод торможения, при котором постоянный ток (DC) подается на неподвижные обмотки двигателя переменного тока после того, как напряжение переменного тока снято.Это эффективный и действенный метод торможения большинства двигателей переменного тока.
Торможение постоянным током обеспечивает быстрое и плавное торможение при всех типах нагрузок, включая высокоскоростные и высокоинерционные.
Напомним, что противоположные магнитные полюса притягиваются, а аналогичные магнитные полюса отталкиваются. Этот принцип, применяемый как к двигателям переменного тока, так и к двигателям постоянного тока, является причиной того, что вал двигателя вращается на .


В асинхронном двигателе переменного тока, когда напряжение переменного тока снимается, двигатель останавливается по инерции в течение определенного периода времени, так как нет индуцированного поля, поддерживающего его вращение.Поскольку время выбега может быть неприемлемым, особенно в аварийной ситуации, можно использовать электрическое торможение для более быстрой остановки.
При подаче напряжения постоянного тока на неподвижные обмотки после отключения переменного тока в статоре создается магнитное поле, которое не меняет полярность .
В свою очередь, это постоянное магнитное поле в статоре создает магнитное поле в роторе. Поскольку магнитное поле статора не меняет полярность, он будет пытаться остановить ротор, когда магнитные поля выровнены (N к S и S к N).
Демонстрация торможения инжекторным двигателем постоянного тока (ВИДЕО)
Единственное, что может предотвратить остановку ротора при первом выравнивании , — это инерция вращения нагрузки, подключенной к валу двигателя. Однако, поскольку тормозное действие статора присутствует постоянно, двигатель тормозится быстро и плавно до полной остановки.
Поскольку нет деталей, которые вступают в физический контакт во время торможения, техническое обслуживание сведено к минимуму .
Вернуться к методам торможения ↑
2. Динамическое торможение
Динамическое торможение — еще один метод торможения двигателя. Это достигается, , повторным подключением работающего двигателя к работе в качестве генератора сразу после его выключения , быстро останавливая двигатель. Генератор преобразует механическую энергию вращения в электрическую, которая может рассеиваться в виде тепла в резисторе.
Может потребоваться динамическое торможение двигателя постоянного тока , потому что двигатели постоянного тока часто используются для подъема и перемещения тяжелых грузов, остановить которые может быть трудно. .
Должен быть доступ к обмоткам ротора для повторного подключения двигателя к работе в качестве генератора. В двигателе постоянного тока доступ осуществляется через щетки на коммутаторе.
В этой схеме выводы якоря двигателя постоянного тока отсоединены от источника питания и сразу же подключены через резистор, который действует как нагрузка. Чем меньше сопротивление резистора, тем выше скорость рассеивания энергии и тем быстрее двигатель замедляется.


Обмотки возбуждения двигателя постоянного тока остаются подключенными к источнику питания.Якорь генерирует напряжение, называемое «противодействующей электродвижущей силой» (CEMF) . Эта CEMF заставляет ток течь через резистор и якорь. Ток заставляет тепло рассеиваться в резисторе, забирая энергию из системы и замедляя вращение двигателя.
Сгенерированная CEMF уменьшается по мере уменьшения скорости двигателя. Когда скорость двигателя приближается к нулю, генерируемое напряжение также приближается к нулю. Это означает, что тормозное действие уменьшается по мере уменьшения скорости двигателя.
В результате двигатель не может быть полностью остановлен с помощью динамического торможения. Динамическое торможение также не может удерживать груз после его остановки , потому что больше не действует торможение.
По этой причине электромеханические фрикционные тормоза иногда используются вместе с динамическим торможением в приложениях, которые требуют удержания нагрузки, или в приложениях, где требуется остановить большую тяжелую нагрузку . Это похоже на использование парашюта для замедления гоночного автомобиля перед нажатием на тормоза.
Для динамического торможения двигателей переменного тока можно использовать преобразователь частоты.
Вернуться к методам торможения ↑
Ссылка // Основы двигателей и управления двигателями Eaton
,Что такое торможение двигателем?
Большинство из нас, вероятно, знакомы с термином «торможение двигателем», но задумывались ли вы когда-нибудь о том, как оно работает?
Некоторые из вас, кто немного более склонен к механике, вероятно, имеют довольно хорошую идею, но на самом деле существует 3 различных метода торможения двигателем, которые можно использовать в зависимости от автомобиля. Чаще всего торможение двигателем используется на больших грузовых автомобилях или транспортных средствах, которые в противном случае было бы трудно замедлить с помощью роторных тормозов.
Однако существует метод торможения двигателем в бензиновых двигателях, а также два других метода для дизельных двигателей. По сути, торможение двигателем использует тормозящие силы внутри двигателя (трение, сжатие и т. Д.), Чтобы замедлить движение ротора и, как следствие, автомобиля. Вы можете ознакомиться с подробным объяснением всех видов торможения двигателем в видео ниже с YouTube Channel Engineering Explained.
Первый метод, который следует обсудить, — это торможение бензиновым двигателем, которое использует образование вакуума для замедления транспортного средства.Когда вы отпускаете ногу с дроссельной заслонки, корпус дроссельной заслонки закрывается, а это означает, что по мере того, как поршни втягиваются в цилиндры, образуется небольшой вакуум, создавая силы, которые препятствуют дальнейшему движению автомобиля.
Первый дизельный метод действует прямо противоположно созданию вакуума, а скорее создает избыточное сжатие в цилиндре. Когда поршень движется вверх, чтобы вытолкнуть выхлоп, выпускной клапан закрывается, создавая противодавление в цилиндре, тем самым замедляя автомобиль.
Последний дизельный метод торможения двигателем немного сложнее, и он получил название «джейк-тормоз» в честь компании, создавшей его.Видео выше объясняет этот метод лучше всего, но, по сути, вы ослабляете часть сжатия, накопленного в двигателе, поэтому оно не так эффективно при перемещении поршней.
Вы «тратите энергию» на процесс горения, просто сжигая газы, а затем немедленно их выпуская, что приводит к отрицательной сети. Для правильной работы каждой из этих систем используется довольно много клапанов и соленоидов, и все они синхронизированы и регулируются идеально, чтобы все работало.
Надеюсь, теперь вы немного лучше разбираетесь в торможении двигателем и сможете произвести впечатление на своих друзей-не инженеров, узнав, как автомобили могут замедляться, не нажимая на тормоза.
.